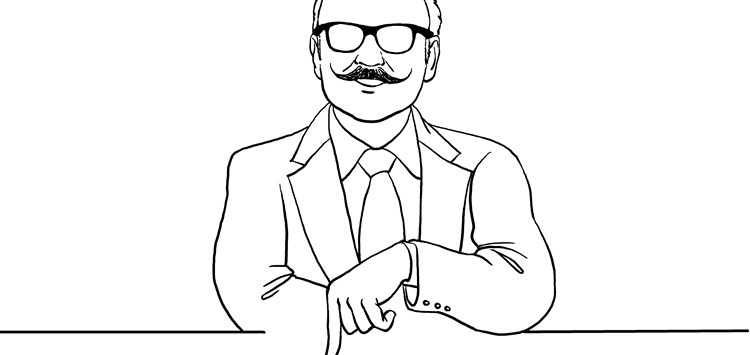
(Bild: ISGATEC GmbH)
08.06.2022 „FIPG und FIPFG sind spannende Akronyme"
Seit es industriell gefertigte und damit ausreichend verfügbare Elastomere gibt, wurden Zuschnitte daraus als Dichtungen in Gehäuse eingeklebt, wobei die Klebung meist als Montagehilfe oder „Verlierschutz“ diente.
Denn die verschlossenen Gehäuse hielten die Dichtungen ohnehin in situ, also am Platz. Bis in die späten 80er war das „Stand der Technik“, wenngleich es schon erste Anwendungen von FIPG-Dichtsystemen gab. Dabei wurde die Dichtung vor Ort geformt – formed in place gasket – indem ein pastöser Dichtstoff vor dem Fügen auf einen Flansch aufgetragen wurde, der vor oder nach dem Fügen chemisch vernetzte und so eine elastische Dichtung formte. Dieser Prozess konnte mechanisiert oder gar automatisiert werden, sparte also Handarbeit beim Einkleben der separat gefertigten Dichtelemente. Vor allem vermied dieses Verfahren aber Müll, der zwangsläufig beim Ausschneiden bzw. Ausstanzen der Dichtung zuvor entstanden war. Außerdem konnten so auch dreidimensionale Dichtungen geformt werden, was zuvor durch das Einlegen oder Einkleben von Elastomerrundschnüren erledigt wurde. Perfekte Lösung?
Noch nicht ganz: Das pastös aufgebrachte Dichtmaterial musste noch vor dem Fügen aushärten – etwa um das Gehäuse später wieder öffnen zu können. Damit war es aber oft, z.B. für dünnwandige Gehäuse, schon zu fest. Die Gehäuse wurden und werden aus Gewichts- und Materialersparnisgründen immer dünner. Deshalb folgte mit dem FIPFG die nächste Entwicklungsstufe, wobei das 2. F für „foamed“ steht. Auch hier wird eine flüssige bis pastöse Masse in einer Raupenform aufgebracht. Durch die anschließende Reaktion, die hier auch ein Aufschäumen beinhaltet, entsteht eine weiche, gut verpressbare Dichtung. Daher rührt letztlich auch der Name Formed In Place Foam Gasket, abgekürzt FIPFG. Die Schaumdichtung („foam gasket“) wird direkt („in-place“) am abzudichtenden Bauteil aufgebracht („formed“). Der größte Vorteil dieser Technologie liegt vor allem im maschinellen und damit kostengünstigen Auftragsprozess, denn das Auftragen des Dichtschaums geschieht entweder per Roboter oder über ein Mehrachsen-Auftragssystem. Auch die Zu- und Abführung der abzudichtenden Bauteile kann mechanisiert oder gar automatisiert werden. Damit fallen die Vorfertigung der Dichtung, das manuelle Einlegen oder Einkleben weg – die Dichtung entsteht am Einsatzort und passt damit perfekt und haftet von sich aus auf dem Untergrund. Der Spruch „sitzt wie angegossen“ passt hier im wahrsten Sinne des Wortes! Das spart Zeit und Geld – und wenn man dann noch das richtige Material wählt, kann man sich unter Umständen sogar die Dichtnut zur Aufnahme der Dichtung sparen. Warum? Weil es nicht nur dünnflüssige FIPFG-Systeme gibt, die gut in enge Nuten fließen, sondern auch pastöse, die einfach auf ebene oder schräg geneigte Flächen aufgetragen werden können. Das abzudichtende Bauteil kann damit oft konstruktiv vereinfacht werden. War das ein Fortschritt?
Aber ja doch! Und es ist außerdem ein schönes Beispiel dafür, dass die Hersteller von Dichtmaterialien sowie Misch-, Dosier- und Auftragstechnik eng zusammenarbeiten müssen, damit das System dann auch reibungsfrei läuft. Auf der Anwenderseite sorgen idealerweise Konstruktion, Anlagenplanung, Qualitätssicherung, Einkauf und Produktion für einen optimalen Projektverlauf. Erfolgreicher technischer Fortschritt – hier mal zur Vermeidung des Klebens – ist immer Teamwork.
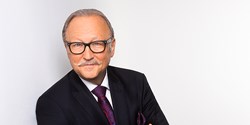
„Auch wenn Fortschritt nur mit einem Buchstaben beschrieben werden kann, heißt das nicht, dass nicht eine Menge zu berücksichtigen wäre.“ Thomas Stein, Inhaber, IMTS Interims Management