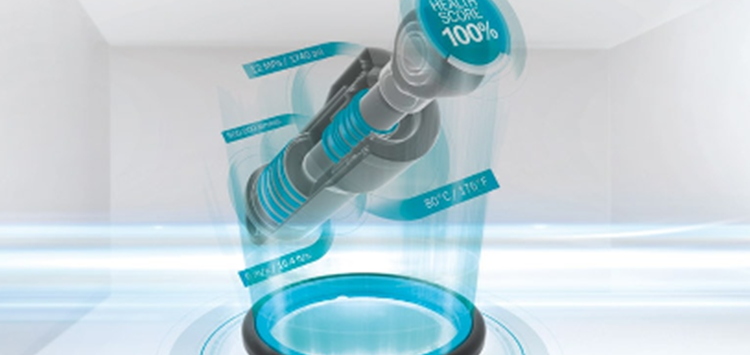
Mit intelligenten Dichtungen lässt sich kontinuierlich der „Health Score“ und somit der Zustand der Dichtung bestimmen (Bild: Trelleborg Sealing Solutions)
11.03.2025 Brauchen Dichtungen Intelligenz?
Argumente. Lösungen. Praxistipps.
Knackpunkt intelligenter Dichtungen ist, dass sie bis heute nicht als standardisierte Produkte mit definierten Systemschnittstellen zur Datenerfassung und -übertragung nutzbar sind.
Die Dichtung selbst ist oft nur so gut wie der Bauraum um sie herum. Daher sind Lösungsansätze im System zu suchen – und weniger bezogen auf eine Dichtung als einzelnes Konstruktionselement. Allzu oft sind es die Anwendungsbedingungen, die Dichtungen an Grenzen führen. Temperatur, Reibung und Medien wirken auf die Dichtung und verändern ihre Eigenschaften über die Nutzungsdauer oder beschleunigen Abnutzungsprozesse, die dann zu verkürzten Nutzungszyklen führen.
Häufig gibt es bereits ausreichend Sensorik im Aggregat, sodass die Dichtung auch mittels bereits bestehender Daten und Sensorinformationen mit überwacht werden kann. Deshalb entwickeln wir sie stets in enger Entwicklungspartnerschaft mit unseren Kunden. Hierfür bündeln wir das Know-how unserer Expert:innen aus den Bereichen Elektronik, Dichtungstechnik und IT über „Cognitive Sealing“.
Wichtigstes Instrument einer intelligenten Dichtung sind Zustandsdaten und deren Analyse. Nur wenn es gelingt, Sensordaten von Parametern wie Druck, Temperatur, Vibration oder Geschwindigkeit mit historischen Daten in Echtzeit auszuwerten, wird eine Dichtung intelligent. Mit KI-gestützten Systemen entwickeln wir ein Predictive Maintenance, das den Ist-Zustand einer Dichtung jederzeit bewerten kann. So kann eine Wartung rechtzeitig eingeleitet und dadurch ein Effizienzverlust oder Ausfall der Dichtungskomponente verhindert werden.
Den Einsatz von „Cognitive Sealing“ sehen wir daher vor allem bei Anlagen und Geräten, bei denen maximale Sicherheiten und minimale Ausfallzeiten entscheidend sind, um hohe Kosten zu vermeiden. Wir sehen das größte Potenzial im Offshore-Bereich, wo es um hydraulische Systemlösungen von Windkraftanlagen, Ölplattformen oder Wellenkraftwerken geht und die Wartung oder Reparatur einen enormen Aufwand bedeuten würde. Aber auch in der Luft- und Raumfahrt können sich intelligente Dichtungen durchaus lohnen. Unsere Kunden unterstützen wir dabei von der Sensorauswahl über die KI-basierte Datenanalyse bis hin zum Dashboard, das Auskunft über den Systemzustand gibt. Zudem nutzen wir unsere eigene Datenbasis, um bestehende Dichtungslösungen kontinuierlich zu optimieren.
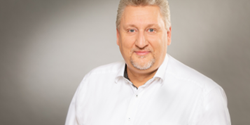
„Intelligente Dichtungen gibt es nicht von der Stange.“ Professor Dr. Konrad Saur, Vice President Innovation, Trelleborg Sealing Solutions