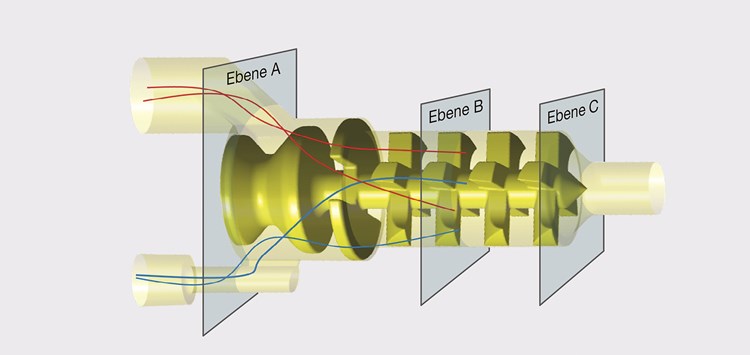
Dynamischer Mischer – die blauen und roten Linien symbolisieren das Particle Tracking (Bild: Sulzer Mixpac Ltd.)
17.09.2018 Optimaler mischen
Tool zur Simulation der Mischqualität
Mit dem zunehmenden Einsatz von 2K-Materialien geht auch die Suche nach effektiveren und zuverlässigeren Applikationssystemen weiter. Bei der erfolgreichen Anwendung von Mehrkomponenten- Materialien ist und bleibt das Mischsystem ein entscheidendes Element. Mit einem neuen Tool lässt sich die Mischqualität sicher vorhersagen.
Heute stehen statische Mischer in verschiedenen Ausführungen für laminare Mischvorgänge zur Verfügung. Diese kompakten Geräte sind kostengünstig und benutzerfreundlich, können aber bei Komponenten mit stark unterschiedlichen Materialeigenschaften, z.B. unterschiedlicher Viskosität, zu einem suboptimalen Ergebnis führen. Gleiches gilt, wenn von einer Komponente wesentlich mehr verwendet wird als von der anderen. Für solche anspruchsvollen Anwendungen werden häufig dynamische Mischer bevorzugt. In diesen erzeugen schnell rotierende Flügel hohe Scherkräfte und ermöglichen so ein präzises Mischen und Austragen. Die beweglichen Teile dieser Mischer rotieren mit bis zu 1.500 min-1, wobei die Axialgeschwindigkeit des Materials im Mischer nur wenige cm/s betragen kann.
Simulation bewährt sich
Benötigen Anwender neue Mischlösungen für ihre speziellen Anforderungen, sind möglichst kurze Entwicklungszyklen gefragt. Eines der am häufigsten genutzten internen Verfahren zur Simulation von Strömungen und deren zeitlicher Änderung ist Computational Fluid Dynamics (CFD). Damit können komplexe Phänomene wie Mehrphasenstrom-Wechselwirkungen, Phasenumwandlung, Fluid-Struktur-Wechselwirkungen usw. berücksichtigt werden. Dank der steigenden Rechenleistung und Fortschritten auf dem Gebiet der numerischen Verfahren werden Simulationen immer häufiger für die Auslegung und Optimierung in verschiedenen Bereichen eingesetzt.
Trotz der Fortschritte, die mithilfe kommerzieller Software möglich geworden sind, lassen sich laminare Mischprozesse nicht exakt vorhersagen. Das laminare Mischen basiert auf der Erzeugung, Teilung und Streckung von Materialschichten innerhalb des Mischers. Diese Schichten werden über die Länge des Mischers zunehmend feiner und dadurch gemischt. Diese sehr feinen Schichten können mit herkömmlichen CFD-Gittern nur unzureichend räumlich aufgelöst werden, was zu einem numerischen Fehler, der numerischen Diffusion, führt. Diese numerische Diffusion führt zu einer Überschätzung der Mischqualität und einem verschmierten Erscheinungsbild der Mischverteilung – im Gegensatz zur Messung, bei der die klaren Grenzen zwischen den beiden Materialien noch immer erkennbar sind.
Diffusionsfreies Particle Tracking
In den vergangenen Jahren wurde versucht, diese Einschränkungen zu überwinden, um den Entwicklungsprozess für Mischer zu beschleunigen und ein exakteres Mischergebnis zu erzielen. Ein bekannter Ansatz ist die Bestimmung der Mischverteilung und des Konzentrationsfelds mithilfe von diskreten, entsprechend der Konzentration gefärbten Partikeln. Die Farben Rot und Blau in Bild 1 stehen für unterschiedliche Konzentrationen. Mithilfe der Partikel kann berechnet werden, wie sich Materialien mit unterschiedlichen Konzentrationen durch den Mischer bewegen. Diese Methode wird Particle Tracking genannt. Sie ermöglicht eine hochauflösende Abbildung der Mischverteilung und wird bereits seit Längerem für statische Mischer angewandt.
Anders als bei statischen Mischkanülen verändert sich bei dynamischen Mischern das Strömungsfeld im Mischer im zeitlichen Verlauf. Daher ist der bisherige Ansatz, d.h. die Offline-Verfolgung einer begrenzten Anzahl von Partikeln auf der Basis eines stationären Strömungsfelds, nicht mehr anwendbar. Neben dem instationären Strömungsfeld bringt die Mehrskaligkeit des Problems weitere praktische Herausforderungen mit sich. Der Rotor dieser Mischer dreht sich mit bis zu 1.500 min⁻1. Die Axialgeschwindigkeit der Strömung kann hingegen nur wenige mm/s betragen. Die Simulation des gesamten Vorgangs einschließlich des Befüllens des Mischers und der Erfassung der Rotation mit ausreichender Genauigkeit ist eine Herausforderung.
Fazit
Nach zahlreichen Tests und Messungen ist es gelungen, ein zuverlässiges Tool zu entwickeln. Die neu entwickelten und implementierten Algorithmen bieten die Möglichkeit, die Mischqualität in dynamischen Mischern genauer vorherzusagen. Außerdem können die notwendigen Berechnungen innerhalb der praktischen Grenzen verfügbarer Rechenressourcen durchgeführt werden.
Fakten für Konstrukteure
• Das Tool erlaubt die beschleunigte Auslegung und die Optimierung von neuen und vorhandenen Produkten
• Das ermöglicht es, Designs und Lösungen für den stetig zunehmenden Einsatz von 2K-Materialien in allen Bereichen des modernen Lebens zu realisieren
Fakten für Einkäufer
• Die optimale Mischung von Klebstoff senkt die Produktionskosten
Fakten für Qualitätsmanager
• Eine optimale Mischqualität von 2K- und Mehrkomponentenklebstoffen steigert die Produktqualität
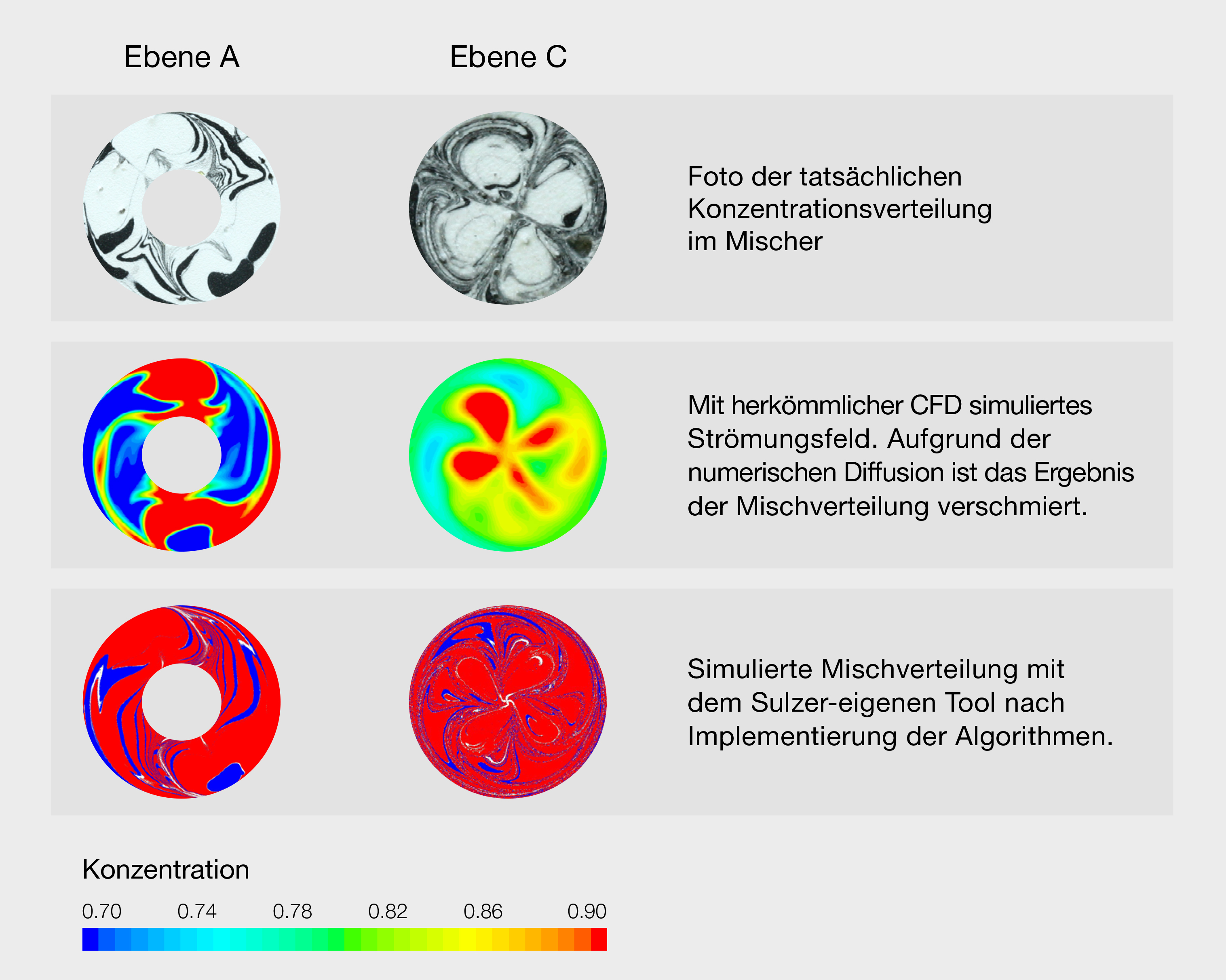
Vergleich von Mischergebnissen (Bild: Sulzer Mixpac Ltd.)
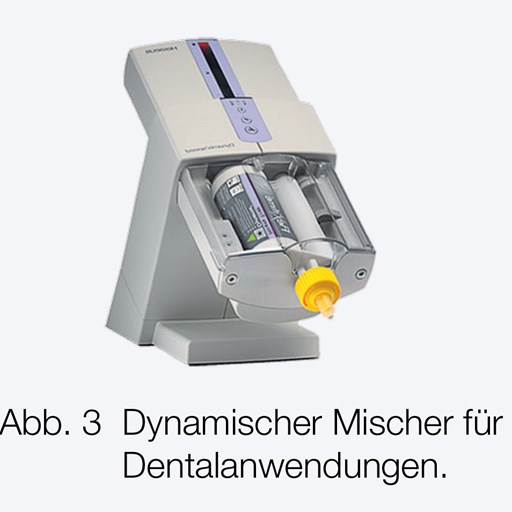
Dynamischer Mischer für Dentalanwendungen (Bild: Sulzer Mixpac Ltd.)
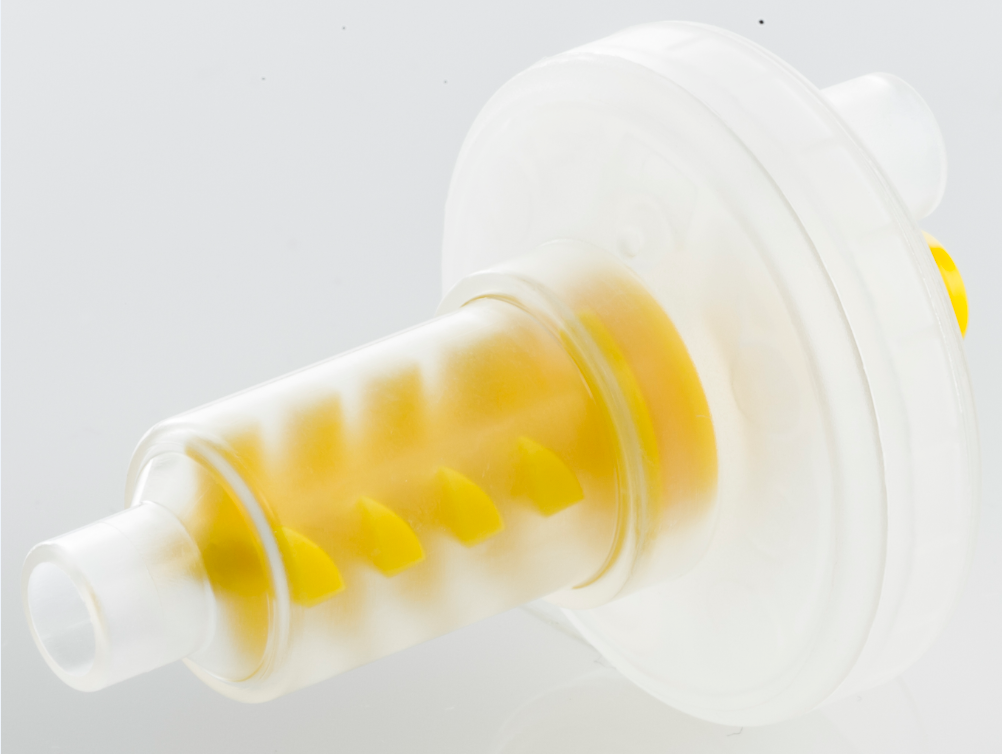
Dynamische Mischkanüle für das 380ml System, Ratio 5:1 (Bild: Sulzer Mixpac Ltd.)