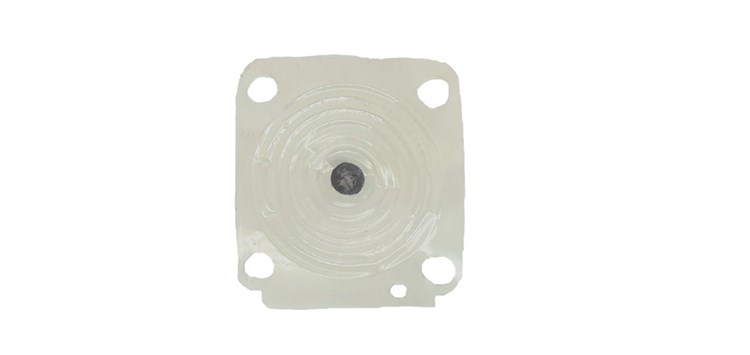
Neue PEEK-Membran nach der Evaluation verschiedener Möglichkeiten (Bild: Dätwyler AG)Bild: Dätwyler AG)
29.11.2019 Die Verfügbarkeit von motorisierten Arbeitsgeräten steigern
Dauerhafte Qualität mit PEEK-Membranen
Viele mobile, motorisierte Arbeitsgeräte beziehen ihre Energie von einem Zweitaktmotor. Ein Knackpunkt für die Standzeiten dieser Geräte ist die Haltbarkeit der Vergaser, oder genauer ihrer Bauteile, weshalb ein neuer Ansatz für Design und Fertigung von Vergasermembranen aus PEEK entwickelt wurde.
Die Aufgabe eines Vergasers ist es, den Kraftstoff zu zerstäuben und ihn entsprechend des Betriebszustandes im richtigen Verhältnis mit Luft zu mischen. Während des Ansaugtaktes wird Luft in den Verbrennungsraum angesaugt, die dabei durch einen trichterförmigen Ansaugkanal strömt und so beschleunigt wird. Der Kraftstoff wird dann durch das Venturi-Prinzip durch das entstehende Vakuum an der dünnsten Stelle des Trichters angesaugt. Das Luft-Kraftstoff-Gemisch wird anschließend durch die Drosselklappe reguliert. Das Kraftstoffdosiersystem in einem Membranvergaser besteht aus vier Komponenten: der Dosiermembran, dem Dosierhebel, der Dosierfeder und der Einspritznadel. Die Dosiermembran muss präzise auf kleinste Veränderungen im Kraftstoffvakuum reagieren. Zur Kraftstoffdosierung ist die Membran am Dosierhebel befestigt, reagiert auf jeden Ansaugtakt des Motors und regelt so konstant, wie und wann die Einspritznadel den Einspritzkanal öffnet.
Nachteile herkömmlicher Membranen
Ein Blick auf die verwendeten Materialien veranschaulicht die Problematik herkömmlicher Vergaser-Membranen: Üblicherweise wird eine faserverstärkte Nitrilkautschukmischung verwendet, um einen größeren Bewegungsraum bei gleichzeitig hoher Festigkeit zu schaffen. Das Kernproblem dieser Membranen ist die hohe Quellung. Bild 1 zeigt diesen Effekt: links die ursprüngliche, unbenutzte Membran, in der Mitte eine gealterte, rechts eine von Dätwyler produzierte PEEK-Membran.
Interne Untersuchungen von Dätwyler haben ergeben, dass das Quellen des Gummis die Materialstruktur schädigt und so die Funktion der Membran stark beeinträchtigt; Fehlfunktionen des Motors sind die Folge. Gerade saisonale Nutzung und längere Lagerzeiten eines Geräts können diesen Effekt verstärken.
Den Treibstoff berücksichtigen
Der Markt für mobile, motorisierte Arbeitsgeräte ist derzeit teilweise durch hohes Wachstum, aber auch steigende Anforderungen gekennzeichnet. Ein Beispiel sind die südamerikanischen Märkte. Hier wird z.B. ethanolhaltiger Treibstoff verwendet, der sich dem Membranmaterial gegenüber wesentlich aggressiver verhält, als der in Europa verwendete. Im Laufe des letzten Jahrhunderts stieg die Produktion von Kraftstoffethanol in Brasilien um durchschnittlich 11,8 % pro Jahr. Doch die Verwendung von Ethanol in konventionellen Motoren hat einen deutlichen Nachteil: Ethanol begünstigt das Quellen von Gummikomponenten, indem es die Aufnahme von Kraftstoff ins Membranmaterial beschleunigt. Sobald dessen Sauerstoff in das Gummi eingedrungen ist, bricht er die Kohlenstoff-Kohlenstoff-Doppelbindungen des Gummis auf. Die Folge kann ein gefährlicher Kraftstoffaustritt sein. Hier mussten neue Lösungen gefunden werden, auch, da die Erwartungen der Kunden an Kosten und Wartungsfrequenz gestiegen sind. Dies führte dann zur Entwicklung einer neuen PEEK-Membran.
Warum PEEK?
PEEK steht für Polyetheretherketon, ein aromatisches Polyetherketon, das eine hervorragende Chemikalien- und UV-Beständigkeit aufweist, schwer entflammbar ist und im Vergleich zu anderen Thermoplasten eine sehr geringe Rauchentwicklung zeigt. Wird PEEK verstärkt, ist es ähnlich stabil wie Leichtmetall. Darüber hinaus ist PEEK biokompatibel. Aufgrund seiner Eigenschaften in Bezug auf Entflammbarkeit und Rauchentwicklung wird PEEK z.B. in der Luftfahrt eingesetzt. Seine Biokompatibilität macht es auch in der Medizintechnik zum beliebten Werkstoff. Weitere Anwendungsgebiete sind Warmwasserautomaten, chemische Apparate, elektronische Komponenten, thermische Abschirmung, Rohre, Kabelisolierungen, Dichtungen sowie diverse Vorrichtungen in der Automobilindustrie. Laut Herstellern von PEEK-Folien zeigt Polyetheretherketon keine Wechselwirkung mit Ethanol, konventionellem Benzin oder Motoröl und ist daher für den Einsatz in diesen Umgebungen geeignet.
Speziell gefertigt und getestet
Für das benötigte Material entwickelte Dätwyler eine spezifische, neue Fertigungstechnologie, mit der dünne, hoch entwickelte thermoplastische Werkstoffe sehr schnell und präzise verarbeitet werden können. Diese Technologie erlaubt eine hohe Präzision und verhindert eine Degradierung der Materialeigenschaften.
Während des gesamten Entwicklungsprozesses wurde eine Vielzahl von Funktionstests an Verbrennungsmotoren durchgeführt, die mit PEEK-Membranen im Vergaser ausgestattet wurden. Diese Tests wurden mit den Werkseinstellungen des Vergasers durchgeführt – lediglich die originale Membran wurde durch eine PEEK-Membran ersetzt. Alle Tests wurden in Zusammenarbeit mit FEV durchgeführt, einem renommierten Hersteller und Entwickler von Verbrennungsmotoren, der zahlreiche Prüfstände betreibt. In dem Programm wurden die Materialien unter folgenden Bedingungen getestet:
• Kaltstart
• Warmstart bei zwei verschiedenen Temperaturen
• Heißstart
• Volllast (Höchstdrehzahl des Motors)
Bild 2 zeigt beispielhaft die aus einem Test gewonnenen Daten für einen Warmstart bei 80 °C. Das erste Diagramm zeigt den Vergleich zwischen der speziellen PEEK-Membran (farbige Linien) und der originalen Membran (schwarze Linie). Es ist klar zu erkennen, dass das Ansprechverhalten des Systems auf die Membranen nahezu identisch mit der Originalmembran ist. Die zweite Grafik vergleicht das von einer externen Lambda-Sonde gemessene Luft-Kraftstoff-Verhältnis. Ähnlich wie beim ersten Diagramm gibt es auch hier nur sehr geringe Unterschiede, auch das Gesamtbild ist nahezu identisch. Ein ähnliches Bild zeigte sich über alle Testbereiche, was verdeutlicht, dass PEEK-Membranen herkömmliche Membranen unter allen Arbeitsbedingungen gleichwertig ersetzen können. Sowohl auf den Herstellungsprozess als auch auf das Membrandesign wurde ein Patent angemeldet. Bevor eine weiterführende Beurteilung der PEEK-Membran für kundenspezifische Anwendungen möglich ist, müssen noch weitere Tests durchgeführt werden, insbesondere Belastungstests im praktischen Einsatz.
Fakten für Konstrukteure
• Mit Hochleistungswerkstoffen wie PEEK lassen sich steigende Produktanforderungen an Dichtungen und Membranen in den Griff bekommen
• Tests mit der neuen Lösung können Anwender selbstständig durchführen oder in Abstimmung mit Dätwyler als Partner
Fakten für Einkäufer
• Mit dem Einsatz neuer Werkstoffe lässt sich die Kundenzufriedenheit einfach steigern, was sich positiv auf Image und Verkauf der Produkte auswirken kann
Fakten für Qualitätsmanager
• Richtig eingesetzt sorgen Hochleistungswerkstoffe für höhere Produktqualität und weniger Reklamationen
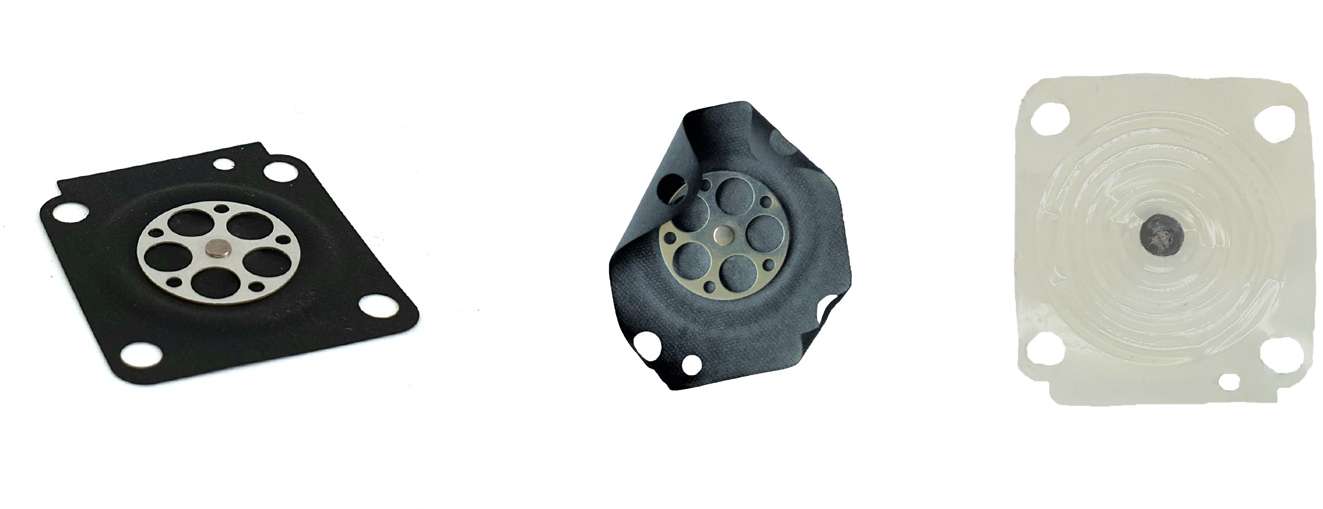
Bild 1: Im Vergleich: Originalmembran (links), benutzte/ gealterte Membran (Mitte) und PEEK-Membran (rechts) (Bild: Dätwyler AG)
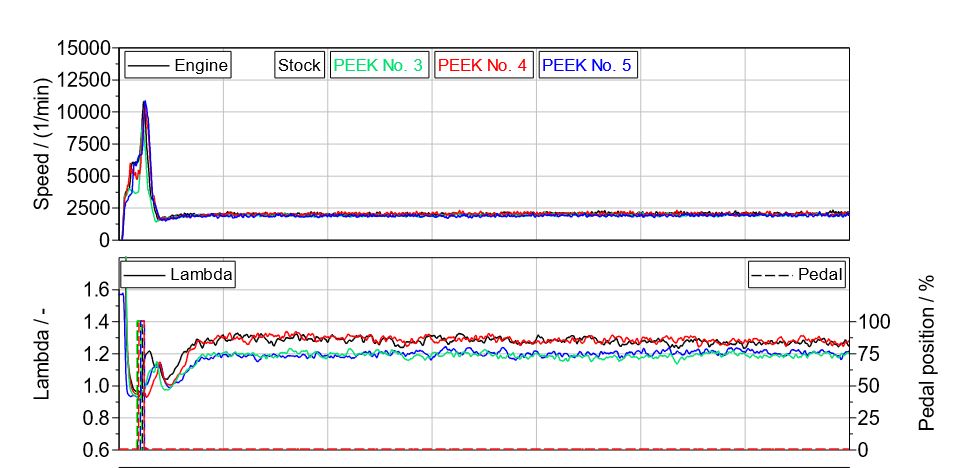
Bild 2: Testbeispiel: PEEK-Membranen und herkömmliche Membranen wurden bei 80 °C getestet (Bild: Dätwyler AG)