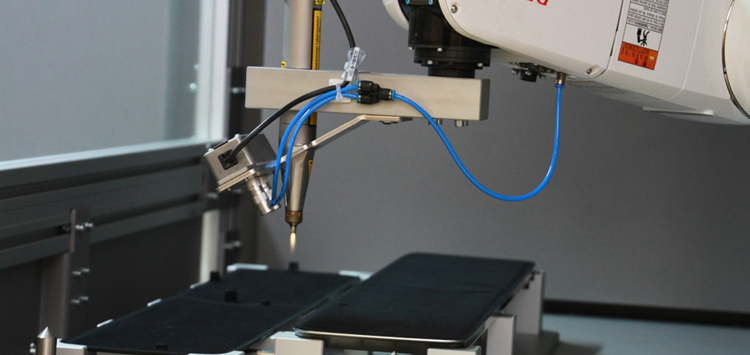
Atmosphärendruck-Plasmadüse mit optischer Plasmastrahlüberwachung in der Roboterzelle (Bild: Diener electronic GmbH & Co. KG.)
31.03.2018 Die Daten beherrschen
Auch für Plasmareinigungs- und Plasmaaktivierungsanlagen steigen mit Industrie 4.0 die Anforderungen
Bei hochautomatisierten Fertigungen steigen in Industrie 4.0-Konzepten die Anforderungen an die begleitende Datenverarbeitung in vielfacher Hinsicht. Moderne Plasmaanlagen sind darauf vorbereitet.
Egal, ob es moderne Autosensoren für die Druck- oder Temperaturmessung, andere elektronische oder Kunststoffkomponenten für Autos, Smartphones, Sportschuhe oder künstliche Organe sind – die Vorbereitungsprozesse zum Verkleben bzw. Bonden können oft nicht mehr ohne Plasmavorbehandlung realisiert werden. Darüber hinaus erfordert das Produzieren von Hightech-Massenprodukten in Europa einen hohen Automatisierungsgrad der Fertigung. Jeder Arbeitsschritt, der ohne menschliche Eingriffe abläuft, muss dabei zuverlässig überwacht werden. Und all diese Aspekte sind dann Voraussetzung für eine moderne Fertigung unter Industrie 4.0-Bedingungen mit dem Ziel einer zunehmend effektiveren Fertigung qualitativ hochwertiger Produkte.
Plasmatechnik, integriert in hochautomatisierte Fertigungsabläufe
Als sich die Plasmatechnik ab den 80er Jahren des letzten Jahrhunderts in der industriellen Fertigung zu etablieren begann, wurde die Automatisierung der Niederdruckplasmaprozesse zunächst mithilfe von SPS-Steuerungen und nur teilweise auf Windows basierter Software realisiert. Zu dem Zeitpunkt machte sich noch niemand große Gedanken hinsichtlich einer Prozessdokumentation. Dann folgte die Atmosphärendruckplasmatechnik. Sie erlaubte vollautomatische Prozessabläufe, die erstmals auch überwacht werden konnten (Bild 1). Anschließend haben Kurztakt-Anlagen, basierend auf der Niederdruckplasmatechnik, die Möglichkeiten automatisierter Fertigungslösungen abgerundet.
Heute soll eine Plasmaanlage – eine Plasmaprozessüberwachung ist gängiger Standard – mit anderen, in der Fertigungslinie verketteten Anlagen kommunizieren und Daten austauschen (Bild 2). Dies geschieht mithilfe einer Software auf Windows-Basis. Sie ermöglicht die Kommunikation mit anderen Fertigungssystemen. Ob dabei Niederdruck- oder Atmosphärendruckplasmasysteme zum Einsatz kommen, spielt keine Rolle. Ein Beispiel: Wird z.B. ein Produkt spritzgegossen und muss anschließend mit Plasma aktiviert oder gereinigt werden, fragt die Plasmaanlage zuerst beim vorherigen Fertigungslinienglied über den Linienrechner ab, ob der Ablauf des Spritzgussprozesses eines Bauteiles störungsfrei war. Erst wenn dies geschehen ist, kann die Plasmabehandlung gestartet werden. Wurde dieser Ablauf sauber protokolliert, folgen die weiteren Schritte eines Fertigungsprozesses.
Optimierung der Fertigung – auch unter Qualitätsaspekten
Fehlerhafte Prozessschritte werden in solchen Fertigungen sofort erkannt und in Richtung QS-Personal kommuniziert. Das Protokoll fehlerhafter Chargen, inkl. der Ursachen wird automatisch im Linienrechner und bei Bedarf im ERP-System gespeichert. Weitere Daten lassen sich per Tastatur eingeben oder mit einem Barcodescanner erfassen.
Mithilfe der Barcodes lässt sich auch die Fertigung steuern. Wurden vorab ein oder mehrere nummerierte Programme erstellt und mit einem Barcode verknüpft, können diese Codes ganz einfach per Barcodelesegerät einem Bauteil oder seiner Verpackung zugeordnet werden. Der gespeicherte Prozess startet dann automatisch.
Eine Erweiterung der Eingabehilfen sind RFID-Chips. Diese Chips lassen sich in die zu behandelnden Bauteile integrieren. Mit diesem System lassen sich nicht nur Prozesse steuern, sondern Prozessmeldungen, z.B. i.O. oder n.i.O. speichern. Bei der Bauteilbehandlung werden diese Chips nicht vom Plasma angegriffen und können für die weiteren Fertigungsschritte genutzt werden. Je nach Einsatz stehen diese Daten nach Herstellerangaben lebenslang im Produktkontext zur Verfügung und bieten so ein hohes Maß an Rückverfolgbarkeit.
Prozessdaten dokumentieren
Zu dokumentierende Daten entstehen auch beim Behandlungsprozess direkt. Für die Qualität von Plasmabehandlungen ist die Erfassung, Steuerung und Dokumentation aller wichtigen Prozessparameter entscheidend »3. Einerseits, um ggf. die Behandlung zu optimieren, andererseits, um im Zweifelsfall eine richtige Plasmaaktivierung der Klebeflächen nachweisen zu können. Dazu zählen z.B. der Prozessgasdruck in der Kammer, die Gasart, die Generatorleistung und die Prozesszeit bei einer Niederdruckplasmaanlage oder die Leistung und die Gasflüsse bei einer Atmosphärendruckplasmaanlage. Diese Basiswerte lassen sich durch produktionssicherheitsrelevante Messungen erweitern. Dazu gehören z.B. eine optische Plasmastrahlüberwachung, eine automatische Kontaktwinkelmessung, eine Oberflächenenergiemessung oder eine Erfassung der Plasmaindikatoren mithilfe einer Kamera.
Fazit
Die Integration von Plasmaanlagen in automatisierte Prozesse erfordert auch datenseitig eine hohe durchgängige Performance der Systeme. Industrie 4.0-Konzepte werden die Anforderungen in diesem Bereich noch mehr nach oben schrauben, wobei auch die Manipulationssicherheit hochintegrierter Fertigungssysteme immer mehr an Bedeutung gewinnen wird.
Fakten für Einkäufer
• Moderne Plasmasysteme lassen sich problemlos in hochautomatisierte Fertigungen und Industrie 4.0-Konzepte integrieren und tragen damit zur Wertschöpfung und Qualität der Produkte bei
Fakten für Qualitätsmanager
• Die integrierte Datenverarbeitung liefert gleichermaßen Daten für Produktoptimierungen durch ausfallsichere Verbindungen als auch Daten für die Fertigungssteuerung sowie Dokumentation des Qualitätsmanagements

»2 Kurztakt-Niederdruckplasmaanlage mit zwei Vakuumkammern und Linienrechneranbindung, installiert im Reinraum (Bild: Diener electronic GmbH & Co KG)

»3 Softwareoberfläche einer Atmosphärendruck-Plasmaanlage (Bild: Diener electronic GMBH & CO KG)