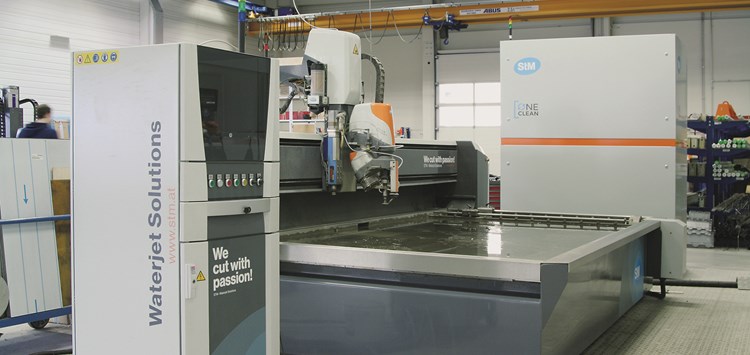
Modernes Wasserstrahlschneidesystem mit OneClean-Modul (Bild: STM Stein-Moser GmbH)
01.11.2018 Nachhaltig Dichtungen fertigen
Moderne Wasserstrahl-Schneidsysteme erfüllen viele Kriterien
Nachhaltigkeit ist in den letzten Jahren zwar als Modewort etwas überstrapaziert worden. Im Bereich der Wasserstrahltechnologie trifft dieser Begriff aber im Kern für viele Entwicklungen zu. Denn diese Technologie bietet nicht nur interessante ökologische Aspekte, ihr Einsatz kann auch zur nachhaltigen Unternehmensentwicklung beitragen.
Ressourcen sparen, energieeffizient produzieren – diese Anforderungen stehen heute quasi in jedem Pflichtenheft von Dichtungsherstellern. Auch deshalb, weil viele der heute produzierten Dichtungen helfen, Ressourcen zu sparen und Maschinen und Anlagen energieeffizient zu betreiben. Moderne Wasserstrahl-Schneidsysteme (Bild 1) bieten aufgrund ihrer modularen Bauweise viele Ansätze, Nachhaltigkeit ökologisch umzusetzen.
Abrasiv Recycling
Ein Ansatz ist die vollautomatische Wiederaufbereitung von Abrasivsand. Wasserstrahl-Schneidanlagen benötigen für den laufenden Betrieb Wasser und eben Abrasivsand. Letzterer ist der größte variable Kostenfaktor beim Wasserstrahlschneiden und eine knappe Ressource. Hier setzt das OneClean-System (Bild 2) an. Das Abrasiv-Recycling-Modul dieses Systems ermöglicht es, mehr als die Hälfte des Granatsandes für weitere Schneidaufträge zu recyceln. Das spart Beschaffungs-, Entsorgungs- und Transportkosten, die bei ca. 50 t Abrasiv-Verbrauch pro Jahr eine Amortisierung der Anschaffung innerhalb von ca. drei bis fünf Jahren möglich machen.
Die Recycling-Technologie funktioniert so: Ein spezifischer Hydrofilter sondert über ein patentiertes Verfahren Grob- und Feinteile aus dem gebrauchten Abrasiv in den Auffangbehälter des Basismoduls ab, wobei zu grobe und zu feine Bestandteile ausgeschieden werden. Das Gebrauchtabrasiv wird energieeffizient getrocknet und automatisch mit neuem Abrasiv aus dem Abrasivbehälter vermischt, um eine stabil hohe Abrasivqualität sicherzustellen. Mit diesem System sind – je nach Qualität und Schneidgeschwindigkeit – bis zu 55% des gebrauchten Abrasivs wiederverwendbar. Der benötigte Energieaufwand für die Wiederaufbereitung des Abrasivs ist mit 3 bis 6 kW minimal. Die Schnittqualität bleibt im Vergleich zu neuem Abrasiv gleich. Das Abrasiv Recycling ist eines von fünf zueinander in Beziehung stehenden Modulen des OneClean-Systems. Die Anlage kann also mit einem kleinen Investment in Betrieb gesetzt und nach Bedarf jederzeit erweitert werden.