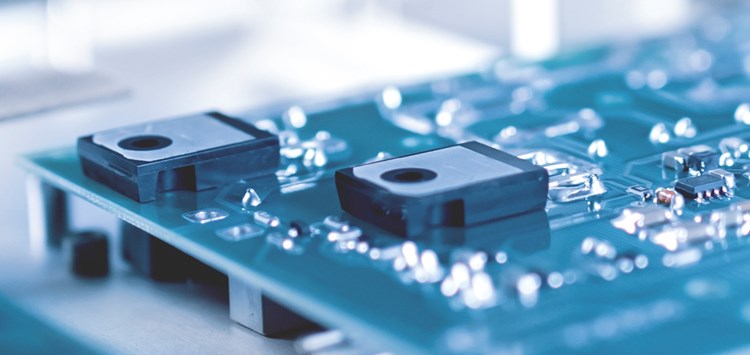
Die Vergussmasse WEVOPUR 512 FLE schützt PCBs zuverlässig vor Korrosion (Bild: Adobestock_YouraPechkin).
07.05.2025 Untersucht: Polyurethan-Vergussmasse für zuverlässige Leiterplatten
Eine Untersuchung der Denmark Technical University (DTU) zeigt einen deutlich besseren Korrosionsschutz des Elektrogießharzes WEVOPUR 512 FLE gegenüber herkömmlichen Conformal Coatings für Leiterplatten (PCBs). Die Polyurethan-Vergussmasse von Wevo ermöglicht selbst bei Kontaminationen einen dauerhaft sicheren Betrieb.
Elektrokorrosion kann die Lebensdauer und Zuverlässigkeit elektronischer Bauteile erheblich reduzieren. Feuchtigkeit und Kontaminationen durch Produktionsrückstände, wie z.B. Flussmittel, verstärken diesen Effekt erheblich. Die meist als PCB-Coating (englisch: Printed Circuit Board) verwendeten Materialien stoßen hier schnell an ihre Grenzen – ihre Schutzwirkung reicht für raue Umgebungen nicht aus. Eine bewährte Wevo-Vergussmasse für Elektronik bietet hier eine leistungsstarke Alternative. Bereits in der Entwicklung des bewährten 2K-Elektrogießharzes WEVOPUR 512 FLE wurde eine Formulierung gewählt, die u.a. das Korrosionsrisiko minimiert. Dazu verzichtete man z.B. auf klassische Flammschutzmittel wie Phosphat-Verbindungen. Durch die speziellen Eigenschaften ist die PU-Vergussmasse neben Kondensatoren oder Feldbusverteilern auch für den Einsatz im Bereich von Leiterplatten geeignet. Die Wirkungen der Vergussmasse als Schutz gegen Elektrokorrosion für PCBs wurde im Rahmen des Industriekonsortiums CreCon (Consortium for Climatically Reliable Electronics) an der DTU untersucht und bestätigt.
Als Prüfkörper dienten SIR-Platten (englisch: Surface Impedance Resistance) mit kammförmig aufgebrachten Leiterbahnen. Sie wurden entweder vorgereinigt oder gezielt kontaminiert und anschließend beschichtet. Dazu verwendete das Forscherteam entweder eines der gängigen Conformal Coatings oder WEVOPUR 512 FLE. Im nächsten Schritt wurden die SIR-Platten einer Reihe praxisnaher Belastungstests unterzogen, um die Schutzwirkung der Materialien zu bewerten. Dabei wurde die elektrische Impedanz gemessen – jegliche Veränderung der Oberfläche, etwa durch Korrosion, beeinflusst diese Werte.
Bei der Leiterplatten-Herstellung kommt es häufig zu Verunreinigungen, zum Beispiel durch Flussmittelrückstände oder Fingerabdrücke aufgrund unsachgemäßer Handhabung (NaCl). Aus diesem Grund untersuchten die Wissenschaftler:innen zunächst den Einfluss der Kontamination auf die Entstehung von Elektrokorrosion. Dazu wurden die beschichteten SIR-Platten einer vorab definierten Klimawechselbeanspruchung ausgesetzt und bei konstanter relativer Luftfeuchtigkeit für jeweils 2 h bei 40 °C und für weitere 2 h bei 65 °C gelagert – und das für 20 aufeinanderfolgende Zyklen. Der Wechsel von 65 auf 40 °C forciert die Kondensation von Wasserdampf, was unter Bestromung die Entstehung von Korrosionsprozessen begünstigen kann.
Im Fall der vorgereinigten Leiterplatten führte dies nur bei einem der Conformal Coatings zu einem nennenswerten Impedanz-Einbruch (von circa 108 Ω auf ungefähr 2⋅106 Ω). Anders sah es bei den mit Flussmittel kontaminierten Prüfkörpern aus: Lediglich die Wevo-Vergussmasse zeigte mit 6,5⋅107 Ω auf der kontaminierten Leiterplatte nahezu die gleiche Leistung wie auf einer sauberen Leiterplatte (5⋅107 Ω) – die Conformal Coatings schnitten hier deutlich schlechter ab. Weitere Tests untersuchten die Beständigkeit des Wevo-Elektrogießharzes bei Einlagerung in Wasser sowie den Einfluss eines Spezialhärters für eine verbesserte Haftung. Beide konnten die Eignung der Wevo-Vergussmasse für PCBs weiter unter Beweis stellen.
Die Testergebnisse belegen die Wirksamkeit des Elektrogießharzes als Schutz vor Elektrokorrosion. Zusätzlich verfügt die Vergussmasse über flammhemmende Eigenschaften nach UL 94 V-0 und darf selbst in kritischen Bereichen wie Personenzügen zum Einsatz kommen. Hier legt die europäische Bahnzulassung EN 45545-2 strenge Regeln für Brandverhalten und Rauchentwicklung fest, die das Material ebenfalls erfüllt. Damit bietet WEVOPUR 512 FLE für anspruchsvolle Anwendungen Vorteile gegenüber den herkömmlichen Conformal Coatings und moderne Elektronik profitiert von höherer Betriebssicherheit, längeren Wartungszyklen und geringeren Ausfallraten.