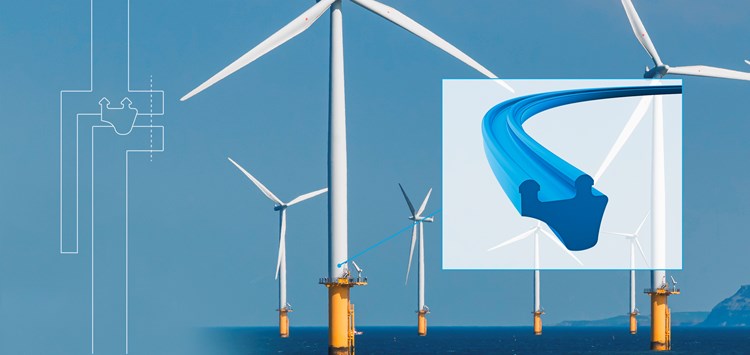
80% aller aktuell projektierten Meeres-Windparks basieren auf der Monopile-Technik, an die Dichtungen werden – nicht nur hinsichtlich der Standzeiten – höchste Anforderungen gestellt (Bild: Freudenberg Sealing Technologies)
04.10.2022 Erhöhte Dichtungslebensdauer bei Offshore-Windkraftanlagen
Auf mindestens 60 GW will die Europäische Union die Kapazität für auf dem Meer erzeugten Windstrom bis zum Jahr 2030 ausbauen. Freudenberg Sealing Technologies trägt mit Dichtungslösungen für die Gründungsstrukturen dazu bei, dass neue Windkraftanlagen trotz der rauen Bedingungen auf See eine Lebensdauer von 30 Jahren und mehr erreichen.
191 km/h betrug die höchste Windgeschwindigkeit, die bislang in der deutschen Nordsee gemessen wurde. Zwar werden im Meer errichtete Windkraftanlagen bereits bei deutlich niedrigeren Windgeschwindigkeiten abgeschaltet. Doch den gewaltigen Kräften eines Orkans müssen die Anlagen unter allen Umständen trotzen – und das über die gesamte Lebensdauer. Eine wichtige Rolle spielt dafür die Gründung, mit der die Türme im Meeresboden verankert werden. Sie erfolgt bei geringer Wassertiefe, wie sie in Nord- und Ostsee vorherrschen, i.d.R. durch „Monopiles“. Dabei handelt es sich um Stahlpfeiler, die in den Meeresboden gerammt werden und deren oberes Ende sich oberhalb der Wasseroberfläche befindet. Der Turm, der bereits bei einer 10-MW-Anlage eine Höhe von 150 m bis zur Rotornabe erreichen kann, wird i.d.R. nicht direkt auf den Pfeiler montiert, sondern von einem Verbindungsstück – einem Flansch – getragen. Die Befestigung des Flansches erfolgt mit mehreren Dutzend Schraubenbolzen, die nach der Montage des Turms für jede Wartung unzugänglich sind. Damit die Verschraubung trotz der rauen Umgebung auf See nicht korrodiert, muss sie vor dem Eindringen von Feuchtigkeit geschützt werden. In mehr als 800 Offshore-Windkraftanlagen übernehmen heute bereits Dichtungen von Freudenberg Sealing Technologies diese Aufgabe.
Die wichtigste Funktion kommt einer Ringdichtung am oberen Ende des Pfeilers zu: Sie umschließt den innen liegenden Teil des Verbindungsstücks, der die Verschraubung trägt. Diese Flanschdichtung mit dem Kürzel MP-TP (Monopile-Transition-Piece) kann für moderne Anlagen einen Durchmesser von 8 bis 10 m erreichen. Seit einigen Jahren bietet man diese Dichtung auch in doppelter Ausführung an. Vorteil des zweireihigen Aufbaus ist vor allem die sich ergebende Redundanz: Kommt es während des Transports oder der Montage zu kleinen Schäden an einer der beiden Dichtungen, ist die Funktion trotzdem sichergestellt. Darüber hinaus lassen sich verschiedene Designs und Materialien in optimaler Weise miteinander kombinieren. Die konkrete konstruktive Auslegung erfolgt allerdings fast ausschließlich kundenspezifisch, um den vorhandenen Bauraum optimal zu nutzen. Auf Wunsch bietet man auch ein bereits etabliertes Standardprodukt an.
Bei gängiger Bauweise verbleibt ein Spalt zwischen dem unteren Ende des Verbindungsstücks und dem Pfeiler. Dafür, dass kein Meerwasser eindringen kann, sorgen eine oder zwei mit Luftkammern durchzogene Ringdichtungen, die als elastische Wellenbrecher ausgelegt sind. Wird der Spalt hingegen mit Zement aufgefüllt, kann eine Ringdichtung den Zement während des Aushärtens in der gewünschten Position halten und später vor einem Salzwasserangriff schützen. Zudem lassen sich Wartungsplattformen, die oft oberhalb der Wasseroberfläche im Inneren des Monopiles angebracht sind, mit einer speziell ausgelegten Dichtung vor dem Eindringen von Gasen schützen. Solche Gase bilden sich unter Umständen aufgrund biologischer Prozesse des Meerwassers im Pfeiler.
Die Lebensdauererwartungen an die Bauteile von seegestützten Windkraftanlagen sind in den vergangenen Jahren stark gestiegen. Galten anfangs 25 Jahre als guter Wert, erfolgt die Auslegung mittlerweile auf bis zu 35 Jahre. Eine so lange Betriebsdauer kann nicht über Prüfstandtests abgesichert werden. Deshalb extrapoliert Freudenberg die Ergebnisse sechswöchiger intensiver Belastungstests mithilfe eines adaptierten Arrhenius-Algorithmus. Das nach dem schwedischen Chemiker und Nobelpreisträger Svante August Arrhenius benannte und an sich bekannte Verfahren wurde in den letzten Jahren von dem Unternehmen konsequent weiterentwickelt. So wurde das Lebensdauermodell deutlich verbessert, indem chemische und physikalische Effekte mit dem strukturmechanischen Verhalten des Werkstoffs gekoppelt wurden.