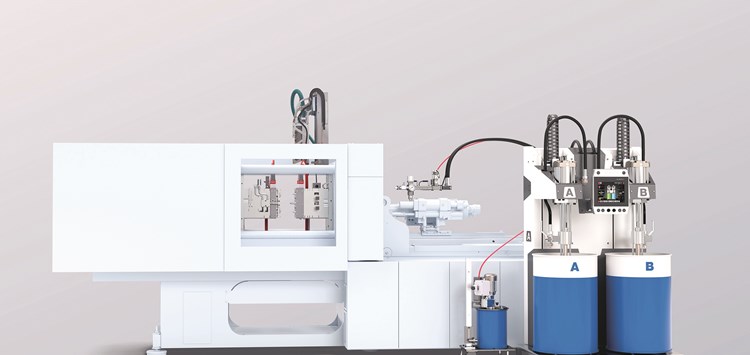
Dosieranlage für 2-Komponenten-Flüssigsilikone mit Spritzgießmaschine (Bild: ELMET GmbH)
18.09.2017 Die „Sinne“ schärfen
Sensoren für optimale Dosierergebnisse
Ein Dosierergebnis hängt von vielen Faktoren ab – u.a. von der Sensorik der Anlagen. So sorgen, z.B. bei Verguss von Elektronikbauteilen oder der Herstellung von 2K-Kunststoffteilen, Drucksensoren und Wegaufnehmer für ein korrektes Mischverhältnis der Komponenten und eine möglichst vollständige Entleerung der Gebinde.
2K-Kunststoffe wie Gießharze oder Flüssigsilikone spielen bei dem Schutz moderner Elektronik eine wichtige Rolle. So bewahren Mäntel aus weichem Flüssigsilikon, z.B. in der Automobilindustrie, Zündkerzenstecker, Schalterabdeckungen oder Regensensoren vor dem Eintreten von Feuchtigkeit und damit vor Kurzschlüssen. Zu einem Feststoff aushärtende Gießharze werden dagegen vor allem als Vergussmasse für elektronische Baugruppen oder offene Kontaktstellen bei Kabeln und Leitungen genutzt. Bei beiden Kunststoffen ist die Herstellung aus zwei Komponenten, die in einem bestimmten Verhältnis zu einer flüssigen Masse vermischt werden, gleich. Beim Gießharz erstarren Harz und Härter durch eine irreversible, chemische Vernetzungsreaktion zu einem Feststoff. Beim Flüssigsilikon werden die beiden additionsvernetzenden Komponenten mithilfe einer Dosieranlage unter Druck einem Mischblock zugeführt. Die fertige Mischung wird anschließend über eine gekühlte Schnecke in das Werkzeug transportiert und vulkanisiert dort bei hohen Temperaturen in Sekunden aus.
Die Einzelkomponenten werden dabei üblicherweise in 20- oder 200-L-Fässern in den Dosieranlagen »1 platziert und an elektrisch betriebene Dosierpumpen angeschlossen. Im Hinblick auf Kosten- und Energieeffizienz ist bei dem Vorgang der Dosierung eine simultane, möglichst 100%ige Entleerung der Fässer mit den Silikon- bzw. Harzkomponenten wünschenswert. Gelingt dies, ist für den Wechsel beider Fässer nur ein Maschinenstopp erforderlich. Zudem spart eine möglichst vollständige Entleerung der Fässer Material und Kosten für die Entsorgung. Die Entleerung der Gebinde wird meistens über große und lange Pneumatikzylinder realisiert. Dabei gibt eine kontinuierliche Messung der Hubposition Auskunft über den aktuellen Füllstand. Drucksensoren messen gleichzeitig permanent den Druck im oder vor dem Messkopf und sorgen so indirekt für einen Gleichlauf bei der Entleerung beider Fässer.