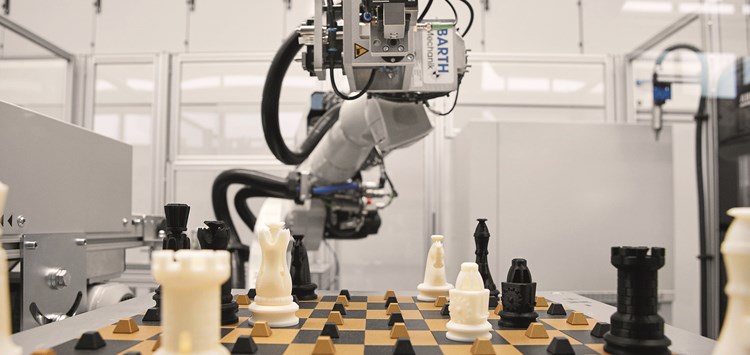
(Bild: ARBURG)
16.09.2019 Effektiver additiv fertigen
Komplexe, belastbare AM-Funktionsbauteile in Hart-Weich-Verbindung
Bei der additiven Fertigung ist die eingeschränkte Materialverfügbarkeit immer wieder ein Thema. Hier gibt es Bewegung. Neue Materialien und die Weiterentwicklung der Technik im Kontext zum vollautomatisierten industriellen Einsatz eröffnen derzeit permanent neue Anwendungsfelder.
Ein Alleinstellungsmerkmal des Arburg Kunststoff-Freiformens (AKF) mit dem Freeformer ist, dass die gleichen Kunststoffgranulate verwendet werden können wie für das konventionelle Spritzgießen. Der neue Freeformer 300-3X mit drei Austragseinheiten (Bild 1) ermöglicht die industrielle additive Fertigung komplexer Funktionsbauteile aus Originalmaterial in belastbarer Hart-Weich-Verbindung mit Stützstruktur. Ein weiterer Anwendungsschwerpunkt für das Verfahren sind Funktionsbauteile und weiche Produkte, wie z.B. Dichtungen aus thermoplastischen Elastomeren (TPE). Im AKF-Verfahren lassen sich die Bauteileigenschaften gezielt beeinflussen. Die Anwender können mit dem offenen System auf die Materialdatenbank von Arburg zugreifen oder ihre eigenen Kunststoffe verarbeiten und die Prozessführung selbst optimieren.
Verarbeitung von qualifiziertem Originalmaterial
Der Freeformer eignet sich für Anwendungen in der Medizintechnik sowie für Vorserienteile, funktionale Ersatzteile, individuell gefertigte Konsumgüter, Montagevorrichtungen und andere Betriebsmittel. Sehr weiche Materialien wie das FDA-zugelassene Original-TPE Medalist MD 12130H (Härte 32 Shore A) oder SEBS Cawiton PR13576 (Härte 28 Shore A) können derzeit nur im AKF-Verfahren verarbeitet werden, z.B. zu dichten Faltenbälgen oder Komponenten für Beatmungsmasken. Aus PCU (Bionate) entstehen Dauerimplantate, etwa für den Einsatz im Wirbelsäulen-Bereich. Auch für medizintechnische Geräte und Hilfsmittel zur OP-Vorbereitung ist das AKF-Verfahren prädestiniert.
Das Verfahren entwickelt sich
Ein Vorteil ist, dass sich über die Maschinenparameter auch die Größe sowie der Abstand der Tropfen zueinander – und damit die Dichte und der Füllgrad –beeinflussen lassen. Um eine hohe mechanische Festigkeit zu erreichen, beträgt der Füllgrad eines Bauteils im Idealfall 100 %. Durch eine Änderung des Formfaktors, also des Verhältnisses von Tropfenbreite zu Höhe (B/H), können bei gleichbleibenden Parametern der Füllgrad eines Bauteils gezielt verändert und damit die mechanischen Eigenschaften variiert werden. Bei TPE resultieren daraus z.B. unterschiedliche Shore-Härten. Auch innerhalb eines Bauteils lassen sich verschiedene Materialdichten realisieren. Ein Testkörper mit Wabenstruktur demonstriert, wie sich solche TPE-Bauteile, z.B. für den Leichtbau oder für Filterelemente, einsetzen lassen. Am Beispiel einer „Spidermembran“ wurde gezeigt, dass das Bauteil reißfest und dicht ist, obwohl es nur aus zwei Schichten TPE besteht.
Erweitertes Anwendungsspektrum
Mit dem Freeformer 300-3X lassen sich ganz neue Anwendungen erschließen. Die Bezeichnung „3X“ steht für die drei in x-, y- und z-Richtung beweglichen Achsen des Bauteilträgers und „300“ für die auf der Bauplatte zur Verfügung stehende Fläche in Quadratzentimetern. Diese ist um knapp 50 % größer als beim Freeformer 200-3X. Der Bauraum bietet Platz für größere Kleinserien und Teile mit Abmessungen von bis zu 234 x 134 x 230 mm. Optional ist ein geschlossenes Kühlsystem mit industrietauglichem Kühlwasseranschluss erhältlich. Damit lassen sich Materialien bei Bauraumtemperaturen von bis zu 200 °C verarbeiten.
Ein Bauteilbeispiel, das aus drei Komponenten in belastbarer Hart-Weich-Verbindung additiv gefertigt wurde, sind bewegliche Greiferfinger aus ABS, TPE und Stützmaterial (Bild 2). Das Funktionsbauteil entsteht in einem Schritt und verfügt nach Entfernen des Stützmaterials über bewegliche Elemente – ohne zusätzlichen Montageaufwand.
Eine Anwendung für die Automobilindustrie sind Gehäusedeckel aus ABS mit weicher Dichtlippe aus elastischem TPE (Bild 3). Hier lassen sich die drei Austragseinheiten auch nutzen, um z.B. zwei Dichtmaterialien mit unterschiedlicher Shore-Härte je nach Bedarf zu verarbeiten und so, z.B. bei Produktwechseln, auf einen Materialwechsel zu verzichten.
Automatisierte industrielle additive Fertigung
Dank automatischen Öffnens und Schließens der Bauraumtür sowie optionalen Robot-Schnittstellen lässt sich der Freeformer automatisiert in vernetzte Fertigungslinien integrieren. Wie sich damit Vakuumgreifer vollautomatisch und zu 100 % rückverfolgbar funktionalisieren lassen, zeigt die „AM Factory“: Das Herzstück der IT-vernetzten Turnkey-Anlage ist ein Freeformer 300-3X, der auf Standard-Greiferplatten aus Aluminium additiv eine individualisierte 3D-Kontur aus dem TPU Desmopan 9370 aufbringt. Ein Sechs-Achs-Roboter übernimmt das Handling, inkl. Funktionsprüfung. Insgesamt werden sechs Varianten von Vakuumgreifern für Schachfiguren gefertigt. Für Dame, König, Läufer, Springer, Turm oder Bauer gilt es, die passende Geometrie zu ergänzen, um die Figur damit per Vakuum „greifen“ und bewegen zu können. Das Scada-System ATCM visualisiert die Anlagefunktionen und sammelt und übermittelt alle relevanten Prozess- und Prüfdaten. Der Datentransfer erfolgt über das Kommunikationsprotokoll OPC UA.
Ausblick
Der Markt der additiven Fertigung wächst rasant und bietet eine interessante fertigungstechnische Ergänzung zum Spritzgießen. Hinsichtlich der Branchen und Einsatzbereiche sind dem Freeformer und dem AKF-Verfahren kaum Grenzen gesetzt. Funktionsbauteile können aus Originalmaterial konstruiert und hergestellt werden, ohne die aus dem Spritzgießen bekannten fertigungstechnischen Restriktionen berücksichtigen zu müssen. Das erschließt ganz neue Anwendungen. Mithilfe von Stützmaterial lassen sich auch Hinterschnitte und komplexe Geometrien erzielen. Der Freeformer ermöglicht auch die Verarbeitung von thermoplastischen Elastomeren (TPE) sowie die additive Fertigung belastbarer Hart-Weich-Verbindungen. Zudem kann er vollautomatisiert in Fertigungslinien eingebunden und die Bauteile können lückenlos dokumentiert und zu 100 % rückverfolgt werden.
Fakten für Konstrukteure
• Hart-Weich-Verbindungen erlauben funktionale Dichtungslösungen in einem Bauteil
• Das Spektrum an additiv hergestellten Dichtungen ist die letzten Jahre deutlich gewachsen
Fakten für Einkäufer
• Wirtschaftliche/s Prototyping und Kleinserienfertigung
Fakten für Qualitätsmanager
• Es stehen heute immer mehr zugelassene Materialien, u.a. mit FDA-Zulassung, für die unterschiedlichsten Branchen zur Verfügung
• Konsequente Bauteilrückverfolgbarkeit unterstützt die Qualitätssicherung effektiv
AKF
Bei der Entwicklung des Arburg Kunststoff-Freiformens (AKF) hat Arburg seine langjährige Expertise in der Kunststoffverarbeitung und im Maschinenbau gebündelt. Der Prozess beginnt – ähnlich wie beim Spritzgießen – mit dem Aufschmelzen von Kunststoffgranulat über einen beheizten Plastifizierzylinder. Anschließend trägt ein starrer Düsenverschluss hochfrequent kleinste Tropfen aus. Jeder Tropfen wird auf die vorher berechnete Stelle auf den beweglichen Bauteilträger aufgelegt und verbindet sich mit umliegendem Material. So entstehen Schicht für Schicht dreidimensionale Bauteile. Die Austragsmenge und Schichtdicke werden bestimmt vom eingestellten Tropfenvolumen, der Frequenz und dem Düsendurchmesser. Die Teilequalität hängt ab von den Materialeigenschaften, der Datenaufbereitung und den Maschinenparametern. Durch eine angepasste Prozessführung erreicht das offene AKF-Verfahren materialabhängig Bauteildichten sowie Zugfestigkeiten, die nahezu denen von spritzgegossenen Teilen entsprechen.
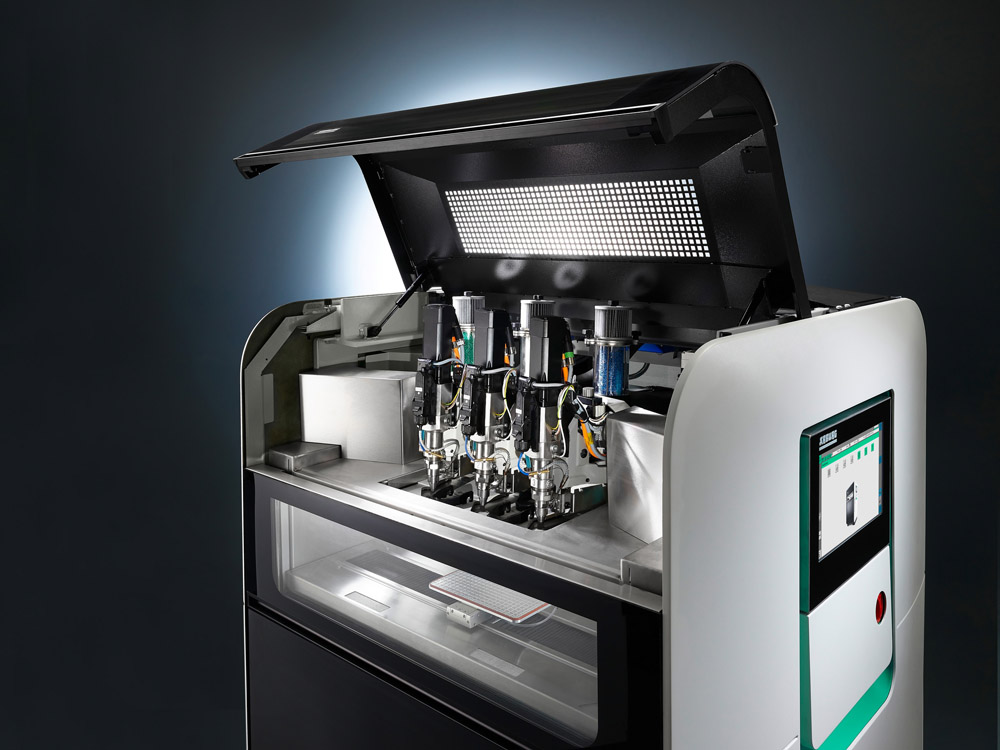
Bild 1: Der Freeformer 300-3X verfügt über drei Austragseinheiten und eine zweigeteilte Bauraumtür (Bild: ARBURG)
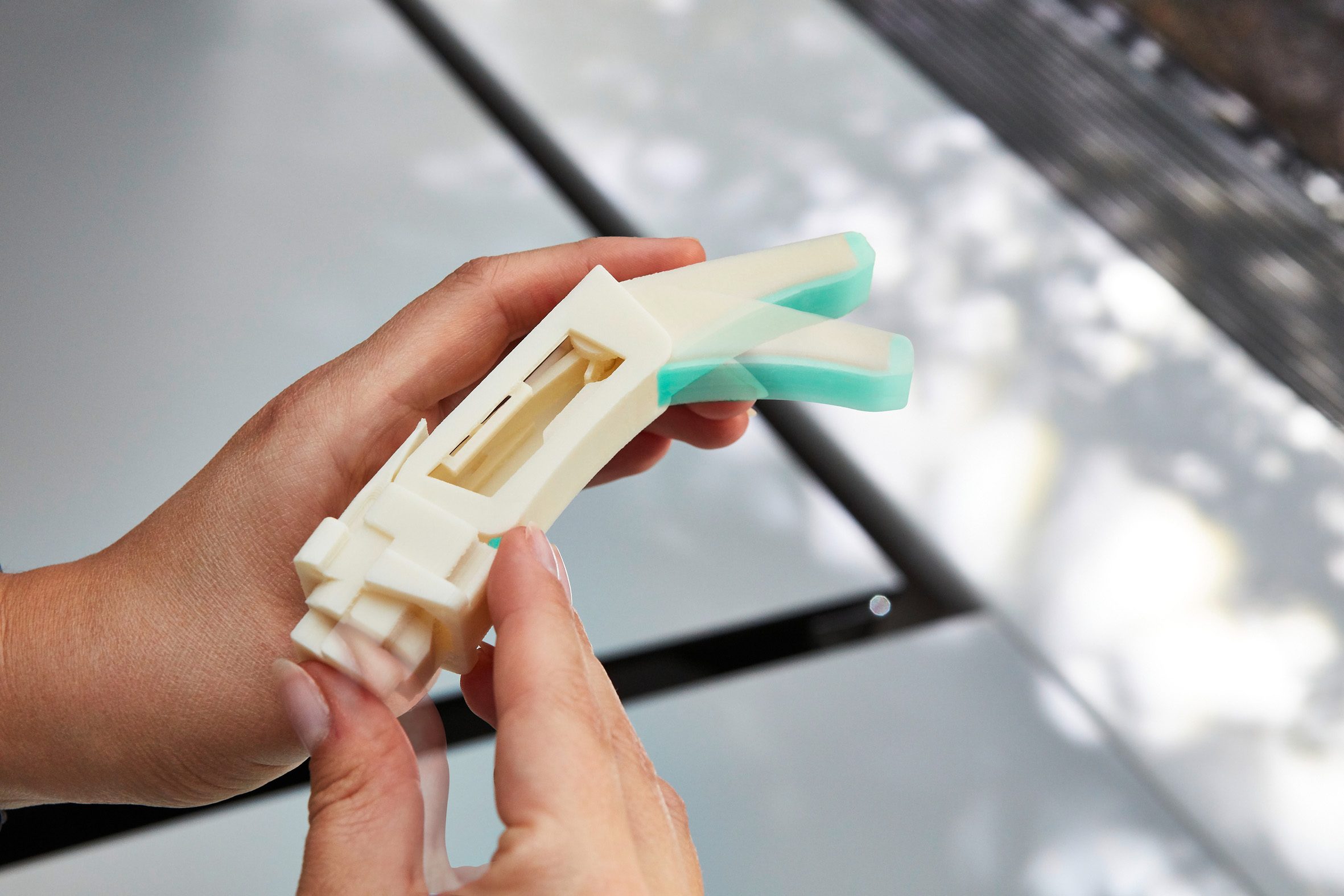
Bild 2: Additiv belastbare Funktionsbauteile in Hart-Weich-Verbindung – ABS, TPU und Stützmaterial werden z. B. zu einem beweglichen Greiferfinger verarbeitet (Bild: ARBURG)
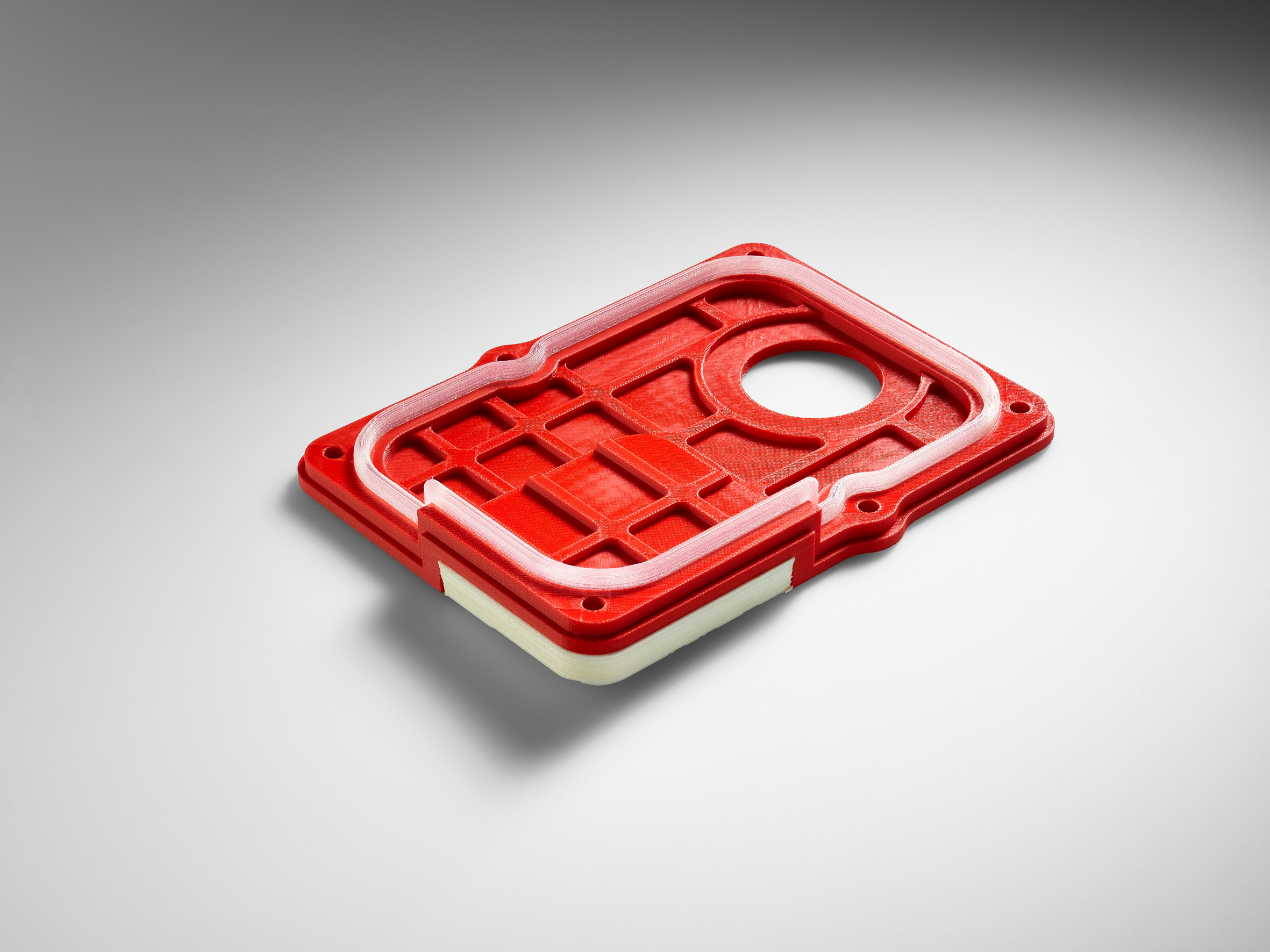
Bild 3: Für die Automobilindustrie fertigt der Freeformer 300-3X aus ABS und elastischem TPE – mithilfe von Stützmaterial, z.B. harte Gehäusedeckel mit weicher Dichtlippe (Bild: ARBURG)
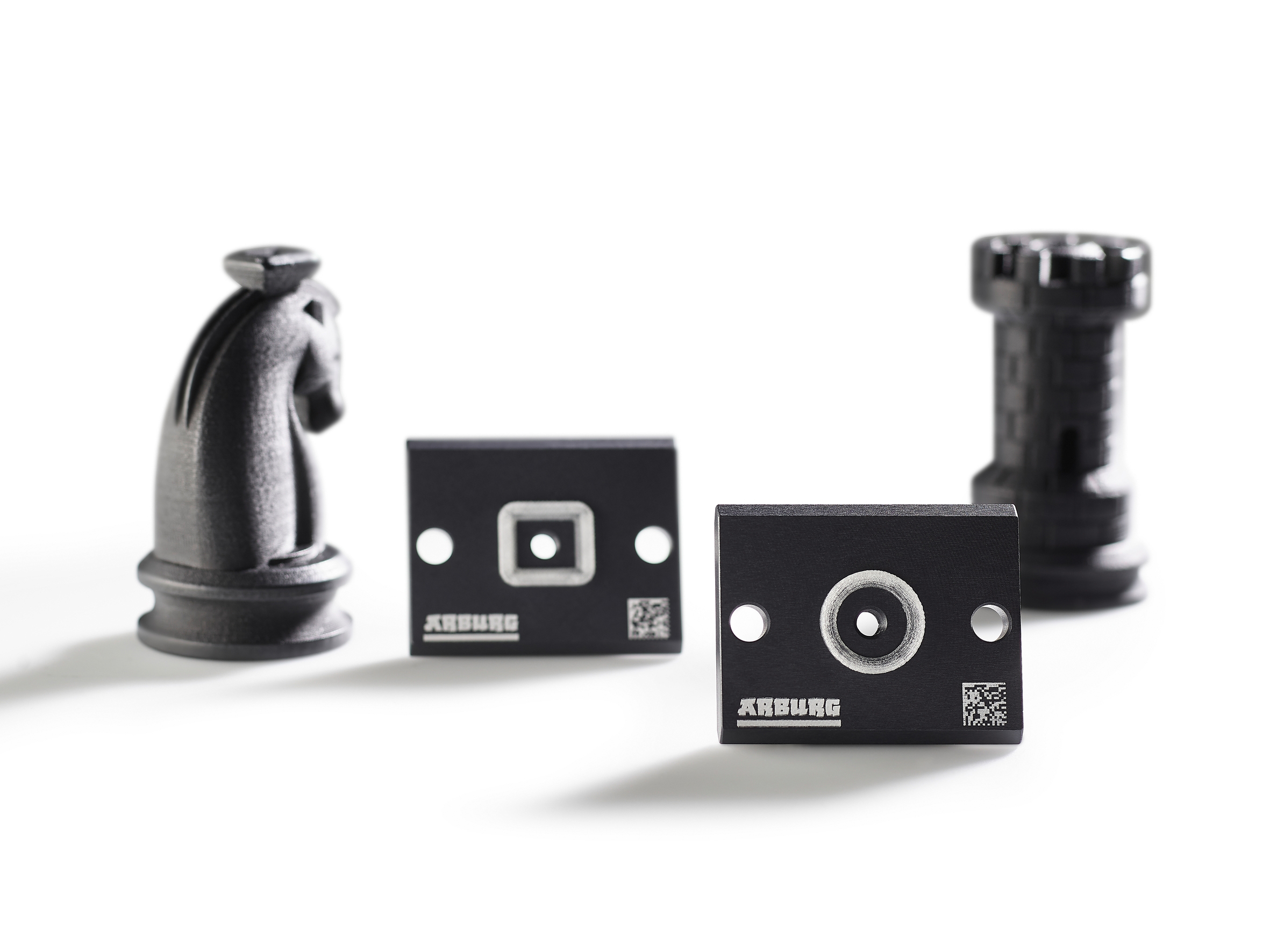
Um Vakuumgreifer zu individualisieren, bringt ein Freeformer 300-3X funktionale TPU-Konturen - in diesem Fall passend zur jeweiligen Schachfigur - auf eine Aluminium-Greiferplatte auf (Bild: Arburg)
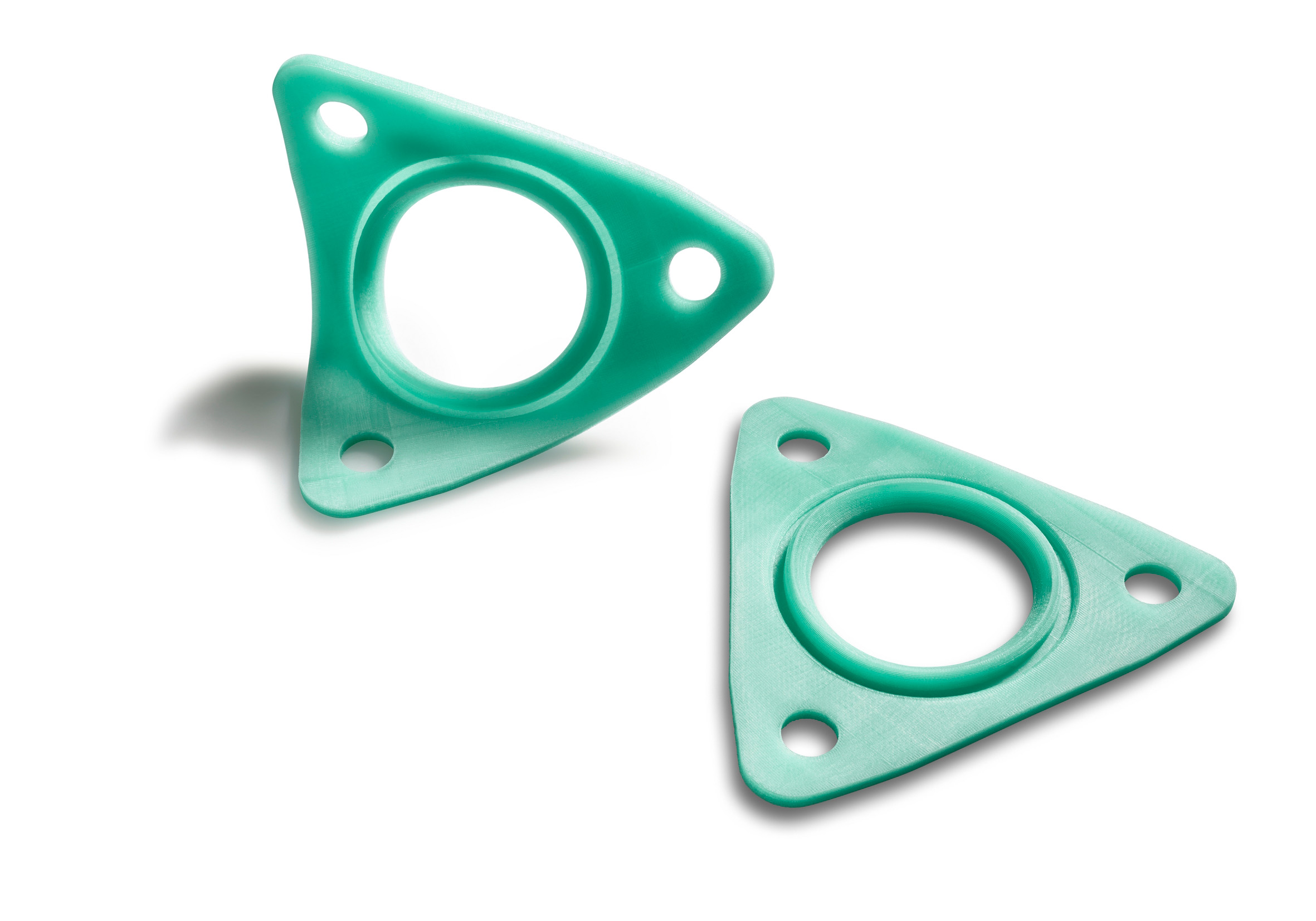
Aus dem TPE-S-Material SEBS (Cawition PR 13576) fertigt der Freeformer additiv sehr weiche und reißfeste Dichtungen (Bild: Arburg)
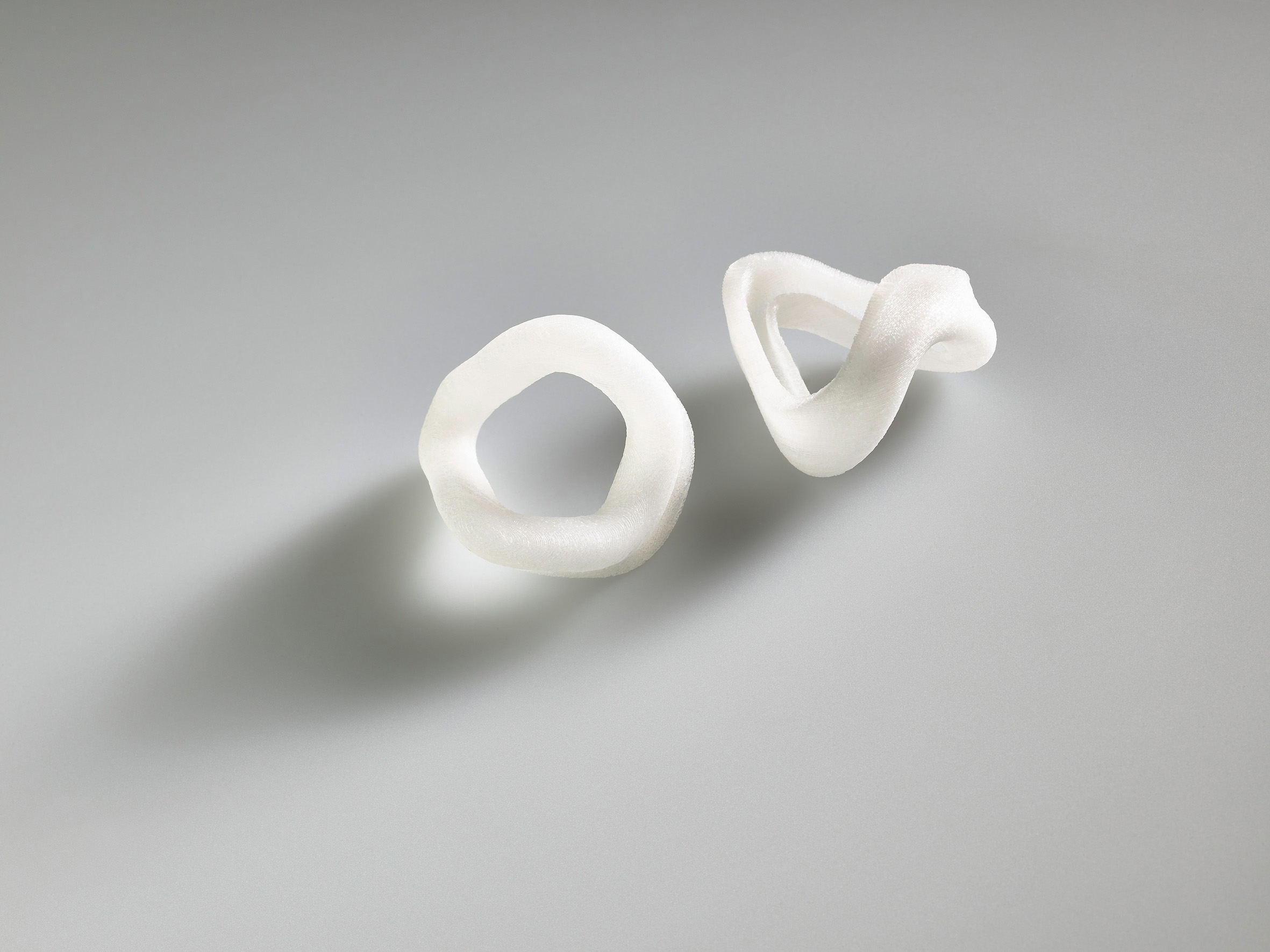
Das medizinische zugelassene TPE Medalist MD 12130H kann im AKF-Verfahren, z.B. zu weichen Komponenten für Beatmungsmasken, verarbeitet werden (Bild: Arburg)