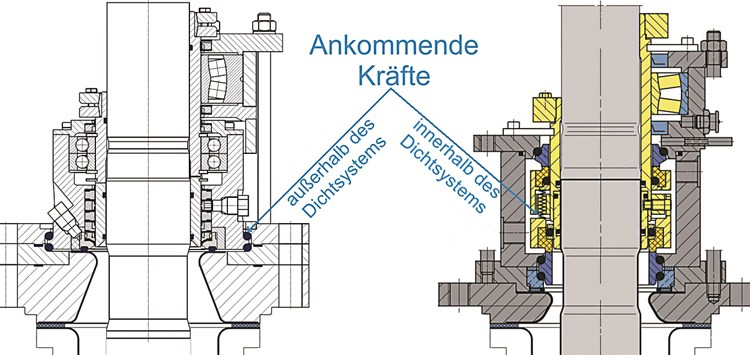
Verlagerung der Taumel- und Auslenkbewegung aus dem Dichtungsinnenbereich (Bild: Pfaudler interseal GmbH)
04.06.2018 Ein langer Weg ... und Ziel erreicht
Schutzkonzept für Wellenlippendichtung in anspruchsvoller Prozessumgebung
Die Herstellung von Feststoffen und Trocknungsprozesse stellen in diesen Industriebereichen erhöhte Anforderungen an Dichtungssysteme und sorgen bei fehlenden Schutzkonzepten für erhöhten Verschleiß. Deshalb wurde über Jahrzehnte an diesem Problem gearbeitet – mit dem Ergebnis einer Dichtungslösung, die auch den hohen Anforderungen der Pharmaindustrie Rechnung trägt.
Die Medien, z.B. Feststoffe, die im Misch- und Trocknungsprozess verarbeitet werden, stehen typischerweise im direkten Kontakt mit den Dichtelementen. Ihre Aufgabe ist es, Medien, die aufgrund ihrer molekularen Struktur geeignet sind, in eine Dichtstelle einzudringen, daran zu hindern. Denn eingedrungene Medien beschädigen die Dichtelemente nachhaltig und führen zu deutlich reduzierten Laufzeiten und damit zu unnötig hohen Produktionskosten bzw. schlimmstenfalls teuren Produktionsausfällen.
Erhöhte Anforderungen der Pharmaindustrie
Bei pharmazeutischen Prozessen besteht zudem die Herausforderung einer GMP- (Good Manufacturing Practice) gerechten Konstruktion der Dichtungslösung, die den besonderen Reinheitsanforderungen dieser Branche Rechnung trägt. Konstruktiv wird hier vorausgesetzt, dass keine unnötigen Toträume entstehen, in denen sich das Medium absetzen kann und die in Folge gar nicht oder nur schwer gereinigt werden können.
Gängige Dichtungslösungen verfügen derzeit über keine oder nur eingeschränkte Schutzoptionen, um die Dichtung vor eindringenden Medien aktiv zu schützen. Auch die in der GLRD-Technik direkt im Produkt angewendete rotierende Gegenringpaarung ist am Ende auch „nur“ eine Kompromisslösung, da das Medium sofort in den Sperrkreislauf (z.B. Flüssigkeit oder Gas) eindringt und sich dort ablagert.
Ein weiteres Problem sind die typischerweise auftretenden radialen Wellenbewegungen bei Mischern und ähnlichen Maschinen. Sie erhöhen die Anforderungen an die Leistungsfähigkeit und Funktion der Dichtung. Diese Auslenkungskräfte, die während des Mischprozesses entstehen, übertragen sich auf das Dichtsystem und führen dort zu Spaltwirkungen. Beispiele sind der typische V-Spalt bei GLRD oder extreme Belastungen der Lippenelemente bei der klassische Lippendichtung. Eine Ideallösung ist also eine Verlagerung der Taumel- und Auslenkbewegung aus dem Dichtungsinnenbereich heraus nach außen. Damit werden die relativen Kräfte an den Dichtelementen eliminiert. Bei Maschinen mit horizontalen Wellen ist zudem zu beachten, dass die Wellenbewegungen auch über die eigentliche Dichtstelle bzw. -strecke hinaus – also vor der Dichtung – wirken. Gerade bei horizontalen Anwendungen besteht damit das Problem, dass das Medium während des Mischprozesses immer direkt in Kontakt mit den Dichtelementen gelangt und damit das Dichtsystem belastet. Hierfür wurde schon länger eine Lösung gesucht, um die Standzeiten der Dichtsysteme nachhaltig zu steigern.
Der Dichtungsschutz rückt in den Fokus
Während des langen Entwicklungswegs wurden zwar immer wieder neue konstruktive Lösungen gefunden, die bestimmte Probleme minimierten, die aber letztendlich nicht alle heutigen Anforderungen erfüllten. Deshalb legte man in der letzten Entwicklungsphase den Fokus auf die Optimierung einer Schutzeinheit. Sie sollte das Dichtsystem perfekt vor schwierigen Medien abschotten, um so die eigentlichen Dichtelemente nachhaltig zu schützen.
Idealerweise muss diese vorgelagerte Schutzeinheit in eine Dichtung nach DIN-Abmessungen integrierbar sein und so flexibel gestaltet sein, dass sie in bestehende Einbauräume mit der Dichtungseinheit verbaut werden kann.
Doch zurück zu den Entwicklungsstufen. Die erste Entwicklung bestand aus zwei hintereinander platzierten „angefederten Drosselringen“. Optional bestand die Möglichkeit, zwischen diese beiden Drosselringe Stickstoff als Sperrgas einzubringen. Diese Ausführung »2 brachte allerdings im Bereich der Eigenerwärmung (Reibung) und mit einem zu hohen Abrieb der Bauteile Nachteile mit sich. Auch der vorhandene Totraum dieser Konstruktion war für pharmazeutische Prozesse ungeeignet. Allerdings wurde das Dichtsystem mit diesem Ansatz vor dem Medium geschützt und es wurden längere Standzeiten erreicht.
Auf Basis dieser Erfahrungen und Rückmeldungen von Anwendern entschloss man sich dann, eine andere Form des Drosselringes einzusetzen. Das Design wurde hier so gewählt, dass das Bauteil aus einem Stück gedreht wurde »3. Dabei entlastet eine Art nachgelagertes Stützlager die vorgesetzte integrierte Lippe. Dieses Element kann zudem in einer Ebene den Wellenbewegungen radial folgen. Diese Variante hatte den Vorteil, dass sie den ankommenden Kräften, die während des Mischprozesses auftreten und auf die Lippe wirken, besser folgen konnte und die Lippe – wenn auch in stark eingeschränktem Maße – dahingehend etwas entlastet wird. Problematisch ist bei diesem Design allerdings, dass die Dichtlippe produktseitig komplett dem Medium „ausgeliefert“ ist – also die komplette Stirnfläche beaufschlagt wird. In »3 wird deutlich, was dies bedeutet. Das Medium arbeitet an der Lippe bzw. dem Werkstoff. Ferner können auch mit dieser Konstruktion weder die Anforderungen an eine totraumarme Dichtungsausführung noch die CIP-Fähigkeit umgesetzt werden. Eine CIP-Reinigung würde das Dichtelement erstens zwischen der Lippe und dem „Stützlager“ nicht erreichen und zweitens produktseitig die eigentliche Lippe zerstören.
Im letzten Entwicklungsschritt ist es gelungen, alle Aspekte, die von der Pharmaindustrie an eine hochwertige Dichtung gestellt werden, in einem Schutzsystem umzusetzen. Gelungen ist dies insbesondere durch den Einsatz der „metallischen Dichtlippe“, die sich wie ein Schutzschild vor die eigentliche Dichtlippe legt. Damit gelangt das Medium nicht mehr an die eigentliche Lippe und kann diese auch nicht mehr beschädigen. Diese Ausführung »4 kann den Bewegungen der Rührwerkswellen folgen. Hier ersetzt – im
Vergleich zur Vorentwicklung – ein metallischer Grundkörper den PTFE-Grundkörper. Materialausdehnungen aufgrund von Druckund Temperaturschwankungen werden so minimiert. Diese Lösung entspricht den hohen Anforderungen an eine GMP-gerechte Ausführung, ist CIP-geeignet und FDA-konform. Vorteilhaft ist auch die Option des Schutzgaseinsatzes, das hinter dieser Einheit vom Innenraum her in Richtung Produkt strömt.
Fakten für Konstrukteure
• Das Dichtsystem ist DIN-konform und passt in bestehende Einbauräume
• Das Dichtsystem ist unanfälliger gegen Druck- und Temperaturschwankungen
Fakten für Einkäufer
• Verlängerte Standzeiten reduzieren die TCO (Total Cost of Ownership) signifikant für die Betreiber
Fakten für Qualitätsmanager
• Die GMP-gerechte Ausführung ist CIP-geeignet und FDA-konform und trägt den hohen Qualitätsanforderungen der Pharmaindustrie Rechnung
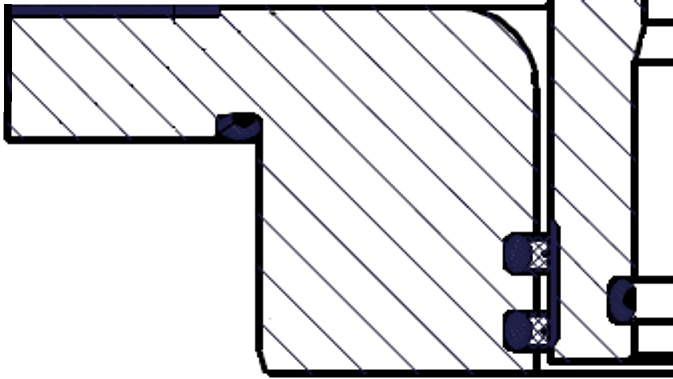
»2 Der Drosselring-Abstreifer sorgte über viele Jahre für verlängerte Standzeiten (Bild: Pfaudler interseal GmbH)
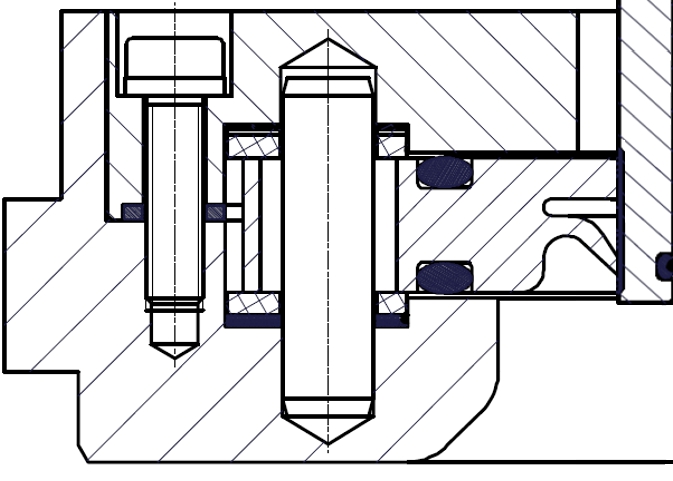
»3 Mit dem beweglichen Abstreifer bekam man zudem die Probleme der radialen Auslenkung der Wellen in den Griff (Bild: Pfaudler interseal GmbH)
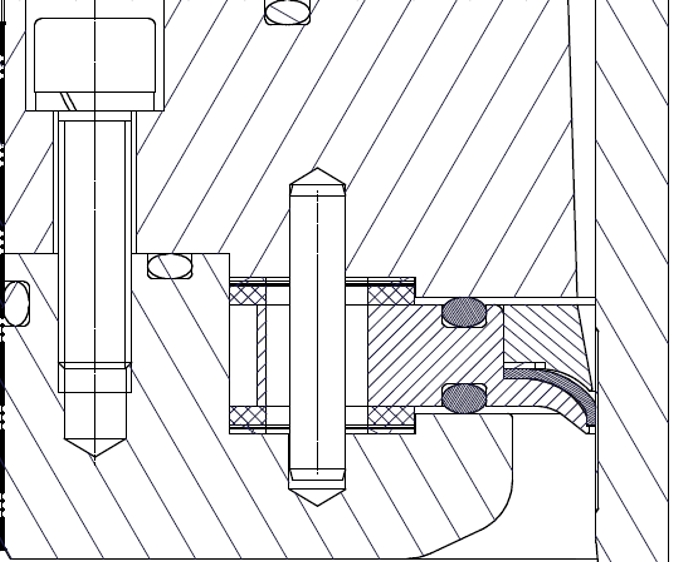
»4 Mit dem beweglichen, metallischen Abstreifer lässt sich die Performance der trockenlaufenden Wellenlippendichtung Typ dry9000 weiter steigern (Bild: Pfaudler interseal GmbH)