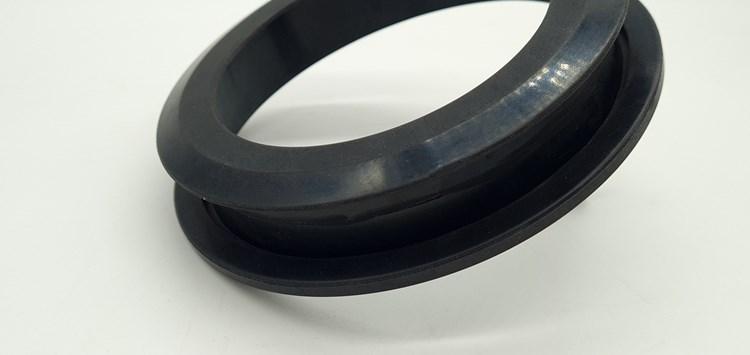
Dieses Formteil wird heute in der benötigten Menge für die Produktion des ProfiTube Fallrohr-Systems bereitgestellt (Bild: Berger S2B GmbH)
23.04.2021 Von der Idee zum Formteil-Serienprodukt
In immer mehr Produkten steckt Hightech, obwohl man es häufig gar nicht vermutet – so auch bei der Berger S2B-Formteillösung für das Haidl ProfiTube Fallrohr-System: ein Projektbericht.
Das Formteil ist ein zentraler Bestandteil des patentierten ProfiTube Fallrohr-Systems von Haidl, das mit vielen Problemen durch die Improvisation mit Folienschläuchen bei Bau- und Reparaturarbeiten an Gebäuden aufräumt.
Doch zurück zum Projektbeginn – wie so oft wurde im ersten Schritt der Geschäftsbeziehung wenig konkretisiert und das Projekt begann mit einer groben Beschreibung und Handskizze des Einsatzes: Das Bauteil sollte als eine Art „Verjüngung“ bzw. „abdichtender Deckel“ für ein Rohr dienen, auf welches ein kleineres Rohr gestülpt werden sollte. Die Geometrie war noch nicht festgelegt. Es sollte aber grundsätzlich möglich sein, dass das Rohr mit einer Stärke von ca. 1 mm immer wieder rein- und rausgenommen werden kann. Dabei musste zunächst keine Dichtigkeit im eigentlichen Sinn gewährleistet sein, aber die Flügel sollten als Dichtlippen dienen. Eine technische Herausforderung war, dass das Rohr, das eingesetzt werden sollte, u.U. scharfe Kanten hat. Bei der Materialspezifikation waren also eine hohe Reißfestigkeit und ein gutes Dehnverhalten zu berücksichtigen. Da das Fallrohrsystem überwiegend outdoor eingesetzt werden sollte, war zudem eine gute Ozon-, UV- und Witterungsbeständigkeit und eine für die unterschiedlichen Klimazonen geeignete Temperaturbeständigkeit gefordert. Die Liefermenge war mit 500 bis 1000 Stück/Monat vorgegeben.
Soweit die Vorgaben: Im Rahmen der Materialspezifikation legte man sich schnell auf ein CR mit 60 Shore A fest. Dieser Werkstoff hat die geforderte hohe Ozon-UV-Beständigkeit und eine universelle, chemische Beständigkeit (bei geringen Mengen/Konzentrationen von Säuren, Laugen, Ölen, Fetten). Darüber hinaus passt das gute mechanische Verhalten des Elastomers zu den Anforderungen. Ein weiteres Kriterium war der relativ günstige Preis des Werkstoffs.
Nach der Materialspezifikation folgte die Ermittlung der optimalen Fertigungsmethode, die einen nicht zu unterschätzenden Einfluss auf Produktqualität und Stückpreis hat. In diesem Kontext wurden zunächst zwei Prototyping-Alternativen in Betracht gezogen:
- Variante 1: Prototypen-Produktion des Gummiformteils aus einem Nest mit der Möglichkeit, im Anschluss mit einem Vierfach-Werkzeug die Serienfertigung zu realisieren.
- Variante 2: Protoytyping im 3D-Druckverfahren und dann die Produktion mit einem Vierfach-Werkzeug in Serienfertigung.
Für Variante 2 sprachen die geringeren Kosten beim Prototyping, die höhere Flexibilität bei der Teilegeometrie – und damit die Möglichkeit einfacher Modifikationen – und ein Herantasten an die Lösung ohne aufwändige Simulation. Für erste Versuche wurden dann 3D-Druck-Muster – hergestellt per SLS-Verfahren – beauftragt. Da für den 3D-Druck kein CR-Elastomer zur Verfügung stand, wurde alternativ ein thermoplastischer Elastomerwerkstoff mit gummiähnlicher Flexibilität und Funktionalität gewählt – ein TPU mit 65 Shore A. Vorteilhaft ist, dass man beim 3D-Druck unproblematisch die Härte und Konturen ändern kann, ohne dass erneut Werkzeugkosten anfallen. Einschränkungen beim Toleranzbereich, der beim SLS-Verfahren bei ± 0,3 mm liegt, und hinsichtlich der Tatsache, dass Details unter 0,8 mm nicht oder nur unvollständig dargestellt werden können, gab es hier nicht. Nachteilig ist bei dieser Prototyping-Vorgehensweise immer, dass das Material nicht vergleichbar mit einem vulkanisierten Elastomer ist. Bei diesem Projekt war dies aber kein K.-o.-Kriterium. Vielmehr erwies sich die Entscheidung für das Verfahren als richtig, da es zu Modifikationen an der Dichtungslippe und den Gesamtkonturen kam. Zur Überprüfung der Nutzung und Funktion konnten so binnen zwei Wochen erneut Muster gedruckt werden. Das war schneller und günstiger als es bei Variante 1 möglich gewesen wäre. Nach der erneuten 3D-Teilebemusterung entsprachen die Konturen und Geometrien den Anforderungen und die Ergebnisse mündeten in die Produktion des Serienteils auf CR-Basis.
Um international wettbewerbsfähig zu sein, werden die Formteile heute von einem Berger S2B-Partnerunternehmen in Indien produziert. Inzwischen übernimmt Berger S2B im Rahmen seines Dichtec®-Konzeptes die Lagerhaltung und Disposition, sodass Haidl jederzeit kurzfristig die benötigten Mengen abrufen kann. Das Projekt zeigt, dass durch das frühe Hinzuziehen eines Spezialisten, der Entwicklungsprozess und Wertschöpfungskette ganzheitlich unterstützen und abdecken kann, innerhalb von fünf Monaten Formteillösungen entstehen können, in denen mehr steckt, als man vermutet.