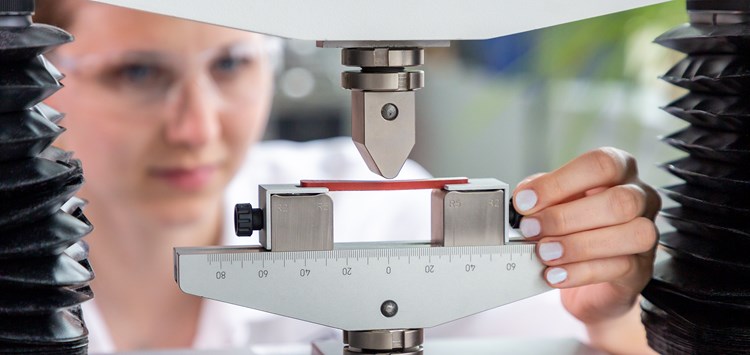
Es wurden Grundlagen geschaffen, um den aktuell betriebenen Scale-up zur Herstellung dieser Siliconharze in drei Stufen durchführen zu können – vom Labor über den Technikumsmaßstab bis zum großtechnischen Prozess (Bild: WACKER)
06.12.2022 Neue Wege zu hochtemperaturstabilen Polymer-Bauteilen
Mit einer neuen Technologie von Wacker können mechanisch belastbare Kunststoff-Formteile produziert werden, die dauerhaft Temperaturen bis zu 220 °C widerstehen.
Ausgangspunkt sind zwei alternativ verwendbare Siliconharz-Bindemittel: SILRES® LR 700 oder POWERSIL® Resin 700. Anwendende können es mit eigenen Füllstoffen und Vernetzern einsetzen. Oder sie greifen zum gebrauchsfertigen Silicon-Formstoff POWERSIL® Resin 710, um daraus durch Pressformen, Druckgelieren oder Spritzgießen Formteile der Wärmeklasse R herzustellen.
Siliconharze zur Herstellung von Formteilen, die auch bei sehr hohen Temperaturen stabil und mechanisch hochbelastbar sind und elektrisch isolierende Eigenschaften besitzen, werden bereits seit längerem industriell eingesetzt. Derartige anspruchsvolle Formteile werden z.B. in der elektrischen Isoliertechnik für zukünftige innovative Anwendungen benötigt – etwa für Elektroautos, um deren Nabenmotoren zu schützen. Der Herstellprozess für solche Bauteile ist jedoch aufwändig. Bislang stellen die Verarbeiter zunächst halbfertige Teile her, indem sie Vorprodukte mit Siliconharz-Bindemitteln laminieren und diese dann nachträglich bearbeiten, um sie in Form zu bringen. Laminate aus Siliconharz und Glas- oder Kohlefaser zu fertigen, sie zu verpressen und dann mechanisch zu bearbeiten, bedeutet aber viel Aufwand und produziert viel Verschnitt und viel Abfall.
Eine direkte, weniger aufwändige Formgebung – etwa durch Spritzgießen – scheiterte bislang sowohl an geeigneten Bindemitteln als auch an den ungenügenden mechanischen Eigenschaften der ausgehärteten Siliconharzmassen. Und konkurrierende Werkstoffe mit einer ähnlichen Hitzebeständigkeitsklasse, wie PTFE (Polytetrafluorethylen) und PEEK (Polyetheretherketon), sind kompliziert zu verarbeiten oder es mangelt ihnen an den nötigen Duroplast-Eigenschaften.
Mit SILRES® LR 700 bzw. POWERSIL® Resin 700 rückt nun auch für hochtemperaturbeständige Formteile eine effiziente und kostengünstige Verarbeitung in Reichweite. Mit diesen beiden Siliconharzen bringt Wacker Werkstoffe auf den Markt, die ähnlich leicht zu verarbeiten sind wie z.B. Polyurethan- oder Epoxidharze und die in der Produktion thermisch geringer beanspruchter Bauteile weit verbreitet sind.
Gefordert war ein flüssiges, leicht zu handhabendes Siliconharz mit ausgeprägter Hitzebeständigkeit, das zudem relativ reaktiv sein sollte. Hier ist es gelungen, Phenylgruppen in das Polysiloxangerüst einzubauen. Dadurch reduziert sich die Sprödigkeit der ausgehärteten Siliconformteile deutlich. Für hohe mechanische Festigkeiten sorgen wiederum entsprechende Füllstoffe. In zahlreichen Versuchsreihen mit hochdisperser Kieselsäure, Quarz und Glasfasern hat man eine erste optimierte Füllstoffmischung entwickelt. Das flüssige Siliconharz, die Füllstoffmischung und ein Peroxid als Vernetzer bilden die Bestandteile des compoundierten POWERSIL® Resin 710 – ein Angebot an Anwendende, die auf eine gebrauchsfertige Materiallösung zugreifen möchten.
Die neue Siliconharz-Technologie ist zugleich eine vorteilhafte Alternative zu hochtemperaturfesten Polymeren wie PTFE und PEEK. So lässt sich z.B. PTFE nicht per Spritzguss verarbeiten, sondern muss gepresst oder bei Temperaturen von >360 °C gesintert werden. Ähnlich hoch liegen die Temperaturen beim Spritzguss von PEEK. Die Vernetzung des Siliconharzes im POWERSILR Resin 710 läuft dagegen schon bei rd. 160 °C ab.
Um die thermische Belastbarkeit von Formteilen aus POWERSIL® Resin 710 zu ermitteln, wurden die Proben bei verschiedenen Temperaturen eingelagert. Später wurde gemessen, wie sich die Masse des Bindemittels mit der Zeit und abhängig von der Lagertemperatur prozentual veränderte. Nach einem standardisierten rechnerischen Verfahren wurde daraus die Wärmeklasse als Maß für die Dauergebrauchstemperatur extrapoliert. Das Ergebnis dieses beschleunigten thermischen Alterungsverfahrens: Die aus diesen Siliconharzen hergestellten Formteile erfüllen die Anforderungen an die Wärmeklasse R, halten also Temperaturen von bis zu 220 °C stand. Man testete außerdem das Verhalten von Probekörpern aus POWERSIL® Resin 710 bei häufigen Deformationen. Bei diesen Probekörpern handelt es sich um 8 cm lange, 1 cm breite und 4 mm dicke Stäbchen, die nur an ihren zwei Enden aufliegen. Der Dorn einer Testapparatur drückt mit definierter Kraft auf die Mitte der Stäbchen – immer und immer wieder. Das Resultat: Bei sehr starker Verformung hält das Material mehrere Hundert Zyklen aus, bei schwacher Verformung viele Zehntausend.
Die neuen Bindemittel enthalten reaktive Doppelbindungen, die in Gegenwart eines Katalysators vernetzende Ethylenbrücken bilden. Anwendende, die mit den neuen flüssigen Siliconharz-Bindemitteln eine eigene Technologie zur Produktion von Formteilen aufbauen möchten, können neben der Vernetzung mit Peroxiden auch eine Additionsvernetzung in Betracht ziehen, wie man sie typischerweise bei Flüssigsiliconkautschuk anwendet. Eine solche Verarbeitungstechnologie bietet zwei Vorteile: Sie lässt sich bei niedrigeren Temperaturen einsetzen und die Geschwindigkeit, mit der das Harz vernetzt, kann durch Variation der Temperatur reguliert werden.
Wie immer bei solchen Produktentwicklungen beginnt man mit einem Batchansatz im Labormaßstab, um erste Muster für interne Tests und für potenzielle Kunden zu generieren. Angesichts des sehr positiven Feedbacks, das die Entwickler:innen intern wie extern auf das Eigenschaftsprofil der beiden Siliconharz-Bindemittel erhielten, stellt sich nun die Herausforderung, möglichst schnell ein kontinuierliches Herstellungsverfahren zu entwickeln. Der Fokus liegt nun darauf, mittels eines kontinuierlichen Prozesses, auch in der Phasentrennung und der Produktwaschung, ein effizientes Herstellungsverfahren zu ermöglichen. Da sich der Mengendurchsatz, gemessen in produzierten Kilogramm pro Stunde, gegenüber einem Batchansatz sehr deutlich erhöht – um den Faktor fünf bis zehn – profitieren auch zukünftige Anwendende von einem solchen sauber skalierten Prozess.