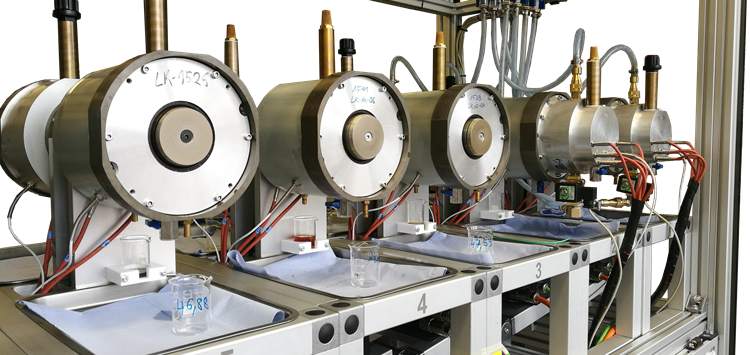
Modular test rig for endurance test runs (Bild: IMA)
29.09.2021 Improving a Gear Box Sealing System
Individual Test Design Based on Given Application Parameters and Failure Analysis
In the event of damage to sealing systems, expert knowledge in dealing with these problems is often not available to many industrial users. The development engineer is faced with the question of improving the product to meet the new requirements. The aim of this publication is to provide a proven guide for dealing with problematic sealing systems.
Elastomeric radial lip seals are used to seal shaft interfaces in all industrial applications and especially in the automotive sector. They are available at the market in different sizes and designs, as well as in different materials. Typical elastomeric materials are FKM (fluorelastomer) and NBR (nitrile rubber). In addition to individual, application-related designs, DIN 3760/ 3761 [1, 2] specifies a number of standards. Figure 1 shows the cross-section of a standard radial lip seals according DIN 3760 form A at the top and a pressure stable profile with a protective lip (dust lip) at the bottom. The sealing system always consist of the elastomeric sealing ring themselves, the fluid to be sealed and the sealing counterface (shaft). This paper describes a typical process in sealing technology, which often starts from a failure and/or an optimization request. The process aims on finding the root cause of the failure and optimising a given sealing system. The procedure is illustrated by means of a real failure from the beginning of the failure analysis through the optimization process to the solution (Figure 2).
The first step in this process is a comprehensive failure analysis to evaluate the root cause of the failure. The second step is an empirical system examination. A test run is developed to recreate the failure on the test rig. As soon as there is a reliable test run available, the optimization process can start in the third step. On the test rig, different types of seals can be tested fast and scientifically. So, the best sealing system can be chosen for the product. This procedure is working both, for the development of new product, as well as in the course of a product care in a running series. Example for illustrating the procedure is a vehicle gearbox sealing system. As these are ongoing cooperations, the manufacturer of the gearbox, and the manufacturer of the radial lip seals deliberately remain anonymous.