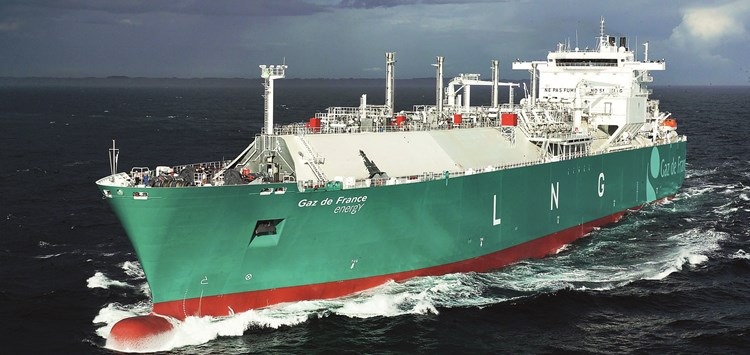
LNG-Membrantanker (Bild: Ives Guillotin)
16.09.2019 Nachhaltig dicht und eiskalt über die Weltmeere
Isolierung von LNG-Membrantankern durch Vorbehandlung mit Atmosphärendruckplasma
Wenn drei riesige Flüssigerdgastanker auch noch nach dreizehn Jahren sicher auf den Ozeanen unterwegs sind, so haben eine atmosphärische Plasma-Düsentechnologie und die Zusammenarbeit deutsch-französischer Ingenieure bei der Realisierung des sicherheitsrelevanten Klebprozesses der Tankisolierung entscheidend dazu beigetragen.
Verflüssigtes Erdgas oder abgekürzt LNG (Liquified Natural Gas) zählt laut Expertenmeinung zu einem der wachstumsstärksten Energieträger weltweit. LNG entsteht, indem man Erdgas auf -161 bis -164 °C tiefkühlt, es sich bei dieser Temperatur verflüssigt und jetzt aufgrund der Erhöhung seiner Dichte nur noch ein Sechshundertstel seines Volumens im gasförmigen Zustand besitzt. In dieser komprimierten Form eignet es sich ideal zur Lagerung in speziellen LNG-Export- und Import-Terminals und zur Beförderung in Tankern.
LNG, das hauptsächlich aus Methan besteht, ist farblos, geruchlos und ungiftig. Auch ist es nicht zündfähig, im Gegensatz zu dem sich bei einer Erwärmung entwickelnden Gas im Gaszustand, welches in Verbindung mit einem bestimmten Anteil Sauerstoff explosive Gemische bilden kann. LNG-Tanker sind die flexible Alternative zum Transport von Erdgas in Pipelines. Da sie das Flüssigerdgas auf den Weltmeeren über weite Strecken und in großen Mengen von ihren Verflüssigungsterminals zu den Regasifizierungsterminals befördern, müssen sie extrem gut gedämmt und absolut dicht sein (Bild 1). Bei Membrantankern muss die über die Tankerwand eindringende Wärme der Außenluft so gering wie möglich gehalten werden, da jede Wärmezufuhr zu einer Verdampfung des verflüssigten Gases und damit zu einer Erhöhung des Innendrucks des Tanks führt. Der Anteil des – trotz aller Isoliermaßnahmen – ständig abgasenden Methans, das „Boil-off-Gas (BOG)“, wird gezielt aus den Tanks abgeführt und entweder sofort als Kraftstoff für das Schiff genutzt oder unter hohen Sicherheitsvorschriften in die Atmosphäre abgefackelt. Die in die Isolationsebenen eingebauten Membranen dienen als Sperrschichten. Ihre alles entscheidende Aufgabe ist es, zu verhindern, dass das tiefgekühlte Flüssigerdgas durch eine undichte Stelle entweicht und mit der Stahlstruktur des Schiffsrumpfes in Kontakt kommt. Schon geringste Leckagen könnten zu einer Versprödung des tragenden Baustahls führen und ihn zerstören.
Wie langzeitstabil und dauerhaft dicht eine ursprünglich nicht haften wollende Verklebung der Dichtungsebene nach einer Vorbehandlung mit Atmosphärendruckplasma (AD-Plasma) sein kann, zeigt das Beispiel eines weltweit einzigartigen Einsatzes dieser Vorbehandlungsmethode: Auf einer Gesamtlänge von mehr als 100 km sicherte die Plasma-Düsentechnologie Openair-Plasma in den Jahren 2005 und 2006 die Dichtigkeit der Dämmplattenisolierung beim Bau der beiden damals größten LNG-Tanker sowie ihrem kleineren Schwesterschiff (Bild 2).
Die Tanker lassen sich in fünf wesentliche Sektoren unterteilen. Im hinteren Schiffsteil befindet sich der Maschinenraum. Ihm vorgeordnet sind hintereinander vier hochisolierte, in den Schiffskörper integrierte und der Schiffsform weitgehend angepasste Tanks. Die Membransysteme sind nicht selbsttragend, die Doppelhülle des stählernen Schiffsrumpfes bildet die eigentlich tragende Tankstruktur.
Membransystem CS1
Beim Bau der drei Schiffe wurde zum ersten Mal die von GTT (Gaztransport & Technigaz) entwickelte Isolationstechnik CS1 eingesetzt. Sie ermöglicht, die Komplexität der Isolierschichten und deren Dicke so zu reduzieren, dass bei Beibehaltung der Schiffsgröße die Tankerkapazität um 8.000 m3 gesteigert werden kann. Die Schiffsklassifikation fordert bei Membrantankern eine doppelte Barriere gegen den Durchtritt von Flüssiggas bis zum Stahlschiffskörper. Überwacht werden die Membranen mit Sensoren. Die Gesamtkonstruktion des CS1-Systems hat vier Ebenen:
• Barriere 1: Die innere, undurchlässige Metallmembran bildet den eigentlichen Ladungsbehälter, steht also in direktem Kontakt mit dem Flüssigerdgas (Bild 3). Diese erste Sperre besteht aus einem 0,7 mm starken, gut isolierenden Invar-Stahl, einer Legierung mit einem sehr geringen Temperaturausdehnungskoeffizienten. Die durch die extremen Temperaturunterschiede zwischen dem -163° kalten Gas und der rd. 20 °C warmen Außenhülle entstehenden Spannungen werden dadurch ausgeglichen. Hinter der Stahlmembran liegt eine Isolierschicht aus Sperrholz und einem 10 cm dicken Polyurethan-Schaumstoff.
• Barriere 2: Es folgt eine steife „Triplex“-Platte. Sie ist das eigentliche Charakteristikum der CS1-Technologie (Bild 4), denn bisher wurde bei Membrantankern auch die zweite Sperre aus Invar-Stahl gebildet. Ihre Aufgabe ist, eventuelle Undichtigkeiten der ersten abzusichern, also zu verhindern, dass im Fall einer Leckage des Tanks das extrem kalte Flüssigerdgas mit der Stahlwandung des Schiffsrumpfes in Verbindung kommt, was zu einem Versprödungsbruch führen würde.
• Der Aufbau: Dieser besteht aus zwei äußeren Glasfaserkomponenten und einer dazwischenliegenden dünnen Aluminiumschicht. Der Materialverbund bildet zusammen mit den zur Fugendichtung per Verklebung aufzubringenden flexiblen Triplex-Bändern die zweite undurchlässige Membran. Zwischen der Triplex-Barriere und der Innenseite des doppelwandigen Metallrumpfs des Schiffes liegt eine weitere 20 cm dicke Schicht aus geschäumtem Polyurethan. Der isolierende Werkstoffverbund wird direkt auf die Innenseite der doppelten Metallhülle des Schiffes geklebt.
Baubeginn und -stopp
Der Bau der neuen Tankerserie begann in St. Nazaire mit der Gaz de France Energy. Ihr geplanter Ausliefertermin war für Ende 2004 angesetzt. Doch dann ein gravierendes Problem: Bei dem im Grunde schon fertiggestellten Schiff wurden plötzlich Undichtigkeiten in der zweiten Sicherheitsbarriere (Kunststoffverbund) des CS1-Membransystems festgestellt, was die sofortige Einstellung der Restarbeiten bedeutete. Einem Bericht des maritimen Nachrichtenportals „Mer et Marine“ [1] zufolge, dauerte es Monate, bevor die Ingenieure und Techniker die genaue Ursache der Havarie ermitteln konnten. Schließlich das Ergebnis: Den für die Fugendichtung der Verbundplatten verklebten flexiblen Triplex-Bändern fehlte es an der ausreichenden Haftung.
Auch bei der sich zu diesem Zeitpunkt bereits im Bau befindlichen Provalys mussten die Arbeiten unterbrochen werden. Nichts ging mehr, bevor nicht eine Lösung des Dichtungsproblems gefunden war. Für die Werft waren die Folgen der Baustopps immens: Verbindliche Liefertermine konnten nicht eingehalten werden, die Arbeit stand still und Vertragsstrafen in Millionenhöhe wurden fällig.
Schadensursache und Lösung
Will ein geeigneter Klebstoff auf einem zusatzfreien Kunststoff nicht haften, so kann man mit ziemlicher Wahrscheinlichkeit davon ausgehen, dass seine Oberfläche entweder nicht wirklich sauber oder die Oberflächenenergie für eine homogene Benetzung mit dem Klebstoff nicht ausreichend ist. Im Fall der LNG-Tanker kam beides zusammen, doch der Hauptfaktor war die durch die Arbeiten entstandene, nicht sichtbare Schmutzbelastung der Umgebungsluft. Die Umgebungsatmosphäre in einem Testlabor
entspricht nun einmal nicht der realen Situation. Die Umweltbedingungen beim Schiffsbau ähneln eher denen einer Beton-Großbaustelle und es wurde klar, dass die Klebprozesse der Isolierungsarbeiten zum einen nur unter Einsatz aufwändiger Ventilationssysteme und Klimaanlagen fortgeführt werden konnten, zum andern, dass darüber hinaus eine Vorbehandlung aller Klebstellen erforderlich wurde. Doch die dafür richtige Methode zu finden, erwies sich als schwieriger als erwartet. Weder brachten eine Vorbehandlung mit einem Primer, noch eine Beflammung der Oberflächen das gewünschte Haftungsergebnis.
Hier erinnerte man sich an ein Plasmaverfahren für schwierige Klebprozesse, das auch bereits erfolgreich in der französischen Automobilindustrie eingesetzt wurde – das Openair-Plasma-Verfahren von Plasmatreat.
Die Evaluation der Technologie ergab, dass die Plasmabehandlung nicht nur beste Haftungsergebnisse erzeugte, sondern auch sämtliche Umwelt-, Sicherheits- und Effizienzbedingungen erfüllte. Ab jetzt ging es voran. In Zusammenarbeit mit den Ingenieuren des Schiffsbauers sowie den Maschinenspezialisten Servisoud und ASI lieferte Plasmatreat zwischen März 2005 und April 2006 an Chantiers de l‘Atlantique zwanzig “Plasma-Roboter“, die mit ihrer Anpassungsfähigkeit die großen Flächen bearbeiten konnten.
Schritt eins – Plasmabehandlung im Megaformat
Die Vorbehandlungslösung mit Atmosphärendruckplasma war weltweit der erste großflächige Einsatz von in Roboter integrierten rotierenden Plasmadüsen. Die Anwendung erfolgte auf dem Niveau der zweiten Barriere. Es ging darum, den Klebeprozess für Tausende von flexiblen Triplex-Bändern vorzubereiten. Die Bänder hatten eine Breite von 30 cm und eine Gesamtlänge von ca. 40.000 m pro Großtanker. Mit ihnen sollten die Kanten-Nahtstellen der 1x3mgroßen Isolierplatten mittels eines 2K-Epoxid-Klebstoffes zum Zwecke der vollständigen Dichtigkeit überklebt werden.
Für den Vorbehandlungsprozess fixierten die Mitarbeiter für den Roboter vor der Arbeitsfläche zunächst eine 3 m lange Hilfsschiene. Nach Programmierung von Start- und Endpunkt steuerte der Roboter den exakten Arbeitsablauf der Düse und fuhr sie vollautomatisch mit einer Geschwindigkeit von 6 m/min und einem Abstand (Düsenkopf/ Oberfläche) von 10 mm über die zu behandelnde Oberfläche. Plasma übt auf Kunststoffoberflächen eine mehrfache Wirkung aus. Zum einen bewirkt die Mikroreinigung die Zerstörung sämtlicher auf der Oberfläche vorhandenen organischen Substanzen. Lose anhaftende Staubpartikel werden gleichzeitig durch die hohe Ausströmungsgeschwindigkeit des Plasmas entfernt. Da der Kunststoff durch die Plasmabehandlung zudem statisch entladen wird, werden Stäube aus der Umgebungsluft nicht mehr angezogen. Des Weiteren bewirkt das Plasma die simultane Aktivierung der Oberfläche, das heißt, ihre Modifizierung auf molekularer Ebene. Die Haftungseigenschaften des Materials werden hierdurch positiv verändert. Unpolare Kunststoffe werden polar und ihre Oberflächenenergie erhöht sich dadurch soweit, dass eine homogene Benetzbarkeit mit einem Klebstoff und dessen langzeitstabile Haftung gegeben sind (Bild 5).
Schritt zwei: Der Klebprozess
Vorbehandlung und Verkleben konnten nur Stück für Stück erfolgen, was bedeutete, dass das Team nach jedem Vorbehandlungsprozess die Hilfsschiene wieder abmontieren
und sie an der nächsten zu behandelnden Fläche neu aufbauen musste. In einem zweiten, sich unmittelbar an die Vorbehandlung anschließenden Schritt wurde von einem anderen Arbeitsteam der eigentliche Klebprozess durchgeführt: Alle zuvor mit Plasma feinstgereinigten und aktivierten Plattenkanten wurden nun mit dem Triplex-Band fugendicht überklebt.
Der von der Werft betriebene Aufwand lässt sich an der eingesetzten Manpower ablesen: Dreihundert speziell für die Herstellung dieser Isolationsschicht geschulte Mitarbeiter arbeiteten in drei 8-h-Schichten rund um die Uhr und fertigten in einer Woche bis zu 3,5 km Bandverklebung. Insgesamt reinigten und aktivierten die Plasmasysteme eine Fläche von 12.000 m2 pro Großtanker (Bild 6).
Fazit
Mit dieser Anlagentechnik wurde eine Lösung geschaffen, die die für die Triplex-Klebprozesse erforderliche Oberflächenbehandlung direkt auf der Baustelle unter besten
Bedingungen ermöglichte. Während die Energy aufgrund des langen Stillstands mit einer Verspätung von etwa zwei Jahren ausgeliefert wurde, trat der Großtanker Provalys im November 2006 seine Jungfernfahrt mit einjähriger Verspätung an. Das Schwesterschiff Gaselys hatte von Baubeginn an von dem neuen Vorbehandlungsprozess profitiert und lief Anfang 2007 vom Stapel.
Zwar sind die drei Schiffe die einzigen Tanker, die bis heute mit der CS1-Membrantechnik ausgestattet wurden[2], doch die enge deutsch-französische Zusammenarbeit in der damaligen Notsituation hat sich ausgezahlt und die durch die Openair-Plasma-Technik erzielte hohe Haftung der Klebverbindungen hat ihre Langzeitstabilität unter Beweis gestellt. Auch noch nach 13 Jahren verschifft das Trio Riesenmengen an eiskaltem Erdgas über die Weltmeere – und das sicher noch viele weitere Jahre. Denn anders als Öltanker, die meist nach 20 bis 25 Jahren abgewrackt werden, ist die Lebensdauer eines LNG-Tankers auf mehr als 40 Jahre ausgerichtet.
Literatur:
[1] www.meretmarine.com/article.cfm?id=110118 [2] www.lngworldshipping.com/news/view,gtt-andcat-settle-decadelong-cs1-disputes_41218.htm
Fakten für Konstrukteure
• Auch große Klebflächen lassen sich mit der Openair-Plasma-Technologie effektiv vorbehandeln
• Labortests lassen sich nur begrenzt in die Praxis übertragen - vor allem bei rauen Produktionsbedingungen
Fakten für Einkäufer
• Die frühzeitige Einbindung aller relevanten Partner auf der Basis praxisnaher Tests spart viel Geld, wie dieses Beispiel zeigt
Fakten für Qualitätsmanager
• Das gewählte Verfahren sorgt über Jahre hinweg für die notwendige Sicherheit
Das Bauprojekt
Im Jahr 2002 erhält die französische Werft Chantiers de l’Atlantique in St. Nazaire, die zu den größten Schiffbauunternehmen der Welt zählt und aus deren Docks berühmte Schiffe wie der Transatlantikliner Queen Mary 2 stammen, vom Energieriesen Gaz de France (heute Engie SA) den Auftrag zum Bau von drei modernen LNG-Membrantankern. Die Schwesterschiffe Provalys und Gaselys sollen mit einer Länge von 290 m, einer Breite von 43,5 m, einer Höhe von 50 m und einem Ladevolumen von ca. 153.000 m³ nach Fertigstellung die zu jener Zeit größten LNG-Tanker der Welt werden. Der dritte Tanker, die Gaz de France Energy (heute GDF SUEZ Global Energy), hat mit ca. 74.000 m³ ein um etwa die Hälfte kleineres Ladevolumen als ihre gigantischen Schwesterschiffe, gehört aber mit ihren ca. 220 m Länge und ca. 35 m Breite auch schon zu den großen.
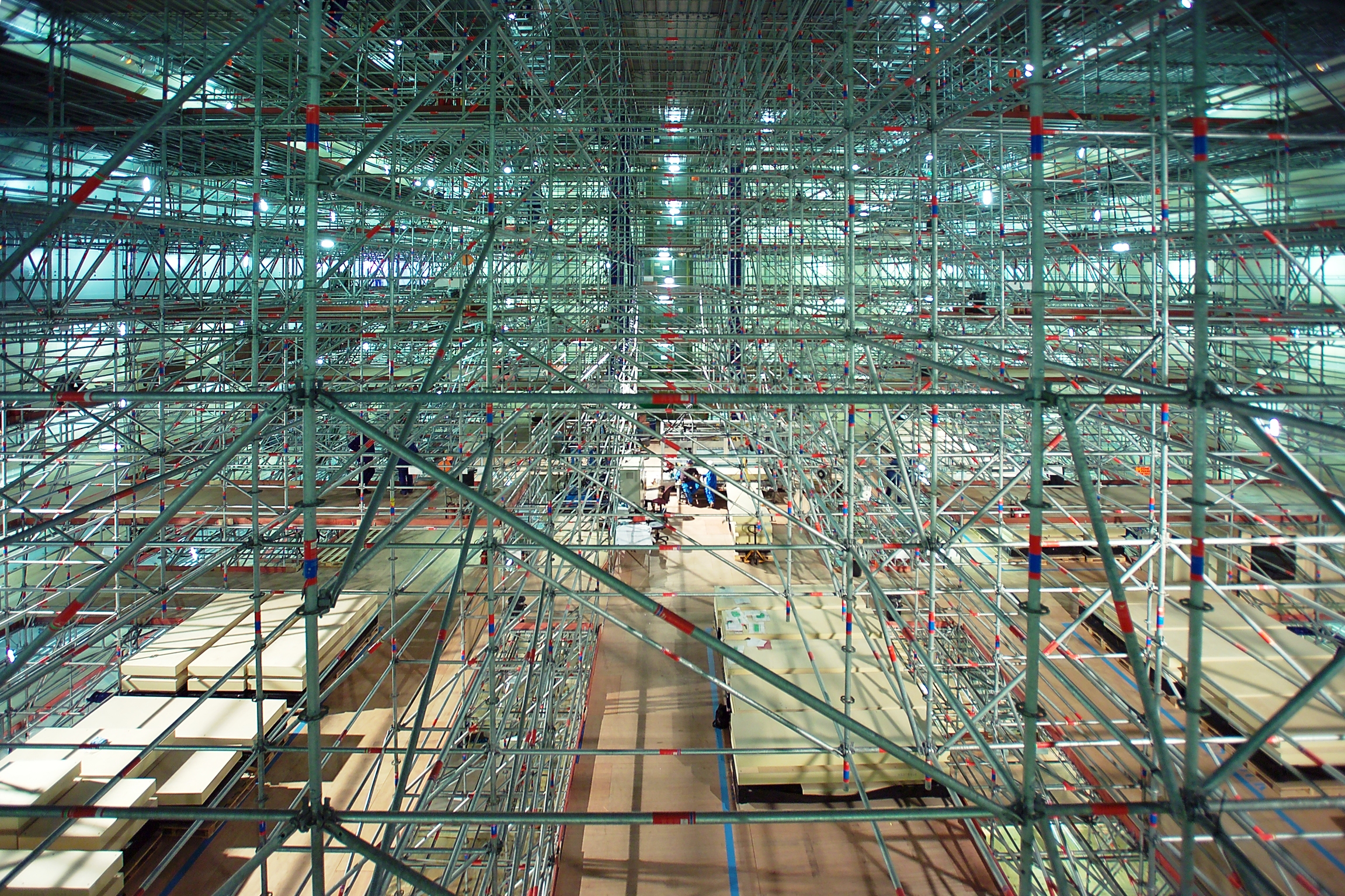
Bild 2: Im Bauch des Giganten: Auf der Großbaustelle des 290 m langen, 43 m breiten und 50 m hohen Tankers Prowvalys bereiten Arbeiter die Dämmung der Schiffsaußenhülle vor (Bild: Yves Guillotin)
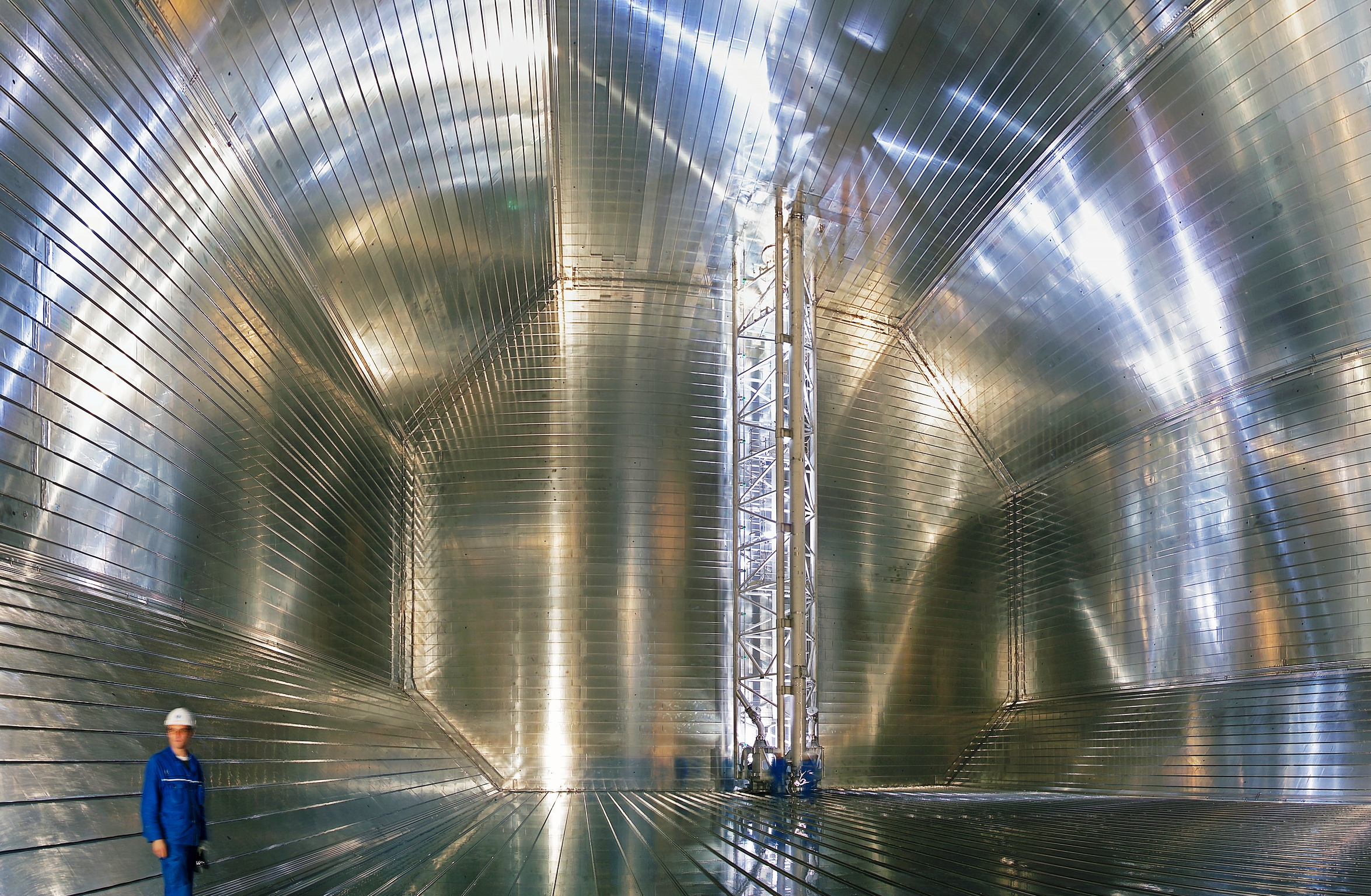
Bild 3: Die innere, undurchlässige Metallmembran aus Invar-Stahl bildet die 1. Barriere und den eigentlichen Ladungsbehälter. Sie steht in direktem Kontakt mit dem auf -163 °C verflüssigten Erdgas
(Bild: Yves Guillotin)
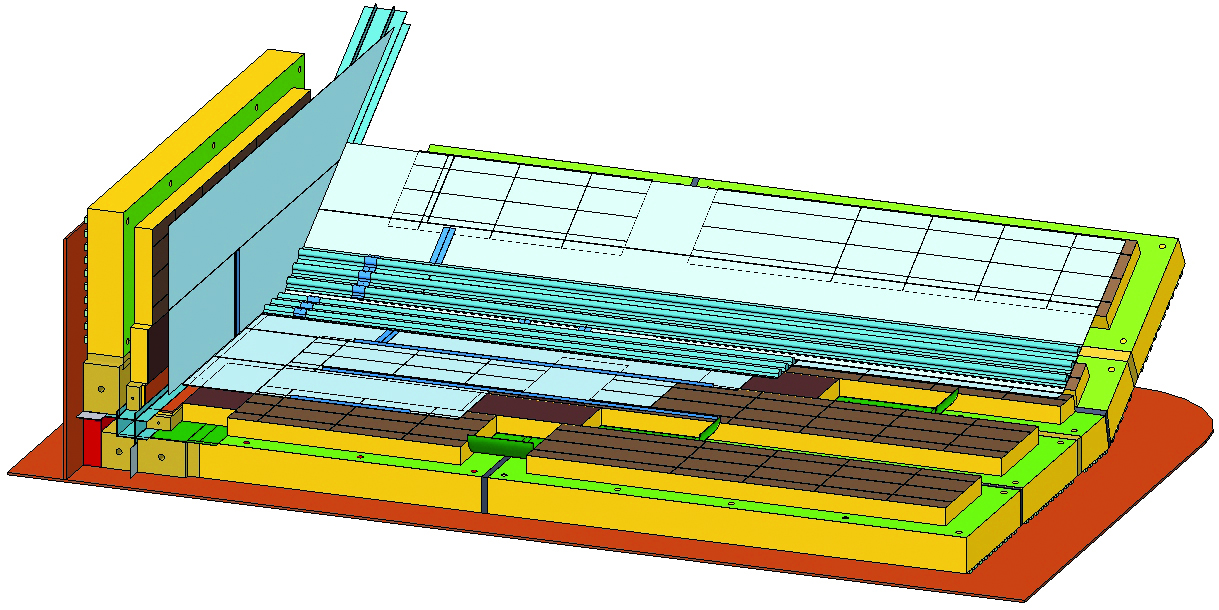
Bild 4: Die Schiffsklassifikation fordert bei Membrantankern eine doppelte Barriere gegen den Durchtritt von Flüssiggas bis zum Stahlschiffskörper. Eine undurchlässige Kunststoff-Triplex-Schicht ist das eigentliche Charakteristikum der CS1-Technologie (2. Barriere) (Bild: Plasmatreat)
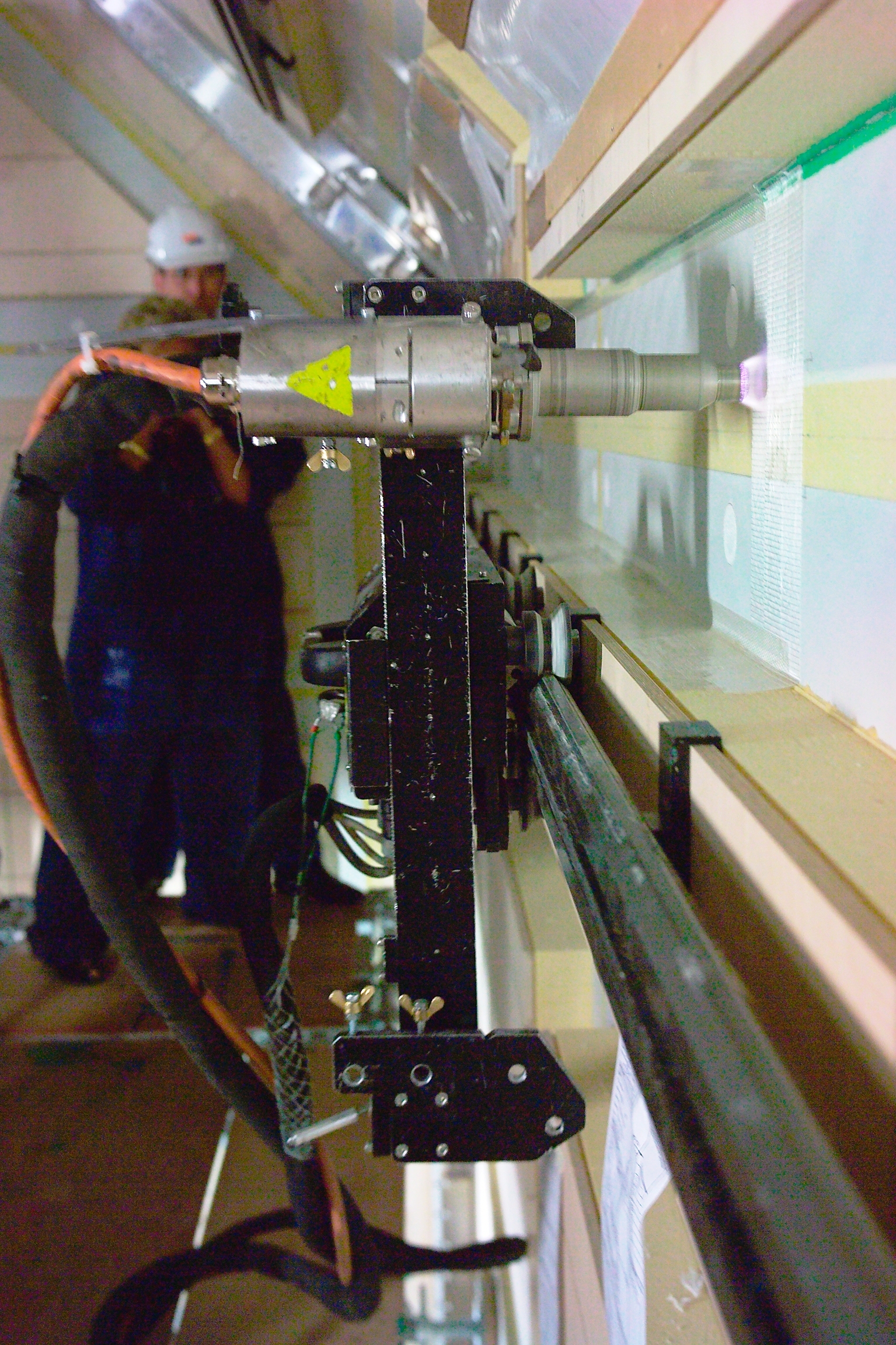
Bild 5: Was Primer und Beflammung nicht schafften, gelang mit Atmosphärendruckplasma: Die langzeitstabile Haftung der verklebten flexiblen Triplex-Dichtungsbänder (Bild: Yves Guillotin)
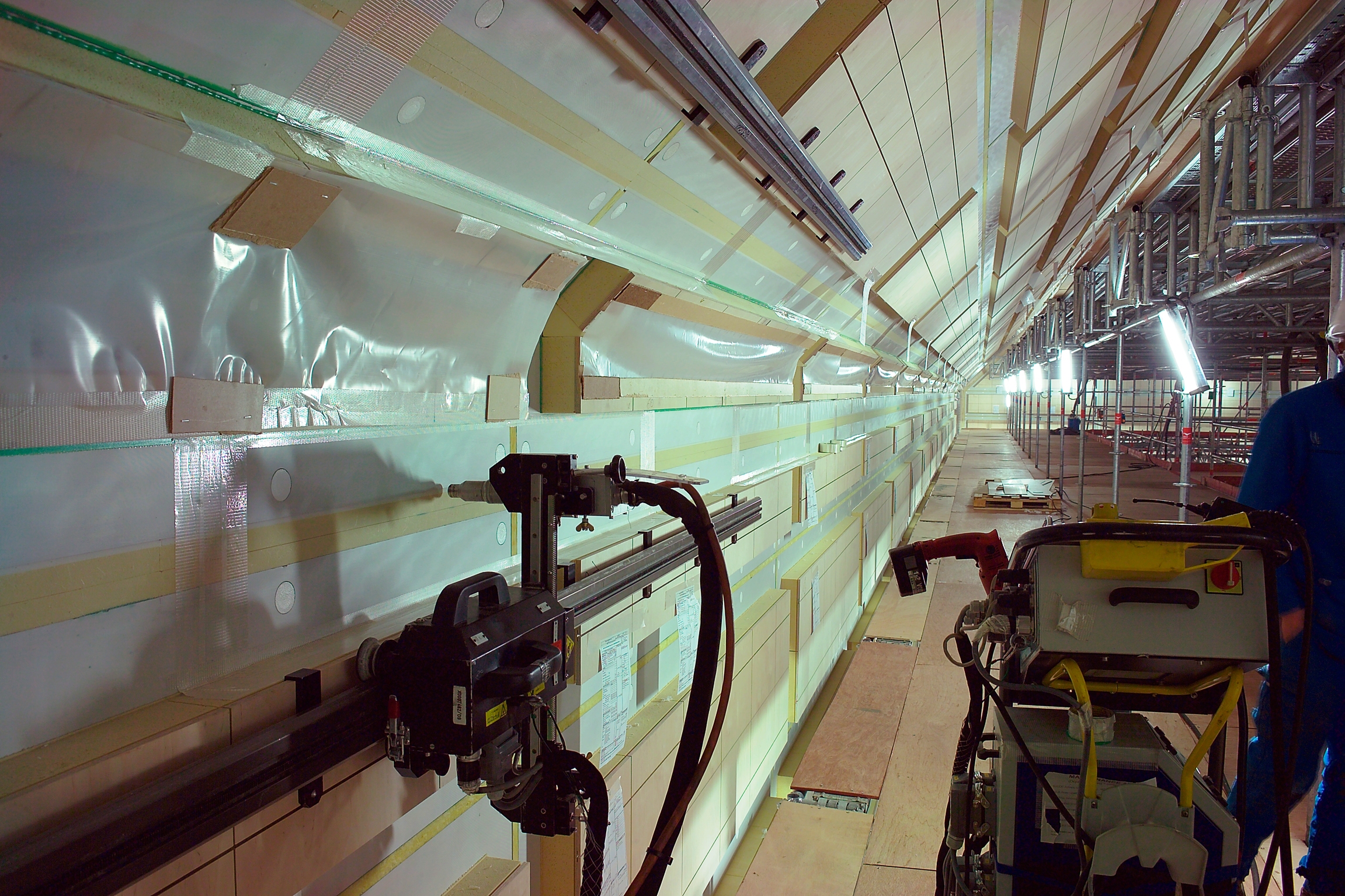
Bild 6: Insgesamt reinigten und aktivierten die robotergesteuerten Openair-Plasma-Systeme eine Fläche von 12.000 m2 pro LNG-Großtanker
(Bild: Yves Guillotin)