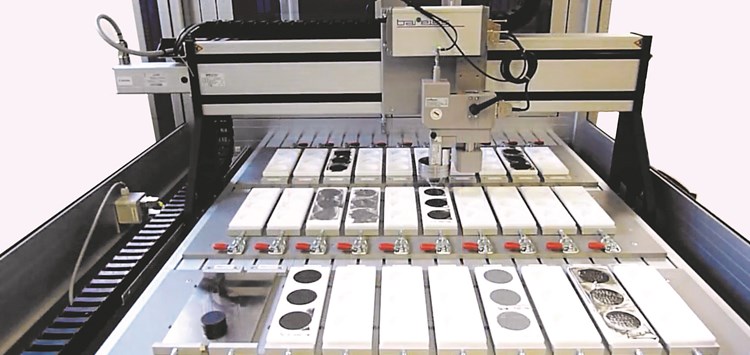
digi test II Portal mit teilweise bestückten Werkstückträgern (Bild: Bareiss Prüfgerätebau GmbH)
17.09.2018 Prozesskosten minimieren
Neues System zur Bestimmung des Aushärteverhaltens von Dichtmaterialien
Warum ist es für Hersteller von Dichtstoffen wichtig, das Aushärteverhalten ihrer Produkte genau u kennen? Zum einen ist dieses Aushärteverhalten für die Verarbeitung des Materials notwendig, zum anderen stellt sich die Frage, wann das Produkt weiterverarbeitet werden kann. In Zusammenarbeit mit einem Anwender wurde ein neues Verfahren entwickelt, das signifikant Kosten spart.
Das Bestimmen dieser materialspezifischen Eigenschaften war in der Vergangenheit recht aufwändig. Um das Aushärteverhalten genau charakterisieren zu können, war die Aufnahme von vielen Härte-Messwerten notwendig. Dies überstieg i.d.R. den Zeitraum eines normalen Arbeitstages. In der Vergangenheit konnte der Mitarbeiter am nächsten Morgen zwar direkt weitermessen, um die Aushärtekurve zu vervollständigen. Allerdings konnte der Messverlauf nicht konsequent nachvollzogen werden, da keine lückenlosen Messdaten vorhanden waren. In diesem Fall gab es die Möglichkeit, die Aushärtekurve mathematisch zu vervollständigen und so die kritische Härte zu bestimmen. Dies war allerdings nur mit aufwändigen Algorithmen möglich und stellte eben keine echt gemessenen Werte dar.
Ein neuer Ansatz
Die Geschäftseinheit Oberflächentechnik des Unternehmensbereichs Coatings der BASF, die unter der Marke Chemetall agiert, hat deshalb einen neuen Prozess entwickelt. Gemeinsam mit der Bareiss Prüfgerätebau GmbH wurden in enger Zusammenarbeit ein detailliertes Pflichtenheft erstellt und Tests mit den Materialien durchgeführt. Aus Machbarkeitsstudien hat sich so das von Bareiss entwickelte „Shore-A-Verfahren“ zur Messung an Formteilen herauskristallisiert. Die Idee bestand darin, eine Messmaschine (Bild 1) zu entwickeln, die viele verschiedene Proben in unterschiedlichen Zeitintervallen wiederkehrend mannlos misst und das echte Aushärteverhalten aufnimmt und darstellt. Die daraus entstandenen Anforderungen beziehen sich auf die automatische Vermessung von bis zu 28 Werkstückträgern, wobei jeder Werkstückträger wiederum aus einer bis drei Proben besteht. Jeder Probekörper muss selbstverständlich auch normkonform vermessen werden. Das bedeutet, die Messmaschine darf jede Position nur einmal anfahren. Der Abstand, den die Messpositionen zueinander haben müssen, beträgt – laut DIN ISO 7619-1 – 6 mm, wobei der Abstand zur Außenkante 12 mm nicht unterschreiten darf. Aus diesen Vorgaben und der gegebenen Probengeometrie ergeben sich 34 Messpunkte pro Probekörper. Diese Messpunkte werden in zeitlichen Abständen bezüglich ihrer Härte geprüft. Außerdem wird der Härteverlauf graphisch dargestellt.
Einfache Bedienung
Der Bediener hat die Möglichkeit, zum Auftragskopf die Anzahl der Probekörper, den Anmischzeitpunkt und die Verzögerung bis zur erstmaligen Messung des Materials einzugeben. Zudem können ein Härtezielwert (bei dessen Erreichen auch die Option eines automatischen Stopps gegeben ist), das Messintervall, die Messzeit und die Messpunkte eingestellt werden. Diese Parameter können sowohl händisch eingegeben als auch in einer Vorlage gespeichert und später wieder geladen werden. Der Auftrag wird nun eingelastet und entsprechend seiner zeitlichen Abfolge eingegliedert. Die Messmaschine arbeitet die Aufträge chronologisch ab, gibt die jeweilige Härteverlaufskurve graphisch aus und stellt die vorher definierten Messwerte (bis zu fünf Stück) in einer Messwerttabelle dar. Diese Messwerttabellen können später überprüft und anschließend in einer .csv-Datei exportiert werden. Der Auftragsfortschritt kann in mehreren Ansichten kontrolliert werden – durch farbliche Codierung auf der Übersichtsseite, durch Aufruf der Auftragsliste (in der die chronologische Abfolge sichtbar wird) oder auch durch einen Blick auf den Ergebnisbereich (im rechten Teil des Bildschirms – hier lassen sich Härteverlaufe, Messwerttabellen und Aushärteverläufe ansehen).
Die Messmaschine bietet zusätzlich die Möglichkeit, eine einzelne Probe zu messen. Hierfür wird der automatische Ablauf unterbrochen und der manuelle Messplatz angefahren. Der Bediener kann Einzelprüfungen durchführen, sie elektronisch auswerten und exportieren. Steht während dieser manuellen Prüfung ein Auftrag aus der automatischen Messung an, wird der Bediener durch ein optisches und akustisches Signal 30 s vorher darauf hingewiesen, sodass er die Sicherheitsumhausung rechtzeitig schließen und den Automatikmodus reaktivieren kann. Kann der Bediener den automatischen Ablauf nicht rechtzeitig starten, reiht die Maschine alle anstehenden Aufträge in eine Warteschleife ein und arbeitet sie anschließend (bei Reaktivierung des Automatikmodus) nacheinander ab. Angezeigt wird der echte Zeitstempel der Messung, sodass eine Fehlinterpretation der Messwerte ausgeschlossen werden kann.
Erste Testergebnisse
Nach der Installation bei Chemetall wurden die Messmaschine und die Software ausgiebig getestet und in mehreren Schleifen iterativ verbessert. Kundenspezifische Zusatzanforderungen wurden von Bareiss vor Ort nachträglich umgesetzt. Somit wurde ein Stand erreicht, der dem Kunden nicht nur exakte Messwerte und damit essenzielles Wissen über sein Produkt liefert, sondern zudem auch noch eine Menge Zeit bei der Messung der Materialien spart. Auch der nachfolgende Prozess konnte durch den Einsatz dieser Messmaschine vereinfacht werden. Chemetall erzielt so signifikante Prozesskosteneinsparungen.
Fakten für Einkäufer
• Die vereinfachte Bestimmung des Aushärteverhaltens senkt die Kosten bei der Dichtmaterialherstellung
Fakten für Qualitätsmanager
• Verbesserte Qualität bei Dichtmaterialien durch effektive Prüfroutinen
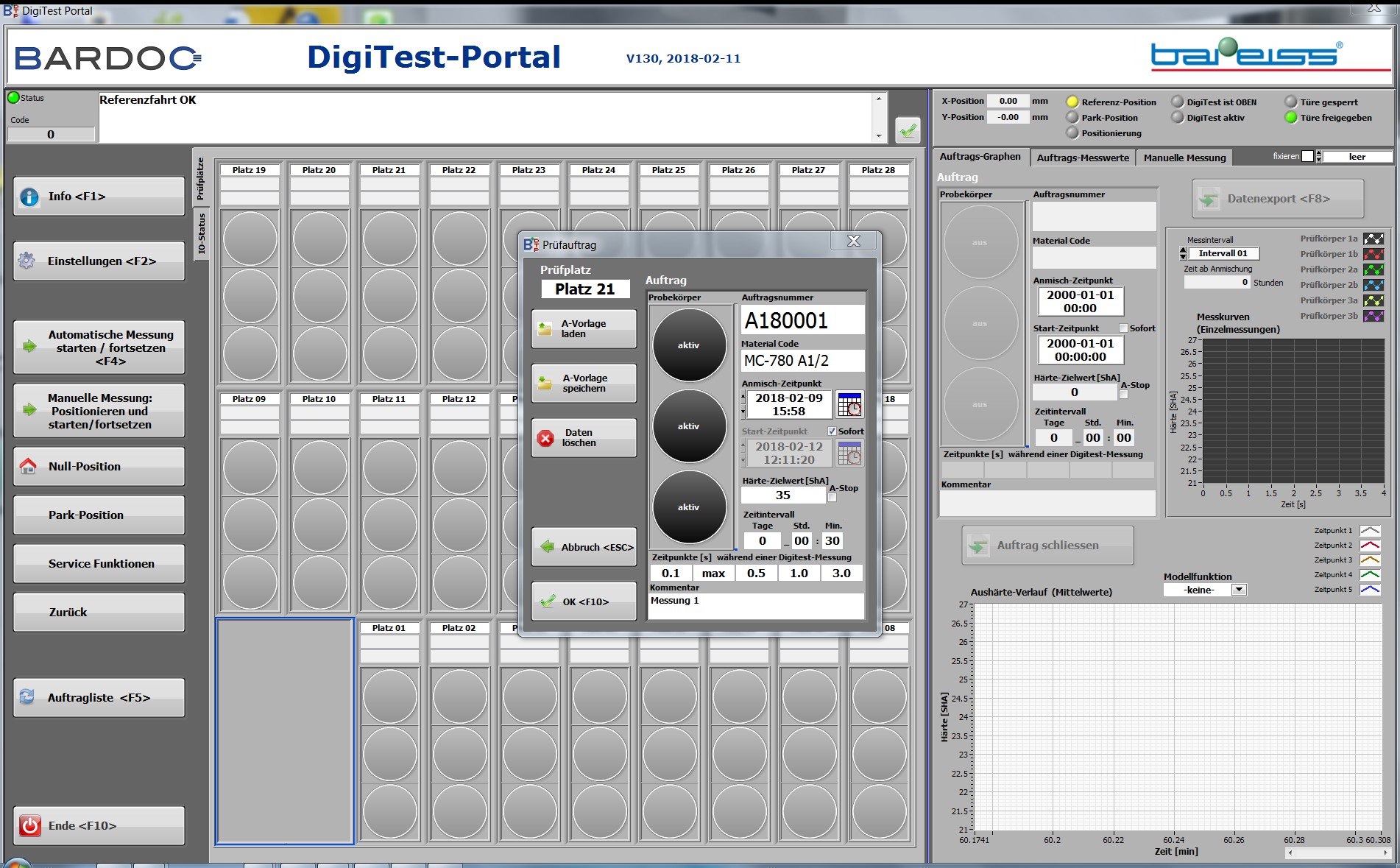
Eingabemaske zum Anlegen eines Prüfauftrages (Bild: Prüfgerätebau GmbH)
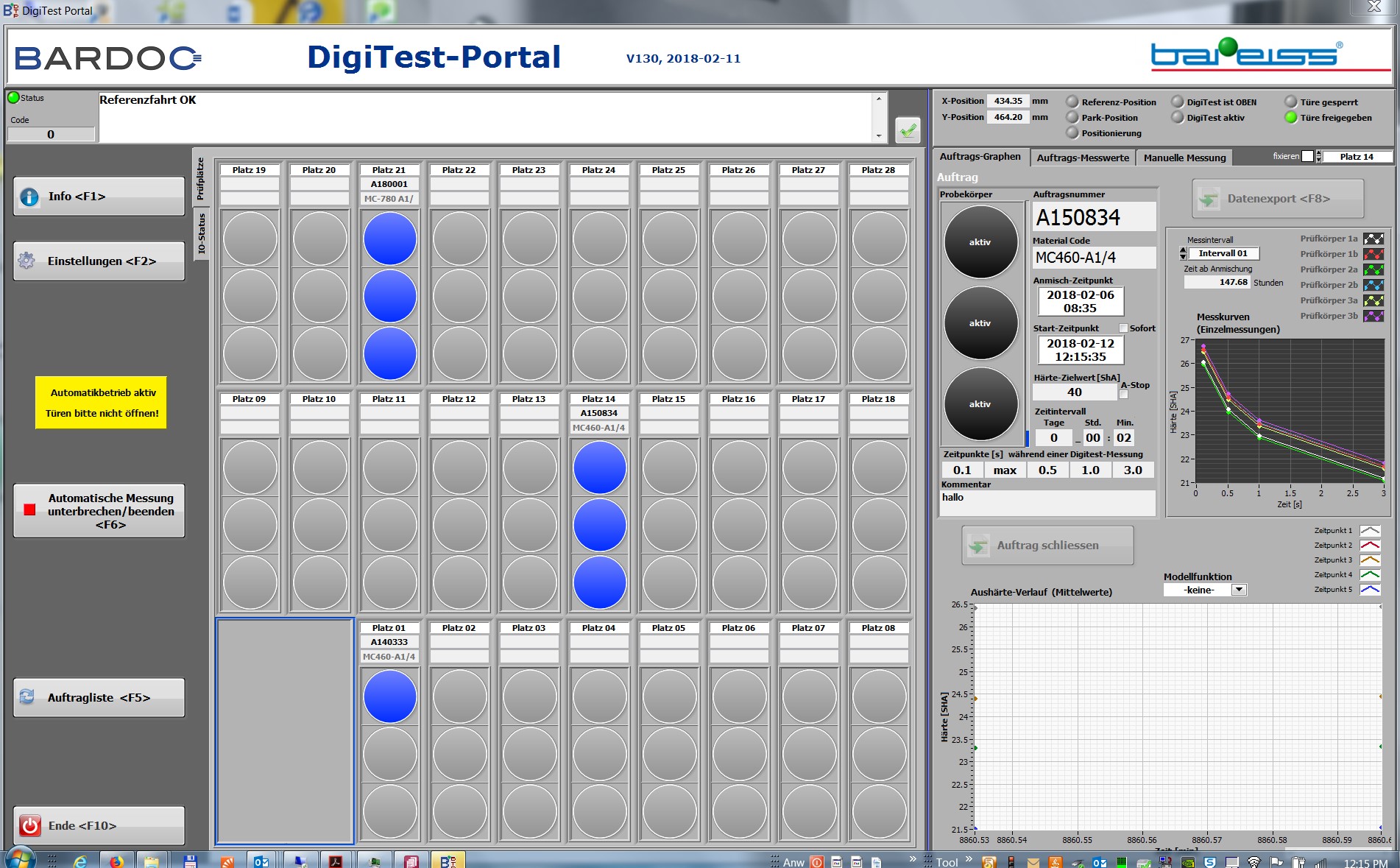
Benutzeroberfläche mit aktiven Aufträgen (blau hinterlegt) und Messwerten sowie Informationen (rechts) (Bild: Prüfgerätebau GmbH)