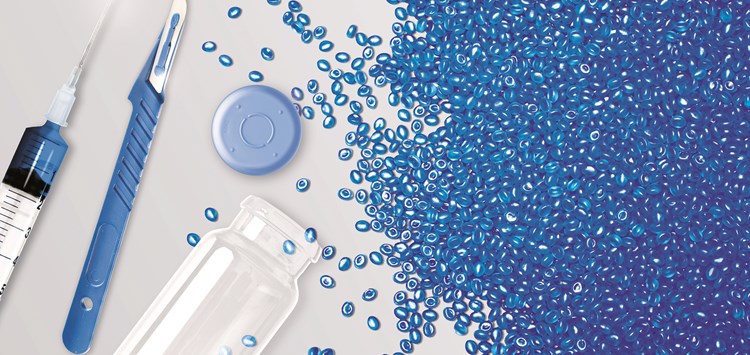
Medizinische Teile aus TPE tragen heute in hohem Maße zur Hygiene bei (Bild: ACTEGA DS)
04.06.2018 Klinisch saubere Lösungen
TPE-Teile mit Dichtungsfunktionen
Die Hygiene ist in unserem Gesundheitssystem ein permanentes Thema. Ohne moderne und dichte Verschlüsse, Membranen und Leitungen aus TPE und ihre prozesssichere Produktion wären die Probleme wahrscheinlich noch größer.
Medizinische Teile unterliegen den strengsten Qualitätstests – von der Entwicklungsphase bis zur Produktion in hohen Stückzahlen. So ist auch für Konnektoren, Ventil- oder Verschlussmembranen, Infusionsleitungen, Ports, Stopfen oder Überleitungssysteme – kurz, für alle Arten von pharmazeutischen Verschlüssen, eine Vielzahl von Ansprüchen zu erfüllen. Das hierfür eingesetzte Material muss – neben anderen wichtigen Eigenschaften – die Fähigkeit des vollständigen Wiederverschlusses aufweisen und alle gängigen Arten von Sterilisationsverfahren ohne signifikante Veränderungen des Eigenschaftsprofils bestehen. Darüber hinaus muss die Partikelkontamination vermieden werden, d.h. es darf kein Material aus dem Kunststoff des Stopfens an der Kanüle haften bleiben.
Auch das Anforderungsprofil an das Dichtungsmaterial für Spritzenkolben »2 oder an die Dichtelemente von Katheterkupplungen ist äußerst umfangreich: Funktionalität, Sterilität und Migrationsarmut sind nur einige Stichworte. Ein entscheidendes Kriterium bei Spritzenkolben ist einerseits, eine konstante Dichtigkeit des Kolbens zu erhalten, andererseits, durch die Elastizität der Dichtung ein leichtes Gleiten des Spritzenzylinders für exaktes Dosieren ohne Slip-Stick-Effekt zu gewährleisten. Das Material muss den Anforderungen der EN ISO 7886 Norm zur Feststellung der Gleiteigenschaften, Dichtigkeit und Mechanik entsprechen. Der weiche Teil einer Katheterkupplung muss auf der einen Seite spezifizierten Zugkräften standhalten können, darf andererseits weder gequetscht noch sonst wie beschädigt werden. Darüber hinaus ist Sterilität gefordert. Wird dafür Gamma-Bestrahlung eingesetzt, darf dies nicht zu Undichtigkeiten, Funktionsstörungen oder Alterungserscheinungen führen.
Nur mit adäquaten Materialien lassen sich optimale Produktfunktionen erzielen. Durch entsprechende Formulierung der Werkstoff-Rezepturen kann die optimale Erfüllung der Anforderungsprofile garantiert werden, gleichzeitig können alle potenziell beeinträchtigenden Einflüsse eliminiert werden. Durch ein entsprechendes Verarbeitungsverfahren kann zudem die Qualität sichergestellt und die Sicherheit von Patient und Personal gewährleistet werden.
Umfangreiche Standards zu erfüllen
Grundsätzlich ist eine große Auswahl medizinisch nutzbarer Kunststoffe vorhanden, die zunächst alle den Medical Grade-Standard erfüllen müssen. Mit Medical Grade wird ein umfangreiches Eigenschaftsprofil umschrieben. Dazu gehören die geprüfte Biokompatibilität und physiologische Unbedenklichkeit. Für die Materialien müssen Untersuchungsergebnisse für die Biokompatibilität nach ISO 10993 und USP Class IV vorliegen. Dabei wird nicht nur die Erfüllung der technischen Anforderungen geprüft, sondern auch die Verträglichkeit des Materials mit dem menschlichen Organismus. Diese biologische Prüfung ist gemäß Medizinprodukte-Richtlinie MDD 93/42 EWG immer dann notwendig, wenn ein unmittelbarer Kontakt von Werkstoff/Produkt mit dem Patienten besteht. Chemische und Medienbeständigkeit sind weitere Merkmale – z.B. gegenüber gebräuchlichen Desinfektions- und Reinigungsmitteln. Und last not least ist auch die Sterilisationsfähigkeit von Bedeutung.
TPE im Mehrkomponenten-Spritzguss eröffnet interessante Perspektiven
Viele Kunststoffe sind jedoch sehr sensibel und können nur in einem engen spezifischen Prozessfenster verarbeitet werden. Hier können TPE durch die Möglichkeit ihrer thermoplastischen Verarbeitung, insbesondere in Mehrkomponentensystemen, eine entscheidende Rolle spielen. Unter Mehrkomponenten-Spritzguss versteht man das sequenzielle Zusammenbringen mehrerer Schmelzen (Kunststoffe) während des Spritzgießvorgangs. Dazu werden verschiedene polymere Werkstoffe – auch in unterschiedlichen Farben – in einem Formwerkzeug und Arbeitsgang durch Spritzgießen miteinander verbunden. Die erzielten Verbunde können unlösbar, aber auch gegeneinander beweglich sein. Die Vorteile sind Verbindungen verschiedener Materialien oder Farbelemente und die Einsparung aufwändiger Montagevorgänge. Die Verträglichkeit der Kunststoffe zueinander und die besondere Anforderung an die Haftung beeinflussen maßgeblich die Qualität dieser Verbindung zwischen Hart- und Weichkomponente, die wiederum diversen Einflussfaktoren unterliegt. Dazu gehören die Polarität der Fügepartner, die Oberflächenstruktur und -güte sowie die chemische Grundstruktur des Kunststoffes sowie die Fließfähigkeit des Materials.
Für eine bessere Haftung von TPE an Materialien wie PC und ABS ist daher die Einarbeitung haftungsfördernder Komponenten in die TPE-Rezeptur und die Reduktion von sich nachteilig auf die Haftung auswirkenden Elementen notwendig. Die durch Modifikation der Werkstoffe erreichbare Verbundfestigkeit haftungskompatibler Kunststoffkombinationen ist bei mechanischer Beanspruchung und bei Medieneinwirkung von besonderem Interesse und daher auch für die Bereiche Medizintechnik und Pharmazie interessant. Der Einsatz von TPE-Compounds im Mehrkomponenten-Spritzguss kann die Anzahl der Prozessschritte verkürzen, senkt die Fehlerquote und steigert die Produktionssicherheit.
Die TPE-Rezepturen für das PROVAMED®-Portfolio von Actega DS sind sowohl für die Extrusion als auch für die Verarbeitung im Mehrkomponenten-Spritzguss ausgerichtet und weisen sehr gute Haftungseigenschaften auf einer Vielzahl von Kunststoffen auf. Darüber hinaus wurde auf niedrigstes Migrationspotenzial, Biokompatibilität, Sicherheit vor Schleimhautirritationen, PVC-, Phthalat-, Silikon- und Latex-Freiheit geachtet. Die TPE sind FDA-konform, schwermetallfrei, sterilisierbar und weisen Self-Sealing-Eigenschaften aus.
Darüber hinaus werden auch wichtige Faktoren wie einfache Verarbeitung, Kosteneffizienz, niedrigerer Abfallanteil während der Produktion und Recycelbarkeit erfüllt. Mit einem sehr niedrigen Migrationspotenzial und Verzicht auf PVC und Weichmacher sind TPE eine saubere Lösung für die Herstellung von Dichtungsmaterialien, Durchstechsepten, Stopfen und Verschlüssen.
Fakten für Konstrukteure
• Für die unterschiedlichsten Aufgabenstellungen stehen optimierte TPE-Compounds zur Verfügung
• Biokompatibilität, PVC-, Phthalat-, Silikon- und Latex-Freiheit etc. sind Standard.
Fakten für Einkäufer
• Die Verarbeitung von TPE im Mehrkomponenten-Spritzguss erlaubt Einsparungen in der Produktion und bei der Montage der Dichtelemente
Fakten für Qualitätsmanager
• Moderne TPE für Medizin- und Pharmaanwendungen erfüllen alle relevante Normen

»2 Dichte Entnahme von Arzneien (Bild: ACTEGA DS)