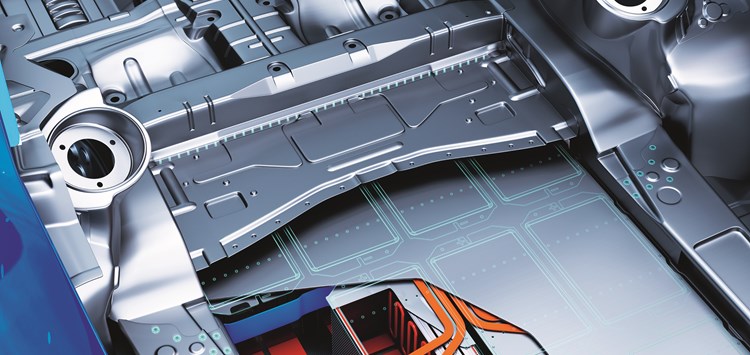
Zellen werden zu Zellstapeln werden zu Modulen werden zu einer ganzen Batterie: Die einzelnen Montageschritte umfassen Klebe- und Dosiertechnik, Stanzniet-, Schraub- und Fließlochschraubtechnik (Bild: Atlas Copco)
04.06.2018 Batterien effizient abdichten und montieren
Kleben, Flüssigdichtungen, Stanzniet- und Schraubtechnik sowie Fließlochschrauben sinnvoll kombinieren
Reibungslos funktionierende Batterien werden in modernen Fahrzeugen eine zentrale Rolle spielen. Bei ihrer Montage und Abdichtung verschiedene Fügetechniken in einem Montagekonzept zu kombinieren – dafür spricht einiges.
Die Automobilproduktion verändert sich gerade radikal. Ein Beispiel ist der weltweite Trend zur Elektromobilität. Der teilweise oder ausschließlich elektrische Antrieb von Fahrzeugen verändert die Konstruktionen schneller als jede andere Innovation der vergangenen Jahrzehnte. In den Antriebssträngen kommen zahlreiche unterschiedliche Batterietypen zum Einsatz, die alle bestimmte Aufgaben erfüllen müssen. Vor allem sind sie in puncto Langlebigkeit, Leistung und Sicherheit immer weiter zu verbessern. Denn die Batterie wird bei Elektroautos zu einem strukturellen Bestandteil, der bestimmte Funktionen übernehmen und bei einem Unfall Sicherheit bieten muss. Hier sind insbesondere intelligente Fügetechnologien gefordert, die einen produktiven Montageprozess mit einem leistungsfähigen Endprodukt ermöglichen.
Wie dies aussehen kann, zeigte Atlas Copco IAS bei der Eröffnung des neuen Innovationszentrums in Bretten und machte dabei auch deutlich, warum der Konzern hier verschiedene Fügetechnologien zusammenfasst. Das Konzept umfasst dabei u. a.:
- die Verklebung der einzelnen Batteriezellen zu Zellstapeln,
- die Fertigung der Zellmodule unter Einsatz des Stanznietens,
- das Auftragen einer Wärmeleitpaste mit einer speziellen Dosiertechnik,
- die Modulmontage mit einem Vierfach-Schraubsystem,
- die Abdichtung der Gehäuseabdeckung,
- die Montage des Deckels mit Fließlochschrauben.
Batteriezellen verkleben und die Stacks verstärken
Um die benötigte Energie bereitzustellen, müssen die prismatischen Zellen fest miteinander verbunden werden. Dazu ist eine präzise Klebeverbindung ohne Lufteinschlüsse notwendig. Das Fügen der Zellstapel (Stacks) ist deshalb eine Herausforderung, weil die Zellen temperaturempfindlich sind und über den Fügeprozess keine Hitze eingebracht werden darf. Eine weitere Anforderung ist es, die Zellen produktiv zu verarbeiten, d.h. schnell und sicher, damit die Stacks während des Montageprozesses oder durch Vibrationen im Fahrzeug nicht verrutschen können. Hier kommen Dosierlösungen aus der SCA-Produktlinie zum Einsatz, die einen 2K-Klebstoff schnell und prozesssicher verarbeiten können. Entscheidend ist hier, dass für das Aushärten keine äußere Hitze benötigt wird und die Fügestelle höchste Anforderungen an Steifigkeit und Crash-Verhalten erfüllt. Durch den Einsatz leicht elastischer Klebstoffe werden zudem Vibrationen während des Betriebs aufgenommen, was die Lebensdauer der Batterie erhöht.
Um die Batterie im Crashfall noch besser zu schützen, lassen sich die Zellstapel über seitlich angebrachte Streben verstärken. Dafür setzt man das Halbhohl-Stanznieten aus der Henrob-Produktlinie ein. Dieses kalte, rein mechanische Fügeverfahren hat den Vorteil, dass es keine Hitze in die Zellen einbringt und auch keine schädlichen Dämpfe oder Schweißspritzer verursacht. Der Stanzniet wird mit hoher Kraft und bei kurzer Taktzeit durch die zu fügenden Materialschichten getrieben. Eine Verstärkungsstruktur kann aus unterschiedlichen Werkstoffen und mehreren Schichten bestehen. Das bietet Konstrukteuren gleichermaßen eine hohe Designfreiheit und maximale Sicherheit.
Wärme sicher ableiten
Der effektive Betrieb von Batterien erfordert ein solides Temperaturmanagement. Die Batteriezellen müssen in einem definierten Temperaturbereich betrieben werden, um die Leistung zu erhalten und Überhitzung zu vermeiden. Dafür werden Wärmeleitpasten, die typischerweise mit Füllstoffen versetzt sind, mit hoher Präzision und unter Vermeidung von Lufteinschlüssen eingebracht. Die Dosierung dieser meist hochabrasiven Pasten ist nicht trivial und erfordert die richtige Technik und viel Know-how. Weil die abrasive Leitpaste zu höherem Verschleiß der eingesetzten Anlagenkomponenten führen kann, hat man hierfür eine entsprechend robust ausgelegte Pumpen- und Dosiertechnik entwickelt. Die Vermeidung von Lufteinschlüssen ist der eine wichtige Aspekt, der andere ist die exakte Dosierung der richtigen Menge. Denn die Pasten sind teuer, sie können bis 30 €/kg kosten und es werden große Mengen – teilweise bis 50 kg – pro E-Fahrzeug benötigt. Damit liegt in diesem Schritt ein hohes Kostenpotenzial. Deshalb werden die aufgetragene Menge, die Position sowie die Durchgängigkeit der Kleberaupe kontinuierlich optisch überwacht. Eventuelle Applikationsfehler werden so schnell erkannt und können umgehend korrigiert werden. Das hält die Zykluszeit kurz und senkt die Kosten für Nacharbeit und Qualitätssicherung. Grundsätzlich wird der ideale Auftrag der Wärmeleitpasten für jeden Batterietyp vorher in Versuchen ermittelt.
Damit die Wärmeleitpaste ihre Funktion ohne Lufteinschluss übernehmen kann, werden die aufgetragenen Pastenraupen mit elektronisch gesteuerter Schraubtechnik auf der definierten Fläche „ausgestrichen“. Von den vier Schraubspindeln aus der QST-Baureihe werden zwei anfangs stärker angezogen, wodurch die Paste in die gewünschte Form bewegt wird. Im Endanzug arbeiten sie dann synchron, was die Taktzeit verkürzt und jedes Modul gleichmäßig in der Wanne verankert. Die programmierte Schraubstrategie berücksichtigt so das Verhalten der flüssigen Leitpaste an der Fügestelle und stellt den optimalen Kontakt her. Durch den Einsatz „klassischer“ Schraubtechnik lässt sich diese Aluminium-Stahl-Verbindung zudem für den Wartungsfall wieder lösen.
Gehäuse abdichten
Sobald alle Module fest verankert sind, kann das Gehäuse verschlossen werden. Dabei ist zu verhindern, dass Feuchtigkeit eindringt. Sonst verschlechtert sich die Leistung der Batterie dramatisch und es kann zu Schäden und Korrosion kommen. Außerdem produziert eine Batterie gesundheitsschädliche Gase. Der Innenraum muss also absolut wirksam nach innen und außen abgedichtet werden. Mit bewährter Klebe- und Dosiertechnologie wird eine niederviskose Dichtnaht präzise, schnell und unterbrechungsfrei aufgetragen. Das kann entweder auf der Abdeckung oder auf dem Gehäuse geschehen. Weil die Batterie keinem Wärmeprozess ausgesetzt werden darf, eignen sich hier Materialien wie 1K-Heißbutyl, 2K-Polyurethan oder
2K-Silikon. So muss die Dichtung nicht im Ofen aushärten.
Im letzten Schritt wird die Abdeckung auf das Gehäuse gesetzt. Da das Batteriegehäuse hierfür nur von außen zugänglich ist, muss das Fügeverfahren darauf abgestimmt sein. Außerdem sollte auch diese Verbindung lösbar sein, um die Wartung und Demontage zu vereinfachen. Erfüllt werden diese Anforderungen von der Fließlochschraubtechnik. Das Verfahren bietet eine zuverlässige mechanische Verbindung, ist reversibel und benötigt nur einseitigen Zugang. Werkzeuge versetzen die Schrauben an der Werkstückoberfläche bei hohem Druck in eine schnelle Rotation. Dadurch erwärmt sich der Werkstoff an dieser Stelle und wird verformbar. Die Schraube wird durch die Werkstoffe Aluminium und Stahl gedrückt und schneidet abschließend ein Gewinde ein. Die metallischen Bauteile werden so leitend verbunden und formen einen Faradayschen Käfig, der elektromagnetische Interferenzen vermeidet.
Fazit
Mit diesem Ansatz wird deutlich, welche Vorteile sich aus einem zielgerichteten Technologie-Mix ergeben, der idealerweise aus einer Hand kommt. Das Beispiel der Batterien vermittelt einen Eindruck davon, wie aufwändig es wäre, das Know-how verschiedener Partner in einem solchen Konzept zu bündeln.
Fakten für Konstrukteure
• Ganzheitliches Konzept für die Montage und Abdichtung von Batterien
Fakten für Einkäufer
• Komplettsystem reduziert Fertigungsaufwand und Abstimmung zwischen Systempartnern
Fakten für Qualitätsmanager
• Die Ermittlung der jeweiligen Fertigungsparameter in Tests sorgt für hohe Qualität
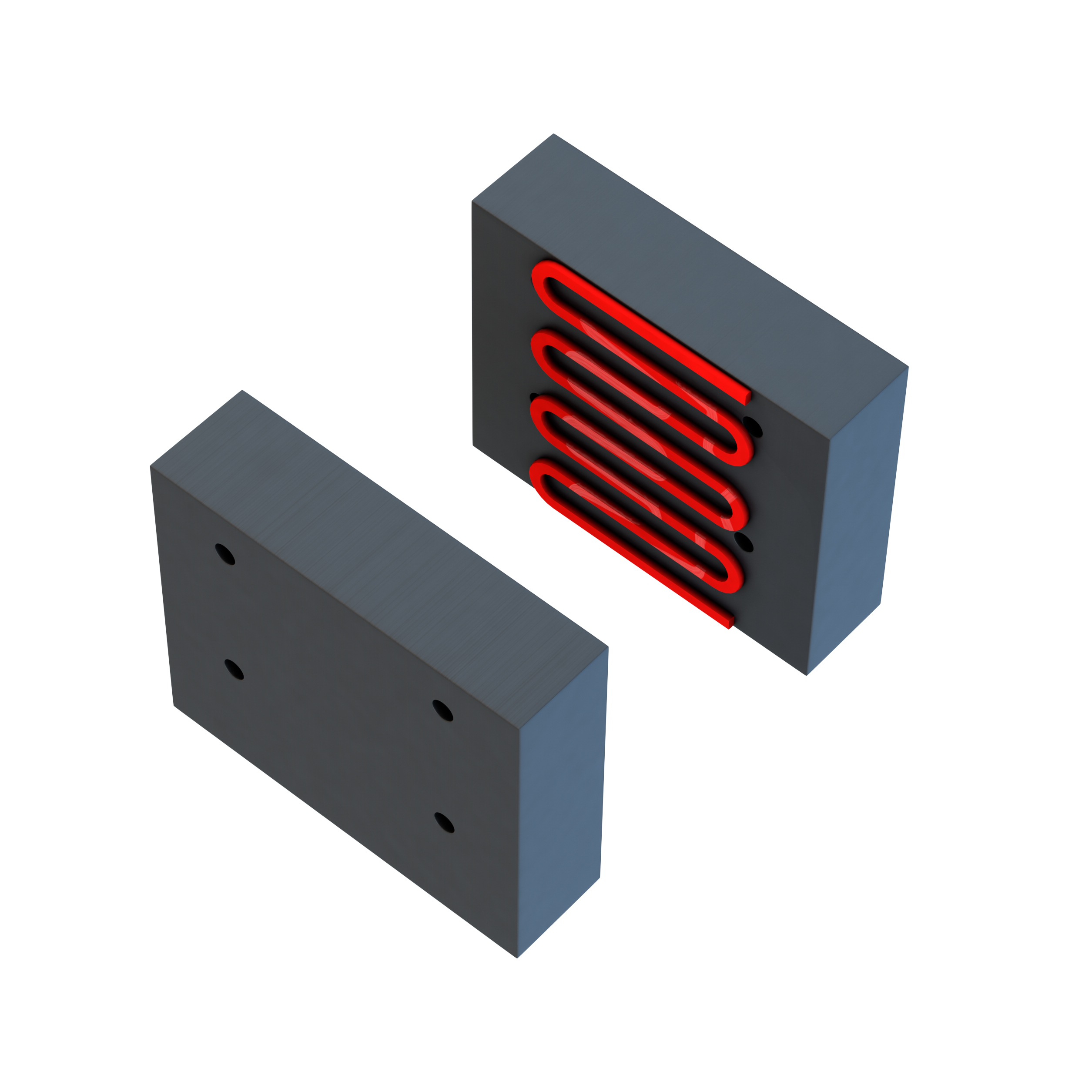
Die einzelnen Batteriezellen werden mit einem 2K-Klebstoff zu Zellstapeln gefügt (Bild: Atlas Copco)
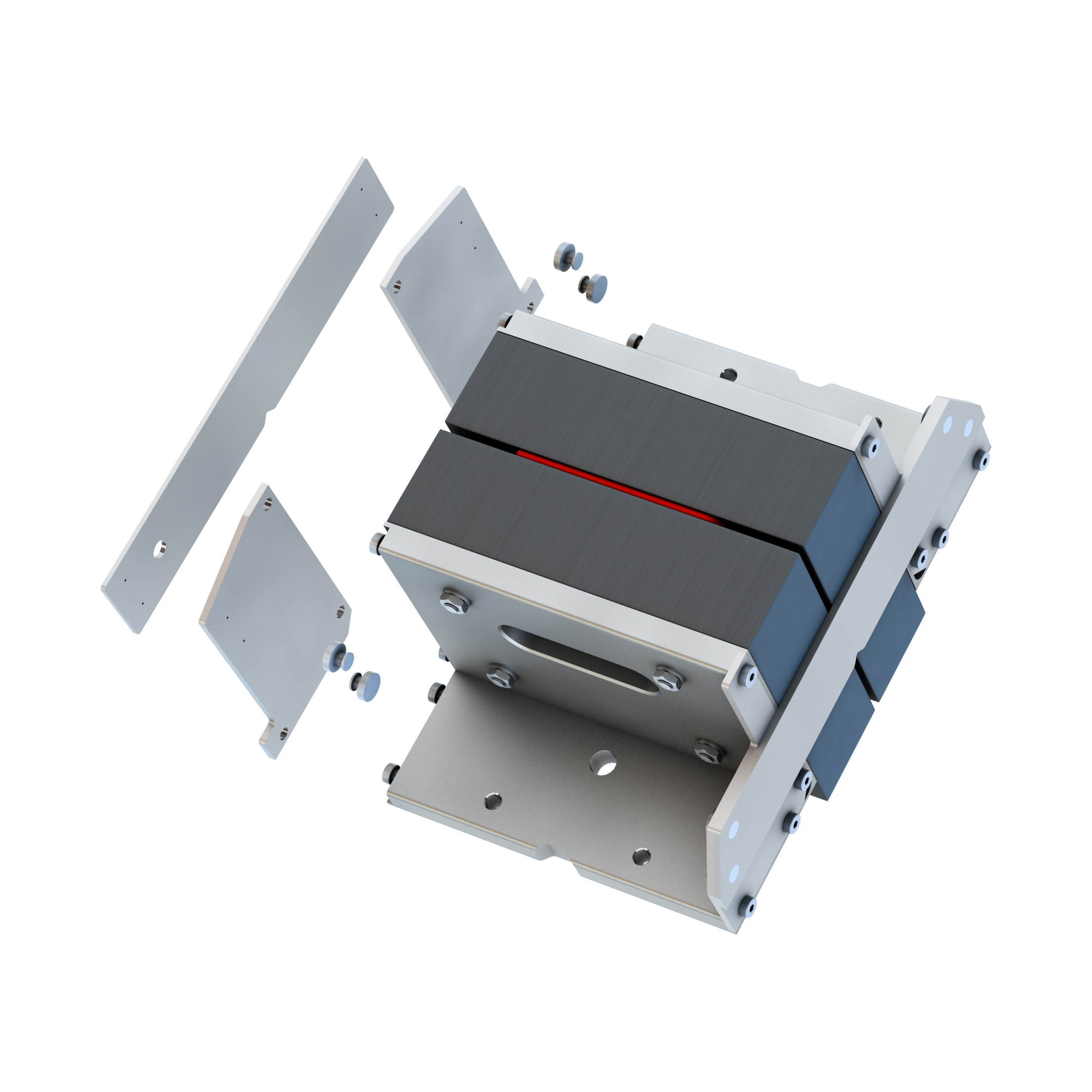
Befestigung seitlicher Streben mit Stanznieten (Bild: Atlas Copco)
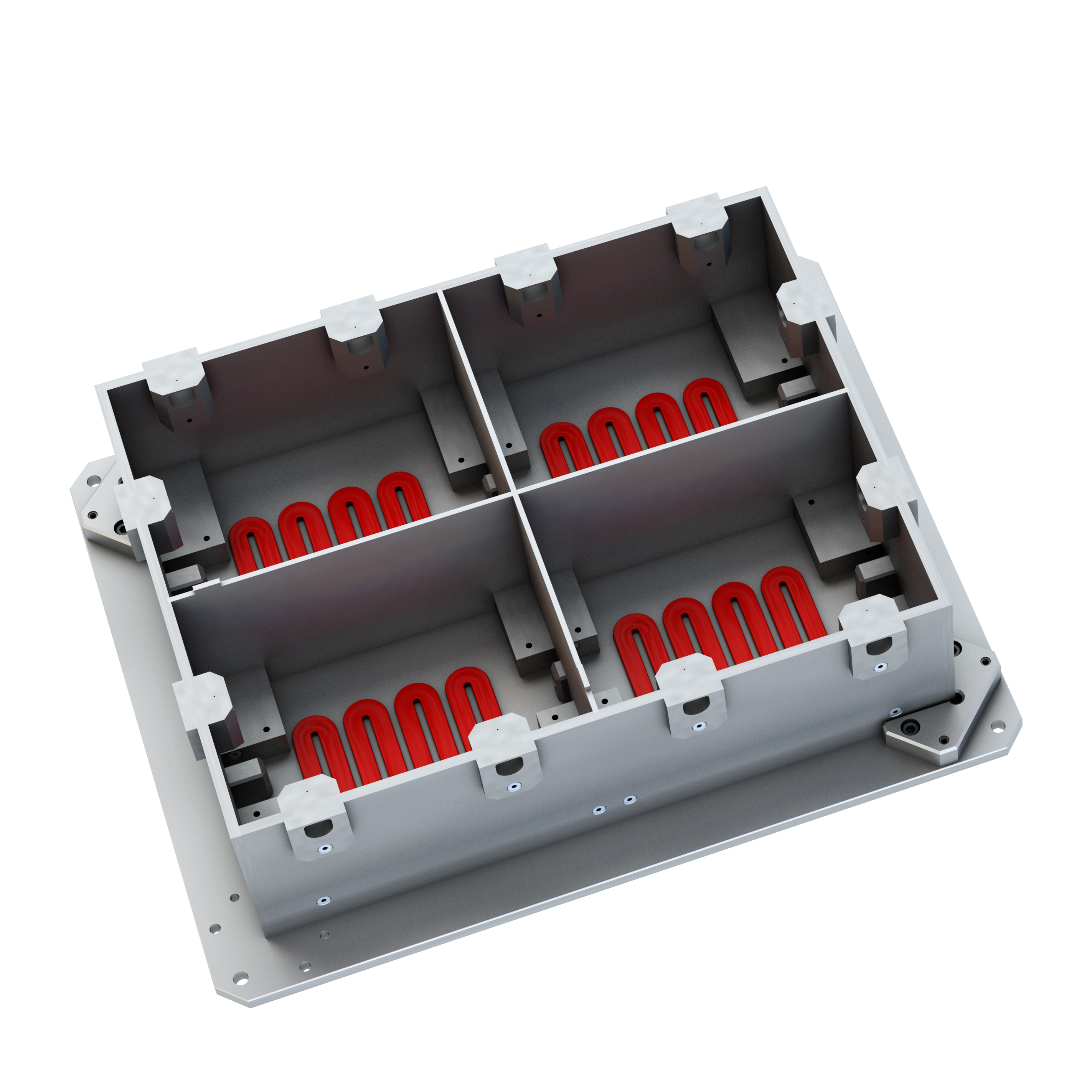
Die Wärmeleitpaste wird eingebracht (Bild: Atlas Copco)
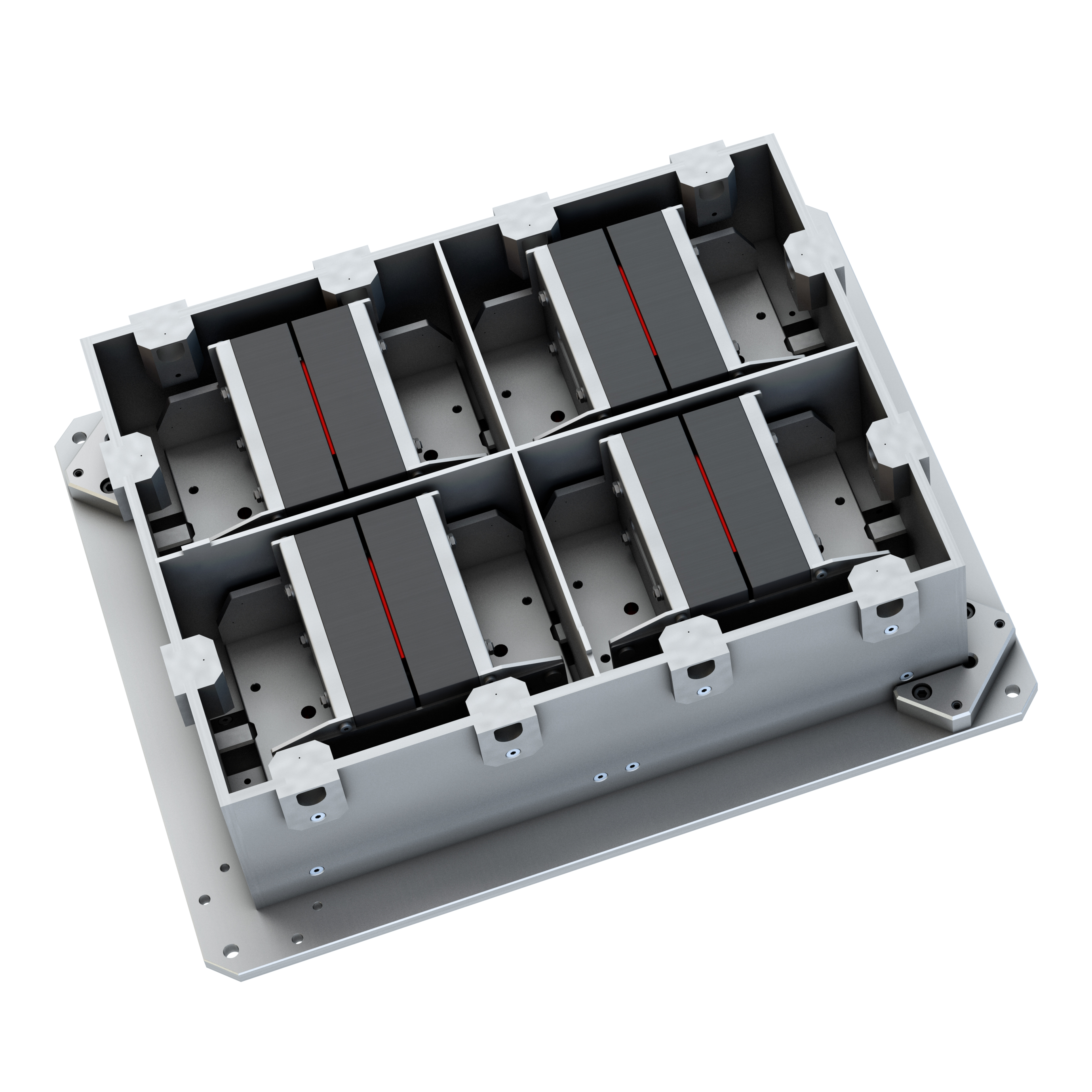
Die Module werden mit einem Vierfach-Schraubsystem in dem Gehäuse fixiert (Bild: Atlas Copco)
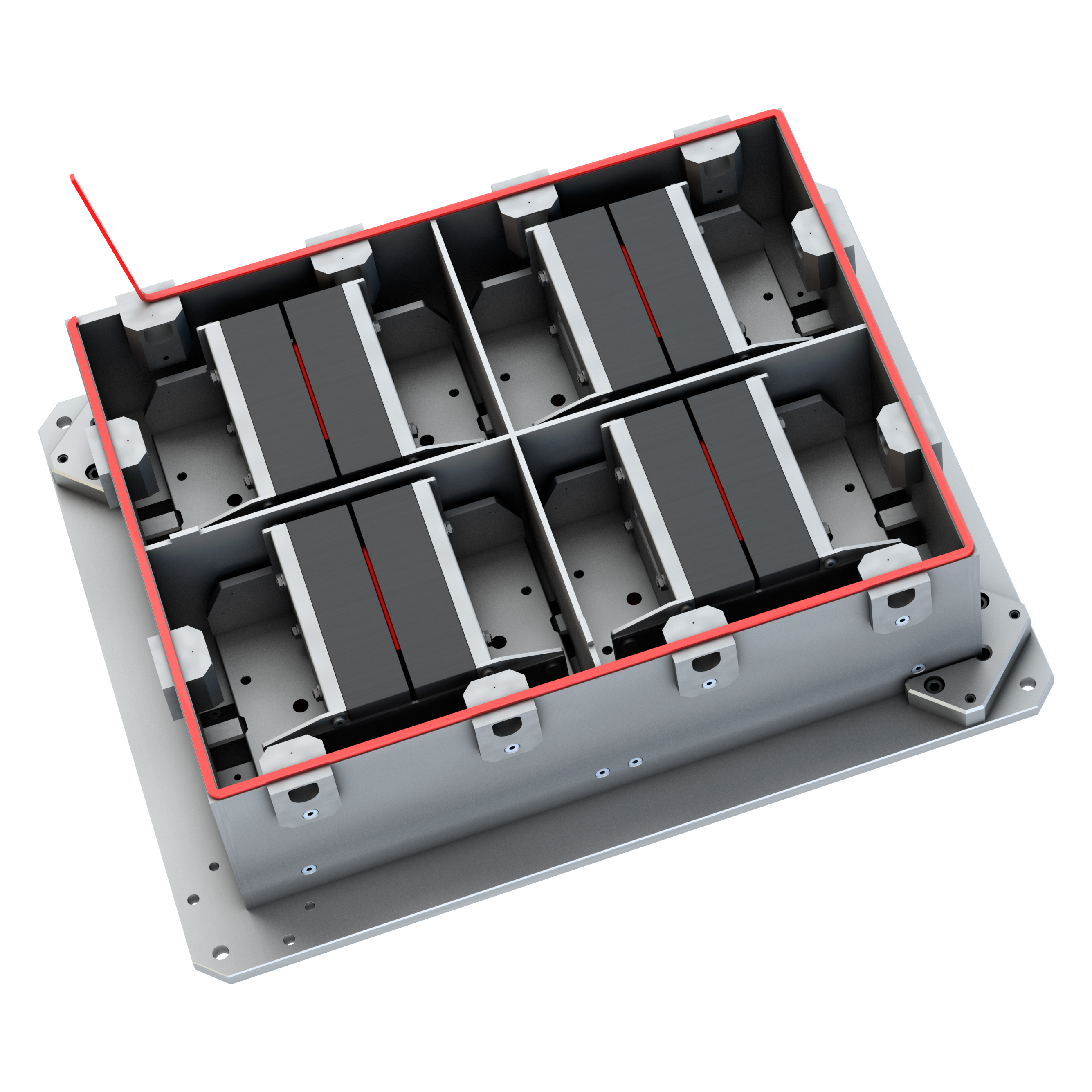
Applikation einer Flüssigdichtung (Bild: Atlas Copco)
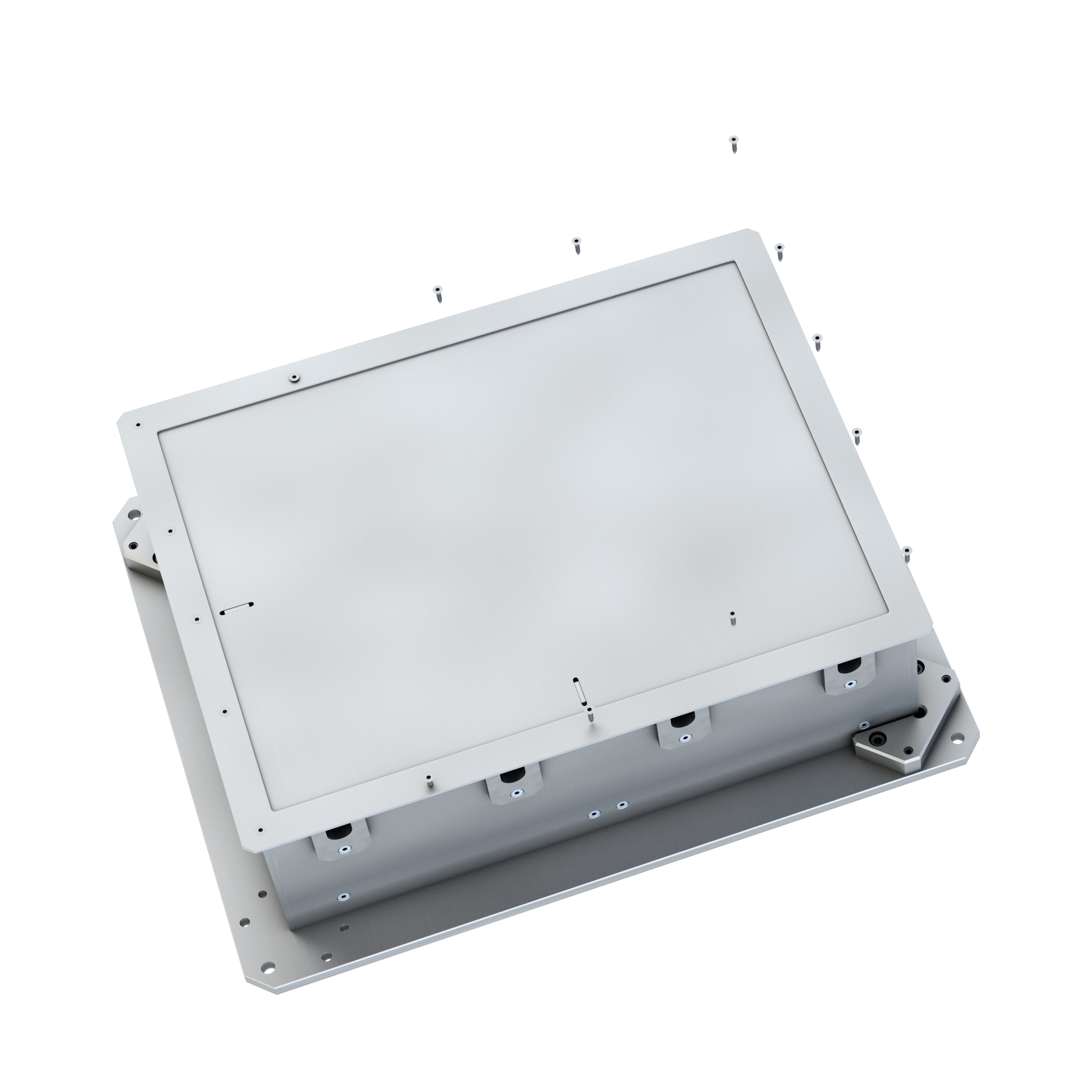
Deckelmontage mit Fließlochschrauben (Bild: Atlas Copco)