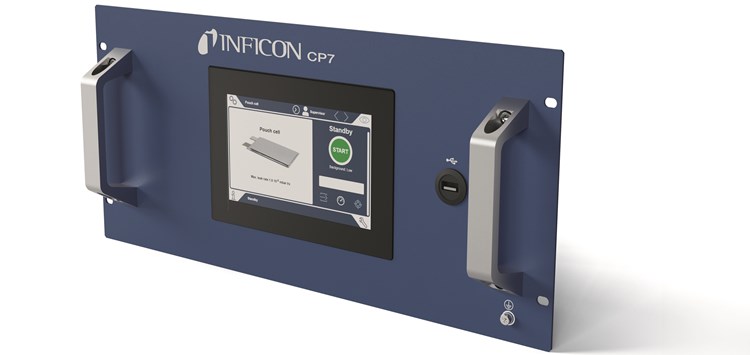
Das System erlaubt die Dichtheitsprüfung an befüllten Lithium-Ionen-Batteriezellen im Takt der Produktion (Bild: Inficon GmbH)
26.03.2024 Individuelle Prüfanlagen in der Batteriezellen-Serienfertigung
Auf der Control 2024 stellt die Inficon GmbH ein Prüfgerät vor, das speziell für die Integration in Dichtheitsprüfanlagen bei der industriellen Serienfertigung von Batteriezellen konzipiert ist: den „ELT Vmax“.
Der ELT Vmax, der für den Einbau in 19-Zoll-Racks vorgesehen ist, prüft die Dichtheit aller mit flüssigem Elektrolyt gefüllten Batteriezellen – ob es um Lithium-Ionen- oder Natrium-Ionen-Zellen geht, um prismatische, Rund- und Knopfzellen mit starrem Gehäuse oder um Pouchzellen mit weichem, beutelartigem Gehäuse. Das Gerät nutzt das von Inficon patentierte Verfahren der direkten Elektrolyt-Dichtheitsprüfung: Es weist aus befüllten Zellen austretendes Elektrolyt in einer Vakuumkammer nach. Bei der Entwicklung des neuen ELT Vmax hat man sich auf eine einfache und flexible Integrierbarkeit in individuell ausgelegte Prüfanlagen fokussiert. Verbunden mit dem Automatisierungs-Know-how eines Integrators ermöglicht der ELT Vmax individuell konzipierte Dichtheitsprüfstationen, die eine konsequente Qualitätssicherung an jeder einzelnen Batteriezelle gestatten – im Takt der Fertigung.
Während der bereits bewährte ELT3000 PLUS wahlweise auch als Stand-alone-Gerät verwendbar ist – etwa für Dichtheitsprüfungen an Prototypen in der Entwicklung –, hat man den neuen ELT Vmax speziell für den Einsatz in der Massenfertigung ausgelegt, als Prüfgerät für individuell konzipierte, automatische Dichtheitsprüfstationen. So beinhaltet ddas Gerät z.B. keine integrierten Vakuumpumpen, weil sich für die industrielle Qualitätssicherung im schnellen Takt der Produktion ohnehin die Verwendung besonders leistungsstarker externer Pumpen empfiehlt. Allerdings ist der ELT Vmax ebenso genau und empfindlich. Er kann kleinste Lecks bis zu einem Durchmesser im einstelligen Mikrometerbereich identifizieren: bis hinab zu einer Heliumäquivalenz-Leckrate von 5∙10-7 mbar∙l/s.
Der ELT Vmax gestattet durch sein 19-Zoll-Gehäuse sowie durch seine seriellen und seine echten Feldbus-Schnittstellen einen unkomplizierten Einbau in beliebige Prüfanlagen. Falls erforderlich, ist er auch mit einem separaten Control-Panel, inkl. Display, lieferbar. Zudem ist das System für den Einsatz in Trockenräumen freigegeben. Durch eine schnelle Grobleckerkennung stellt das Gerät sicher, dass durch sehr große Lecks austretendes Elektrolyt die Prüfanlage nicht stark verunreinigt – trotz des Groblecks steht sie sofort wieder für die nächste Prüfung bereit. Für hohen Durchsatz sorgt zudem ein Trägergas-Modus. Dabei fördert ein kleiner Luftstrom ausgetretenes gasförmiges Elektrolyt noch schneller zum Sensor, was die Messgeschwindigkeit des Systems signifikant erhöht.
Beim Dauereinsatz in der industriellen Serienfertigung empfiehlt es sich, die einwandfreie Funktionalität der Prüfanlage regelmäßig zu überprüfen, sei es zu Beginn jeder Schicht oder z.B. alle zwei Stunden. Zu diesem Zweck steht eine vollautomatische Kalibrierung mit einem Kalibierleck (E-Check 2.0) zur Verfügung. Dieses Kalibrierleck, das zu 100% mit DMC-Elektrolytlösungsmittel befüllt ist, wird in die Vakuumkammer integriert und ist ständig betriebsbereit. So sind auch automatische Testmessungen zu voreingestellten Intervallen möglich. Während eine vollständige Kalibrierung mit dem E-Check 2.0 weniger als 30 s dauert, ist eine einfache Testmessung zur Kontrolle der Prüfgenauigkeit in der üblichen Zykluszeit der Prüfung möglich, d.h. innerhalb von z.B. 12 s. Inficon re-zertifiziert das Kalibrierleck im Jahresrhythmus und befüllt es erneut mit DMC, sodass es sich einfach weiterverwenden lässt.
Der ELT Vmax arbeitet auch im Multikammer-Modus – in Prüfstationen mit mehreren Vakuumprüfkammern. So gibt es für das Gerät keine Wartezeiten während Evakuierungs- und Belüftungsvorgängen: Das Gerät befindet sich dann nahezu ständig im Messbetrieb. Eine weitere Strategie, um den Durchsatz bei der Qualitätssicherung in der industriellen Fertigung zu erhöhen, ist ein Batch-Testing-Ansatz. Die Batteriezellen werden dann stets gemeinsam geprüft, in Chargen von z.B. 16, 32 oder 64 Stück. Fällt eine Charge durch, sind allerdings automatische Nachprüfungen erforderlich. Dabei wird die Charge so lange halbiert, bis die defekte Zelle in einer Charge der Größe eins identifiziert ist. Welche Chargengröße bei solch einer Batch-Testing-Strategie optimal ist, hängt von der typischen Fehlerrate in der Produktion ab. Denn es wäre unsinnig, die Chargen so groß zu wählen, dass sich in nahezu jeder eine undichte Zelle befindet, sodass Nachprüfungen erforderlich werden. Hier gilt es, die optimale Chargengröße für einen maximalen Durchsatz individuell zu bestimmen.
Control: Halle 8, Stand 8303